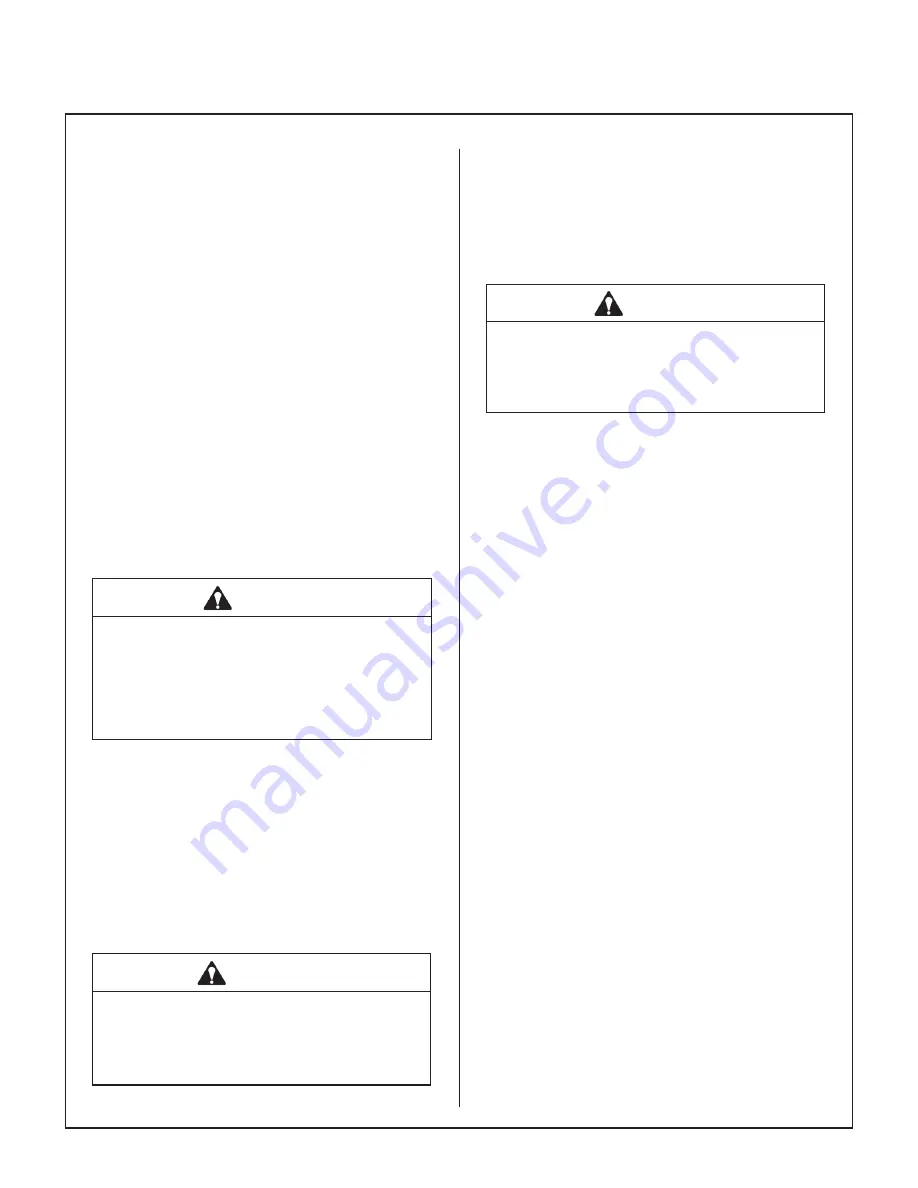
B27i
Maintenance Instructions
Replacing and Repairing
63
Mower Blades
Mower blades are removed and remounted as
described in
Sharpen Mower Blades on page
56
. During the course of sharpening and
inspecting mower blades, if there are
any of the
following conditions of wear or damage, blades
should be replaced
for reasons of safety and
performance of the machine:
● An excessive amount of the
flat section
of the
blade has been
ground away
(removed) when
the blade is sharpened. Replace the blade
when less than a 3/4 in. (19 mm) flat section
remains
at the blade tip.
● Examine ends of the blade carefully, especially
the intersection where the flat section of the
blade turns up to form the “wing tip” (refer to
the illustration
Mower Blade Profile for Sharp
-
ening on page 57
for location of the wing tip
and wear area). Since sand and abrasive
material can wear metal away in this area, the
blade should be
replaced when metal thick-
ness has worn to 1/16 in. (1.6 mm) or less
.
DANGER
When blades are operated over sandy soil,
and if blades are allowed to wear, a “slot”
may be worn into the wing tip of blade.
Eventually a piece of the blade may break
off creating a serious potential for injury or
damage.
● Check the blades for
straightness
by marking
blade tip position inside the deck housing and
then rotating the opposite end of the blade to
the same position and comparing. If the differ-
ence in blade tip track is
more than 1/8 in. (3
mm)
, the blade is bent and
should be
replaced
.
● Inspect the blade surface, especially in formed
areas, for
cracks
. Replace the blade if any
cracks are found.
WARNING
DO NOT try to straighten a blade that is
bent. NEVER weld a broken or cracked
blade. ALWAYS replace with a new blade
to assure safety.
Reinstall the blades following procedure from
Sharpen Mower Blades on page 56
. If blades
are replaced, always use
Walker original equip-
ment blades
to ensure safety and optimum perfor-
mance. The quality and performance of
replace-
ment blades offered by other manufacturers
cannot be guaranteed, they
could be dangerous.
CAUTION
ALWAYS use genuine factory replacement
parts. Substitute parts CAN result in prod-
uct malfunction and possible injury to the
operator.
Summary of Contents for B27i
Page 74: ...70 ...