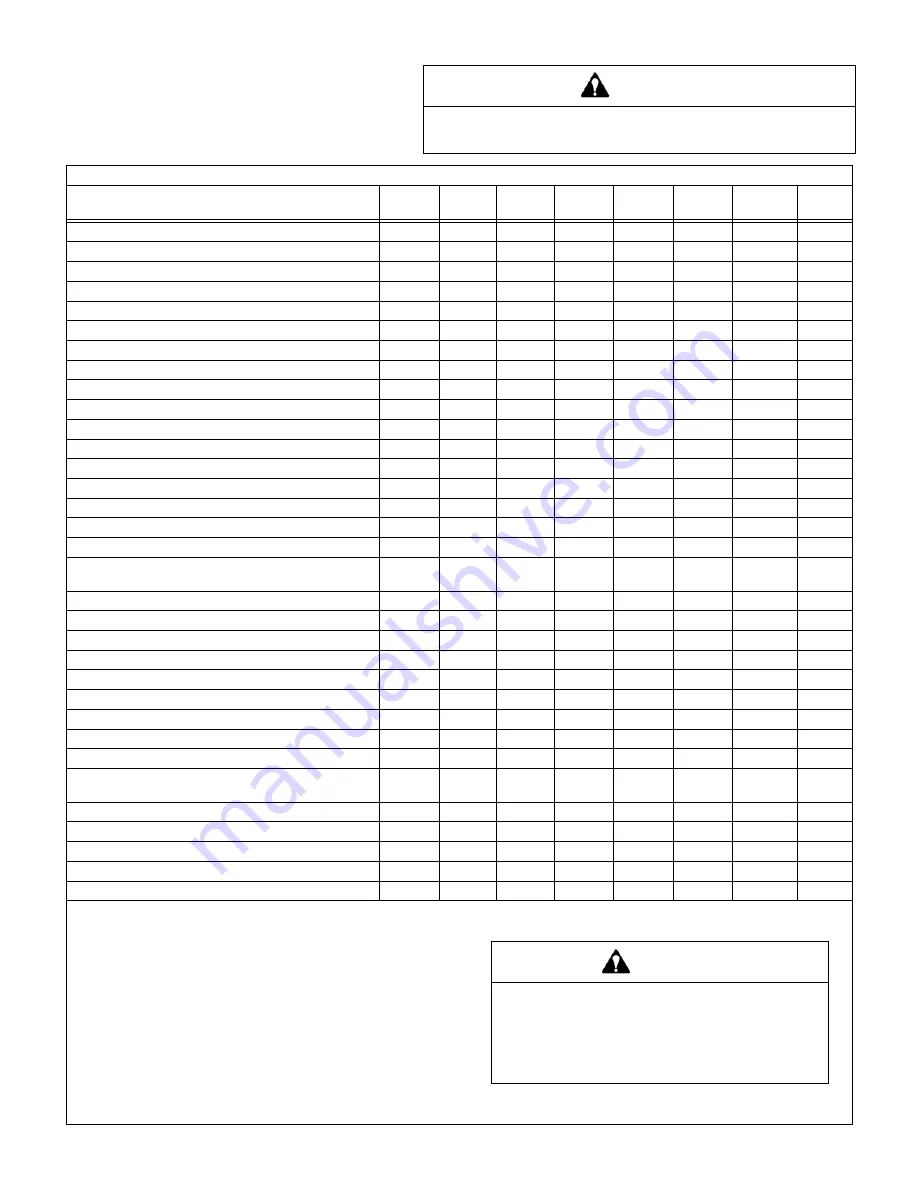
Maintenance Instructions
40
MAINTENANCE SCHEDULE CHART - RECOMMENDED SERVICE INTERVALS - MODEL MBS29
Service Item
Daily
25
Hours
100
Hours
200
Hours
400
Hours
Yearly
Every
2 Years
Ref.
Page
Check Engine Crankcase Oil Level
x
Check/Clean Engine Air Cooling System*
x
Check Air Filter Restriction Gauge
x
Clean Grass Buildup Under Deck
x
Service Mower Blades
x
Check Security of Air Filtration Components
x
Check Transaxle Housing Condition
x
Check Function of Warning Lights and Horn
x
Lubricate Grease Fittings and Oil Points*
x
Check Tire Pressure
x
Check Drive Belts (Engine/PTO, Ground Drive)
x
Check Operation of Safety Interlock Switches
x
Check Battery Electrolyte Level
x
Check Transaxle Oil Level (in Reservoir)
x
Change Engine Crankcase Oil**
x
Δ
Check Air Filter Element***
x
Clean Engine Cooling Fins
x
Check Security of Drive Tire
Mounting Nuts (75 to 85
lb·ft
)
x
Clean Transaxle Housing
x
Check FSC Friction Lock
x
Check Blade Brake Action
x
Check Operation of Turbine Precleaner Fan*
x
Change Engine Oil Filter
x
Check/Regap Spark Plugs
x
Replace Fuel Filter
x
Change Transaxle Oil and Filter
x
ΔΔ
Check Fuel Lines and Clamps
x
Replace Air Filter Element
and Dust Ejection Valve***
x
Service Battery
x
Service Solenoid Shift Starter
x
ΔΔΔ
Check PTO U-Joints for Wear/Looseness
x
Replace Fuel Lines and Clamps
x
Replace Ignition Wires
x
∗
More often in extremely dusty or dirty conditions
(Refer to notes about air cleaner element in
IMPORTANT TIPS FOR CARE OF THE
KOHLER ENGINE)
∗∗
Change engine oil and filter after first 8 hours
of operation of a new engine (break-in period)
∗∗∗
Air cleaner is remote mounted Cummins/Fleetguard
OptiAir™ unit, replace filter every year
Δ
Change oil every 50 hours when operating
in dry, dirty conditions
ΔΔ
Initial oil and filter change at 75100 hours
ΔΔΔ
See your Walker dealer for this service or refer to the
Walker Service Manual
CAUTION
When performing maintenance with the
tractor body raised, a safety prop should
be installed from back of body to chassis
frame (fail-safe protection in case of fail ure
of body lift support).
CAUTION
Maintenance procedures requiring special training or
tools should be performed by a trained technician.