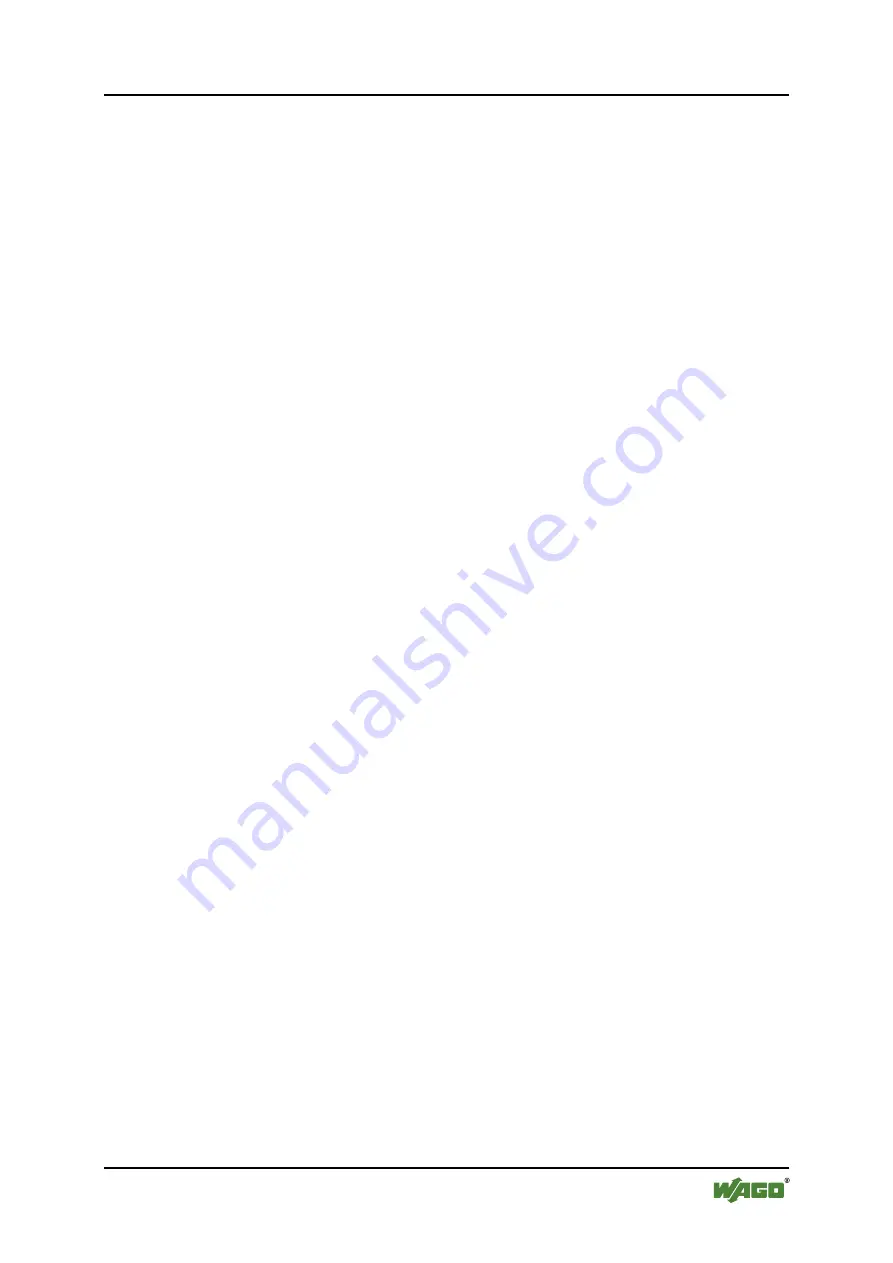
WAGO-I/O-SYSTEM 750
Use in Hazardous Environments
71
750-652 Serial Interface RS-232 / RS-485
Manual
Version 1.4.0
10.2.4 Special Conditions for Safe Use
(IEC-Ex Certificate IECEx TUN 12.0039 X)
1.
For use as Gc- or Dc-apparatus (in zone 2 or 22) the Field bus independent
I/O Modules WAGO-I/O-SYSTEM 750-*** Ex i shall be erected in an
enclosure that fulfils the requirements of the applicable standards (see the
marking) IEC 60079-0, IEC 60079-11, IEC 60079-15, IEC 60079-31.
For use as group I electrical apparatus M2 the apparatus shall be erected in
an enclosure that ensures a sufficient protection according to IEC 60079-0
and IEC 60079-1 and the degree of protection IP64.
The compliance of these requirements and the correct installation into an
enclosure or a control cabinet of the devices shall be certified by an ExCB.
2.
Measures have to be taken outside of the device that the rating voltage is not
being exceeded of more than 40 % because of transient disturbances.
3.
The connecting and disconnecting of the non-intrinsically safe circuits is
only permitted during installation, for maintenance or for repair purposes.
The temporal coincidence of explosion hazardous atmosphere and
installation, maintenance resp. repair purposes shall be excluded.
4.
For the type the following shall be considered: The Interface circuits shall
be limited to overvoltage category I/II/III (non mains/mains circuits) as
defined in IEC 60664-1.