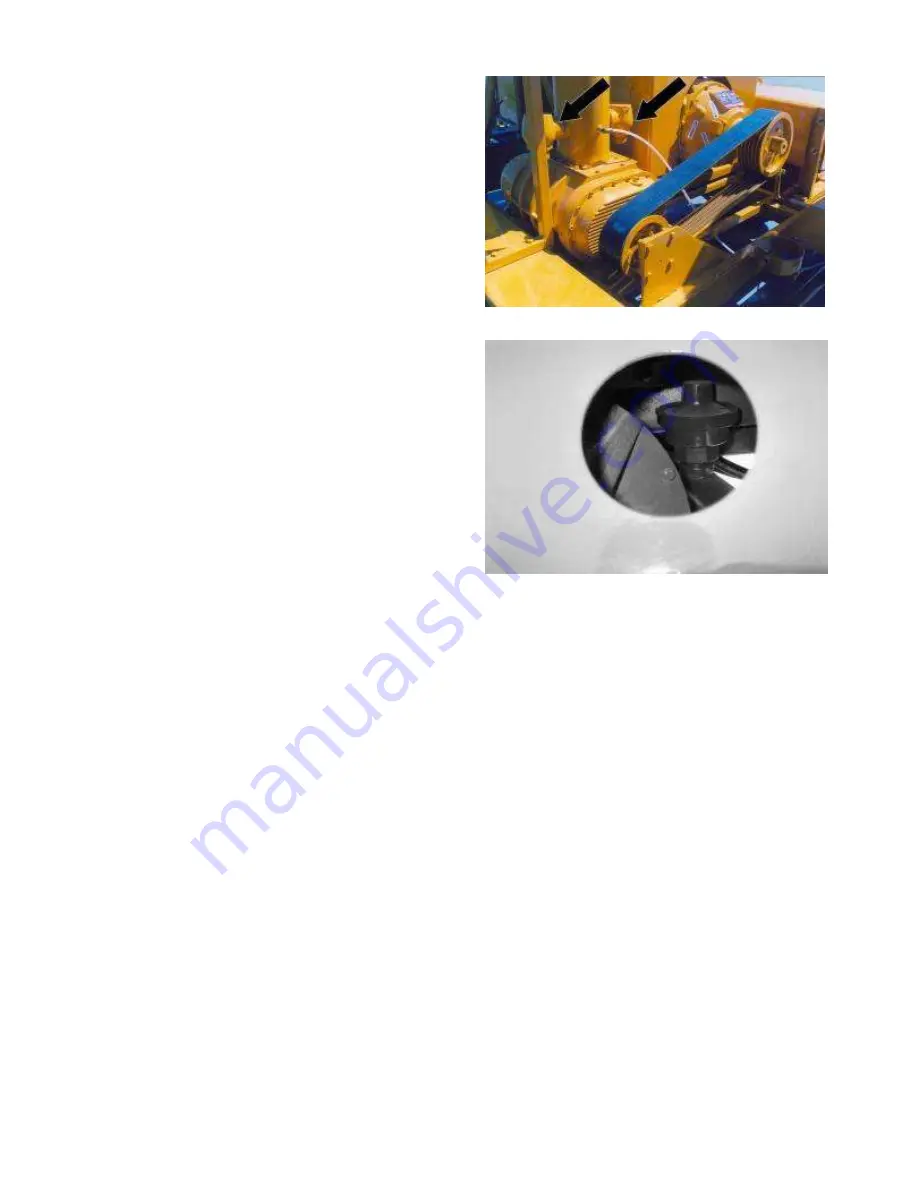
5.2.4 AIR SYSTEM RELIEF VALVES
The air in this system is moved by the blower. It
draws air into the intake side and creates a
vacuum that can pick up and draw material into
the system. As the air moves through the blower,
it becomes pressurized and flows through the
airlock to move material out of the system and to
its destination. As the flow into the intake is
restricted, the vacuum will build until it exceeds the
setting of the intake relief valve. The valve opens
to supply a flow of air to the blower to prevent
overheating. A relief valve on the pressure side
will also open to allow air flow if the airlock (outlet
pressure side of the circuit) is restricted or
plugged.
The vacuum side relief valve is set to open at 15
in. Hg vacuum and the pressure side at 15 psi.
Both must function at very close to these specified
levels to insure optimum capacity and
performance. After prolonged use, the springs in
these valves can weaken causing the valve to
open prematurely and affect machine
performance. Dirt and debris can get caught in the
valve seat allowing air leakage that affects system
performance.
To maintain air system relief valves, follow this
procedure:
1. Listen for the valves opening during operation.
They will sound like a popping or a whistle if
they are opening.
2. Install gauges on the vacuum and pressure
sides of the air system.
3. Watch the gauges to monitor the pressure in
the vacuum and pressure sides of the air
circuit.
4. Restrict the flow into the intake side of the air
system until you hear the valve open. The
vacuum gauge should read 15 in. Hg. If it
does not, replace valve.
5. Restrict the output side until you hear the
valve open. The pressure gauge should read
15 psi. If it does not, replace the valve.
6. Place all controls in neutral or OFF, stop
engine, remove ignition key and wait for all
moving parts to stop.
7. Remove old valve and replace it with a new
one.
8. Tighten valve into fitting to secure.
Fig. 5-19 Vacuum Relief Valves
Fig. 5-20 Pressure Relief Valve