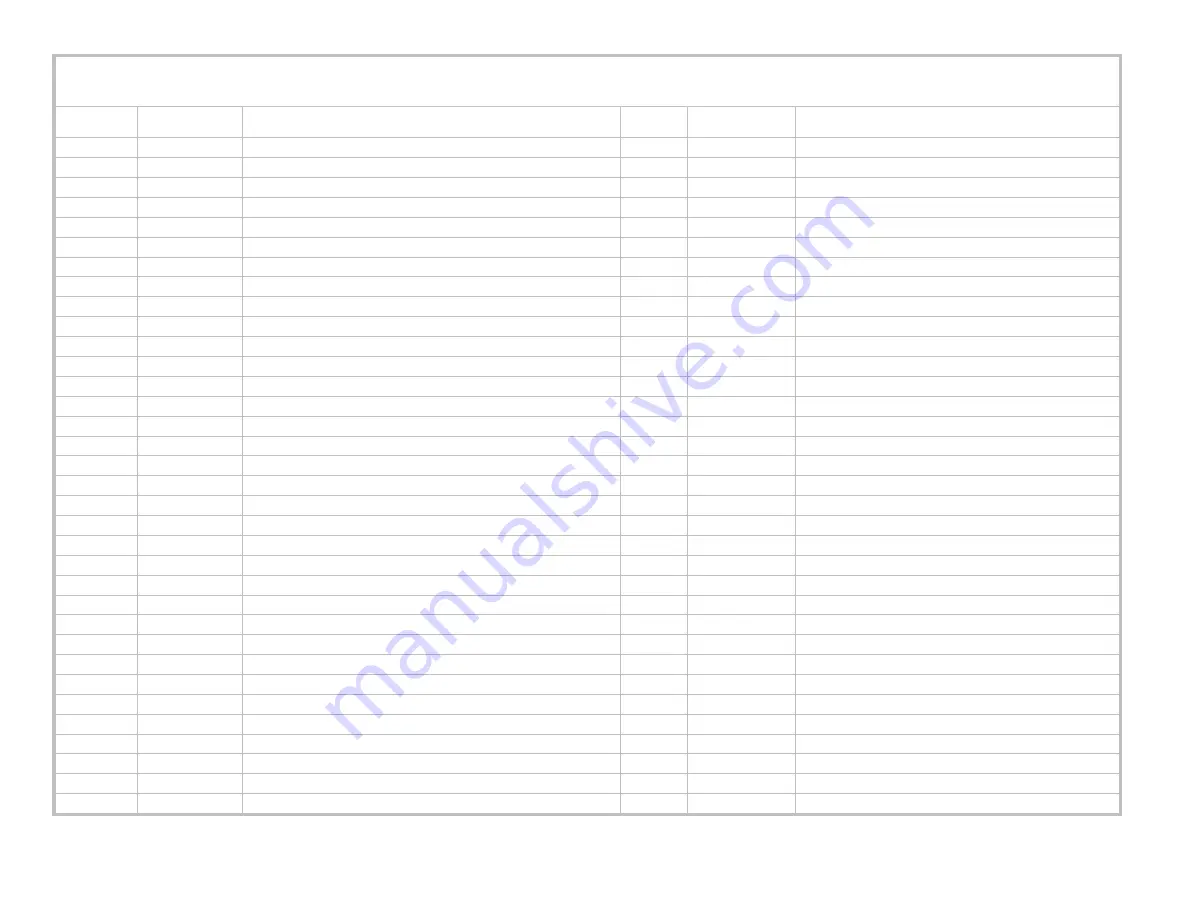
Agri-Vac Operator’s Manual 34-18148-6
86
7614 DLX HBR FRL 2016 PARTS LIST
(see fig. 8-7)
ITEM
NUMBER
DESCRIPTION
ITEM
NUMBER
DESCRIPTION
1
11-03632-6
Jack Topwind Plated LW5000-13TWPM
35
11-88803-4
Liner,Frustum,Full,Receiver,7614,HD,11
2
11-03729-6
1/8" Clear Polycarbonate 5 X 7
36
11-93971-5
Belt Cover Assembly,Bolt,2014
3
11-09219-4
Holder For DM6
37
11-94013-5
Midship Shaft/Pump Assembly,16 long
4
11-104842-4
Liner,Body,Receiver,7614,DI,SH,2016
38
11-94283-5
A/L In Elbow Installation,7614,HD,2014
5
11-104853-4
Liner,Body,Receiver,7614,DI,Long,2016
39
11-94286-5
Muffler Installation,7614,HD,Test 15
6
11-104860-5
Receiver Assembly,7614,DI,FRL,W/PC,HD,2016
40
11-94433-4
MSS,1-3/4X6B,SCH,1.75x16
7
11-14047-6
V-Belt, 5VX1000
41
11-94771-6
Sheave, 8.0 X 5-5V X E
8
11-15577-6
Sheave, 23.6 X 5-5V X F
42
11-94953-4
Shaft,1-1/2,1-3/8 21T SPL13.369G
9
11-16687-6
Tire/Rim Assembly P205/70R15, White Rim
43
11-94964-4
Belt Cover Bolt Down,Vibration Mount
10
11-17572-6
Cylinder Hydraulic 2 X 8"
44
11-95981-5
Flange Reinforce Assembly,7614HD,2011
11
11-17602-6
Bushing, F X 1-3/4" X 3/8"KW
45
11-96501-5
Lower Boom Installation,7614,HBR,HD,2014
12
11-28489-4
Holder For DM7
46
11-96504-5
Boom Swivel Top Installation,7614,2014
13
11-36336-4
Pump Bracket, SCH
47
11-96509-5
Hose Holder Assembly,7614,Rear,2014
14
11-36513-5
Lower Boom Elbow Assembly-7"-40 Degree
48
11-96510-5
Hose Holder Assembly,7614,Front,2014
15
11-39927-4
Liner Frustrum Bolted Cyclone
49
11-96519-4
Boom Flex Hose Sup,66/7614,2014
16
11-59650-4
Fender, Bolt-On
50
28-08918-6
T-Bolt Clamp, 6-1/2",C410C-75-650-S
17
11-64301-5
Hub/Spindle Installation
51
28-16829-6
T-Bolt Clamp, 8-1/2",C410C-75-850-S
18
11-66272-5
Acceleration Hose Installation, 7"
52
30-77779-5
A/L 2018-7a HXS, W/O Motor
19
11-69555-5
Blower Inlet Installation-6614/7614-2010
53
36-16581-6
Flex Hose, SF400 7"X45",Compressed
20
11-70231-6
Drive Shaft, Double Center, 35EBL
54
38-28480-5
DP-7 Plug With Chain
21
11-71116-4
Blower Drive Shaft Guard, Top
55
38-29560-4
614-6 Blower Outlet - Mach
22
11-71119-4
Hydr Tank Mounting Bracket-Top Plate-2010
56
38-73887-5
Hose Holder Assembly-Corner
23
11-72055-4
Hour Meter Pickup Sensor Bracket
57
39-00724-6
Pressure Relief Valve,2",15 PSI
24
11-72773-5
A/L Outlet Installation,7614,2011,HD
58
39-73882-6
Vacuum Relief Valve 3", 16 HG
25
11-72774-5
A/L Outlet Assembly,7614,2011,HD
59
50-69733-5
Blower, 614, Chrome, 2.25"
26
11-73133-5
Hydraulic Tank Installation-SCH-Painted-2010
60
54-80552-6
PLP 20-14-S0-49S1-LOD/OC-N
27
11-75298-5
Cyclone 7" FRL-Left Inlet-2011
61
73-82074-6
Connection Hose 6" Diameter - 10 Long
28
11-75302-5
Split Boom End-Tube Assembly-7-2011
62
96-03623-6
Bearing, Pb, 1-3/4", HCP209-28
29
11-75320-4
Cyclone 7" FRL-Left Inlet-Liner Body
63
96-04567-6
Bearing, 4bolt, 1-1/2", SF 1 1/2
30
11-75321-4
Cyclone 7" FRL-Left Inlet-Liner Top
64
96-09117-6
Gasket, Blower Mount, 614
31
11-76429-4
Bearing Support Plate, 66 / 7614, 2011
65
96-19215-6
Locking Collar Eccentric 3/4"
32
11-82219-6
Hump Hose, Rubber, 8"
66
96-37629-6
Gasket 10-6-J
33
11-82616-6
Tach/Hour Meter
67
97-80192-6
Key, 3/8 X 3/8 X 1-3/4" Long
34
11-85175-6
Bushing, E X 1-1/2" X 3/8KW
Summary of Contents for AGRI-VAC 5614
Page 2: ......
Page 74: ...Agri Vac Operator s Manual 34 18148 6 72 NOTES...
Page 77: ...Agri Vac Operator s Manual 34 18148 6 75 Fig 8 1 Exploded View 5614 DLX HBR FRL SCH DI...
Page 79: ...Agri Vac Operator s Manual 34 18148 6 77 Fig 8 2 Exploded View 6614 DLX HBR FRL SCH DI...
Page 81: ...Agri Vac Operator s Manual 34 18148 6 79 Fig 8 3 Exploded View 7614HD DLX HBR FRL SCH DI...
Page 82: ...NOTES...
Page 85: ...Agri Vac Operator s Manual 34 18148 6 83 Fig 8 5 Exploded View 5614 DLX HBR FRL 2016...
Page 87: ...Agri Vac Operator s Manual 34 18148 6 85 Fig 8 6 Exploded View 6614 DLX HBR FRL 2016...
Page 89: ...Agri Vac Operator s Manual 34 18148 6 87 Fig 8 7 Exploded View 7614 DLX HBR FRL 2016...
Page 91: ...Agri Vac Operator s Manual 34 18148 6 89 Fig 8 8 Exploded View 7816 DLX HBR FRL 2016...
Page 92: ...NOTES...
Page 93: ......