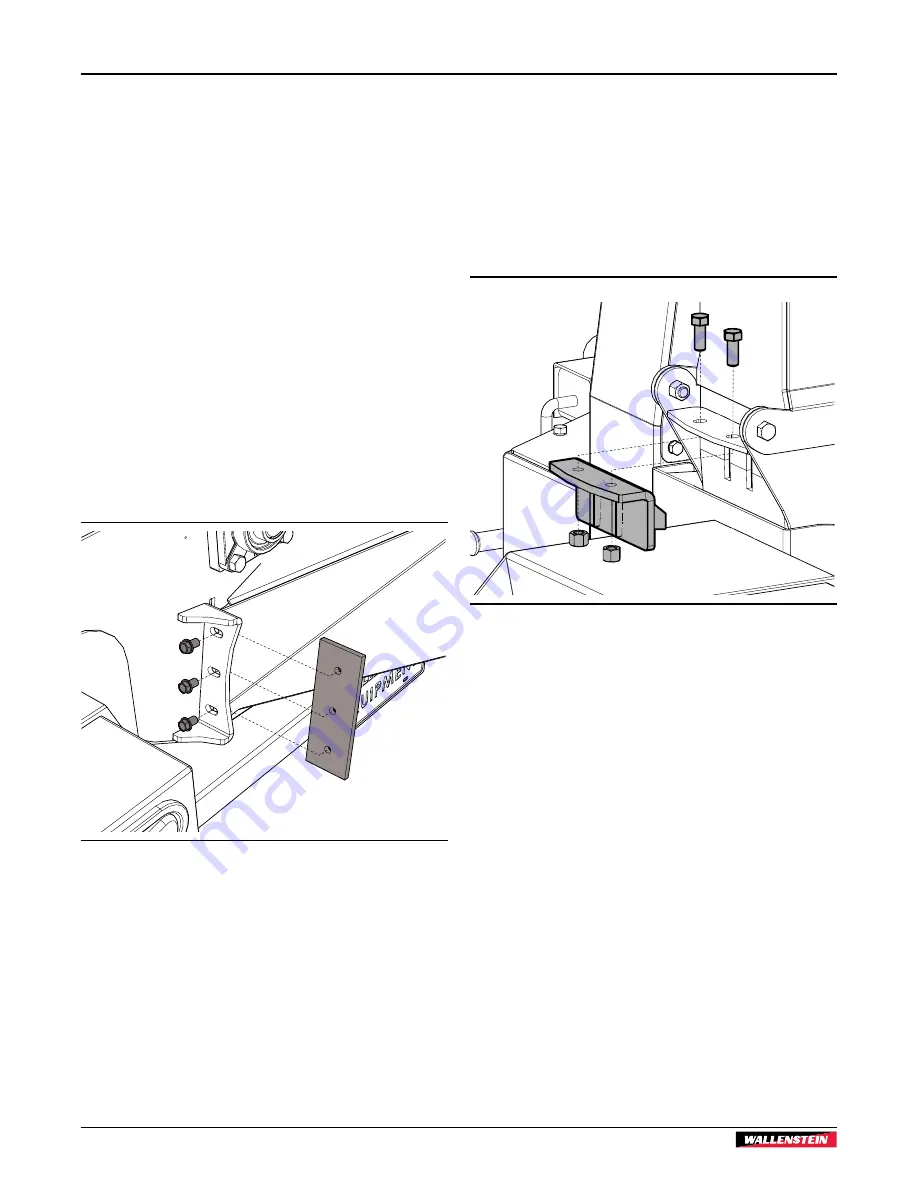
Service and Maintenance
BXTR6438
Trailer Wood Chipper
58
6.13 Ledger Knife
Each machine is equipped with a ledger (stationary) blade that
acts as a shear for the moving rotor blades.
The ledger blade is designed with four usable corners. When
the corner facing the rotor blade rounds over, remove the blade
and re-install with a different corner facing the rotor blade.
It is recommended that the clearance between the rotor and
stationary blades be set and maintained at 1/32–1/16" (3/4 –
1-1/2 mm) to obtain the best performance.
Make sure the engine is off (ignition switch is off).
1.
Remove the two bolts that hold the ledger blade to the
ledger mount, then remove the blade.
2.
Rotate the blade and replace, or swap with new or
re-sharpened blade.
3.
Hand tighten the bolts and set the clearance between the
ledger and rotor blades at 1/32–1/16" (3/4 – 1-1/2 mm).
For fast and easy setting, use the chipper Clearance Setting
Gauge, available from your dealer.
4.
Tighten down bolts.
01593
Fig. 53 –
Ledger Knife
6.14 Twig Breaker
The Twig Breaker is a breaker tab located on side of the lower
rotor housing. As the discharge paddles pass, the twig breaker
helps to break the material into smaller pieces and turn it into
mulch.
Inspect the twig breaker for damage such as gouges, a bent, or
missing tooth. A damaged twig breaker should be replaced. If
the tooth is showing wear, remove and replace.
01594
Fig. 54 –
Twig Breaker