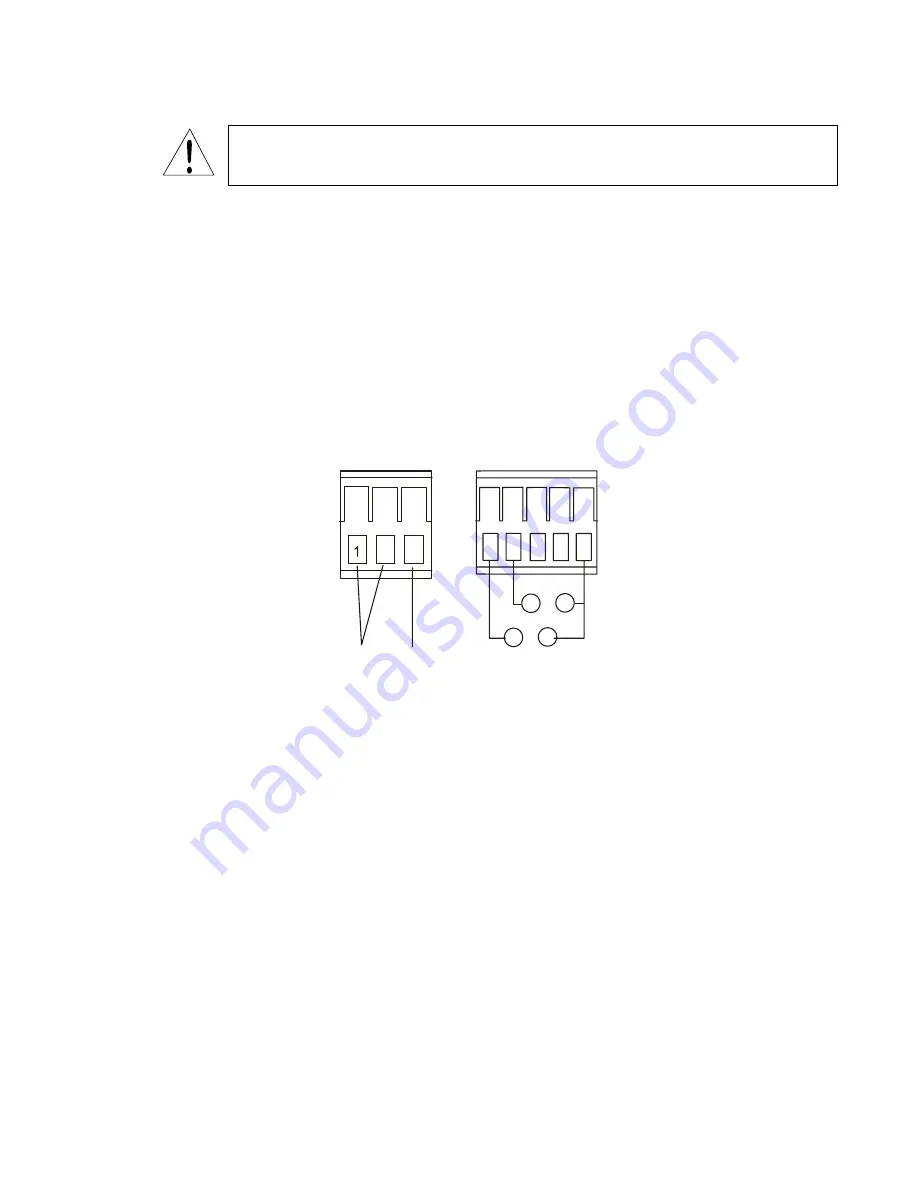
Analog Mode
CAUTION:
Open loop signal voltage must not exceed 25 VDC. If the signal voltage is
greater than 25 VDC, power down the signal source prior to connection.
In analog mode the pump will accept a milliamp signal and produce a pump speed
proportional to the signal level received. The input resistance of the analog signal is
250
Ω
. The pump’s response can be fine tuned by variable set points to meet system
requirements.
Connecting an analog signal device
Disconnect AC power to the pump. Remove the four screws from the terminal block cover
and remove the cover. Remove the cord nut and bushing from the terminal block cover.
Remove the terminal block from the connector. Slide the nut and bushing over the
external control cable and insert the cable through the terminal block cover. Strip 1/4”
insulation from conductors and connect the positive side to terminal 5 and the negative
side to terminal 8. (See Figure 8 and the schematic below.)
4
2
3
5
6
7
8
Power Ground
Analog Input
Sensor Power
DC 12V
10 mA max.
+
-
White
NEU
Black
HOT
Green
+
-
Settings
The pump’s response to a 4 to 20 milliampere signal can be adjusted to meet almost any
need. The adjustment is done by selecting two points. A signal level and a pump speed
are entered for each point. These two points determine a straight line and the pump speed
resulting from any given signal will be defined by that line. The factory settings for point
1 are 4.0 mA, 0 spm and for point 2 are 20.0 mA, 360 spm. An ‘
A
’ in the leftmost
position of the display indicates the data shown is
A
nalog signal level. A ‘
P
’ indicates
P
ump speed. The 1 on the right side of the display is highlighted when viewing or
changing data for point 1. The 2 is highlighted to indicate data for point 2.
Start with pump in the
WAIT
state. If it is not currently in wait, press
START/STOP
once.
15