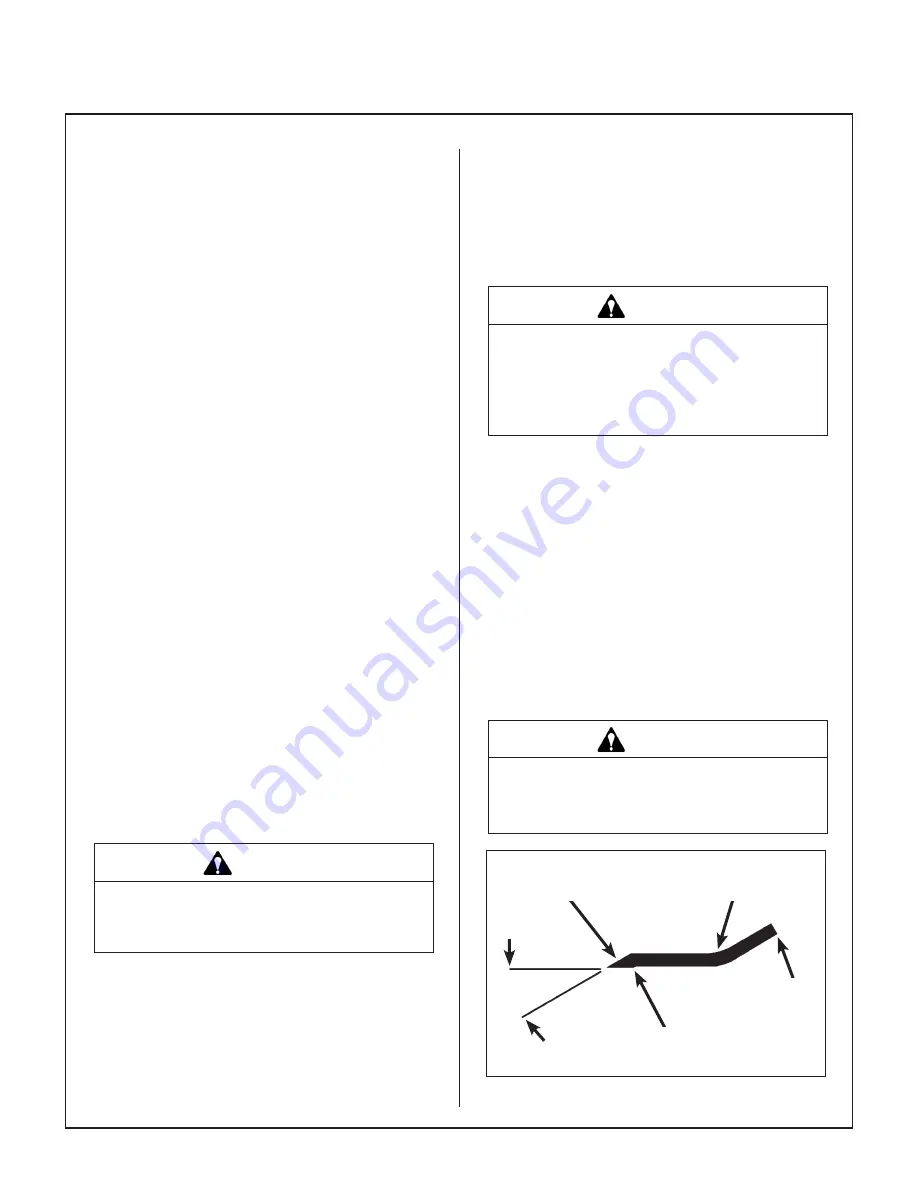
74
Maintenance Instructions
CHECKING/SERVICING
Tire Pressure
Inflate tires to pressures shown below:
Deck Caster Wheel* = 20 PSI (137 kPa)
Drive
= 15 PSI (103 kPa)
Tailwheel
= 20 PSI (137 kPa)
* If equipped with optional pneumatic tires
Wheel Bolt Torque
Check the eight (8) lug bolts that mount the drive
tires.
Every 100 hours
they should be torqued to
75 to 85 lb
·
ft (102 to 115 N
·
m).
Sharpen Mower Blades
Check mower blade(s) for
straightness, sharp-
ness, condition of
the cutting edge,
and
balance
every 10 hours
of operation (or more often when
mowing abrasive type grass or operating on sandy
soils).
Replace blades if worn, bent, cracked, or
otherwise damaged
(refer to
REPLACING/RE-
PAIRING
the
Mower Blades
in this section). Use
the following procedure to check and sharpen
blades:
NOTE: Keep blades sharp
- cutting with dull blades
not only yields a poor mowing job but slows the
cutting speed of the mower and causes extra wear
on the engine and blade drive by pulling hard.
1. Stop the engine, remove ignition key, and dis-
connect the spark plug wires
before
raising the
mower deck to service blades.
2. Raise the deck and
secure
it in the
TILT-UP
po sition. Refer to
CLEANING
the
Grass Build-
up in Mower Deck Housing
in this section for
deck rais ing instructions.
DANGER
NEVER operate cutter blades with the
deck in the raised position.
NOTE:
PTO shaft must be
disconnected
be-
fore checking blades for straightness.
3. Check the blades for
straightness
by marking
the blade tip position inside the deck housing,
and then rotating the opposite end of the blade
to the same position and comparing. If the dif-
ference in blade tip track is
more than 1/8 in.
(3 mm),
the blade is bent and
should be
re placed.
WARNING
DO NOT try to straighten a blade that is
bent. NEVER weld a broken or cracked
blade. ALWAYS replace with a new blade
to assure safety.
4. If the blade cutting edge is
dull or nicked,
it
should be sharpened. Remove blades for
sharpening by grasping the end of the blade us-
ing a rag or a thick, padded glove, while loosen-
ing and removing the nut, lock washer, and flat
washer that mounts the blade.
5. Grind cutting edge at the same bevel as the
original. Sharpen only the top of the cutting
edge to maintain sharpness.
NOTE:
Blades can be sharpened with an
electric blade sharpener, conventional electric
grinder, or a hand file.
CAUTION
ALWAYS wear eye protection and gloves
when sharpening a blade.
Wing
Tip
Do Not Grind or
Sharpen on Underside
Intersection
Wear Area
Sharpen at
Original 30° Angle
30°
Mower Blade Profile for Sharpening