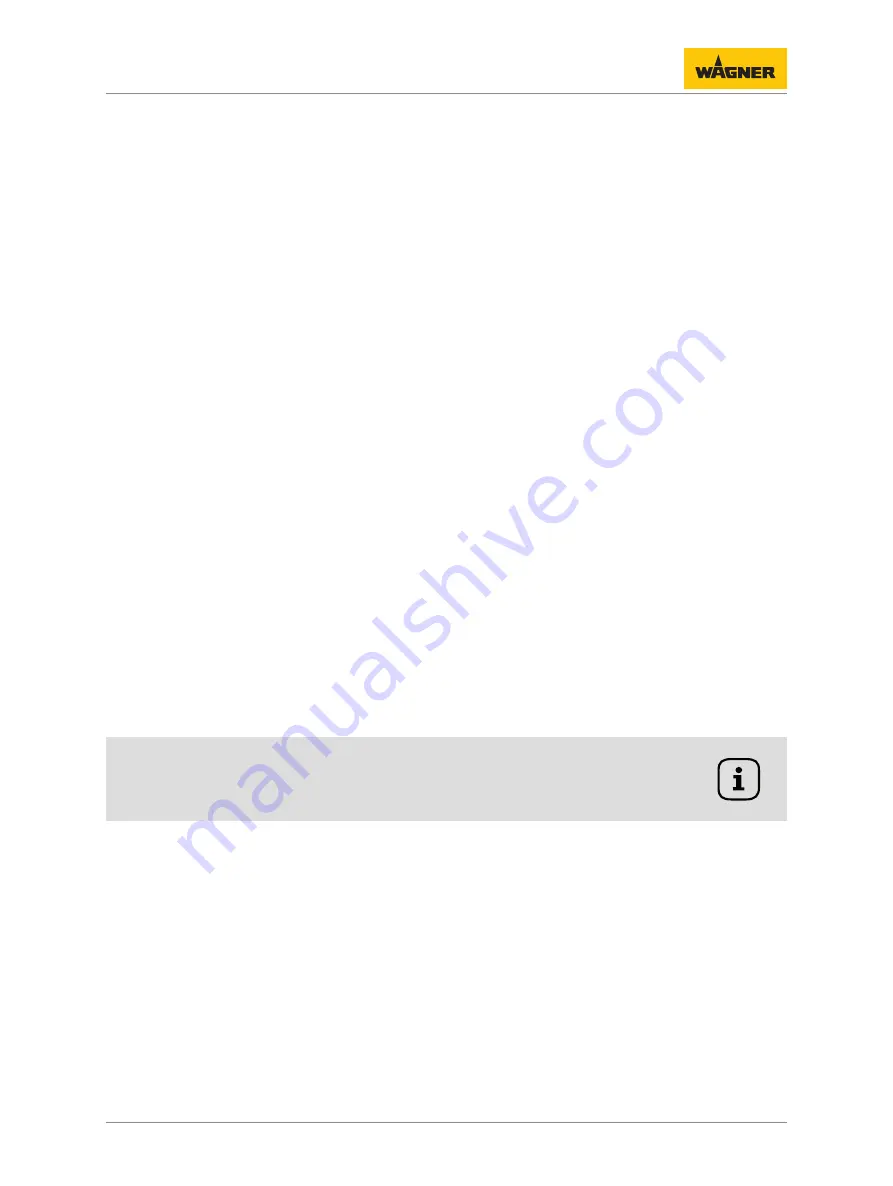
Operating manual Robot powder spray gun PER-X1
2 Using in Accordance with the Instructions
8
Order number 2444998 | Edition 10/2022
2 USING IN ACCORDANCE WITH THE INSTRUCTIONS
2.1 DEVICE TYPE
Robot powder spray gun for coating work pieces which are grounded.
2.2 TYPE OF USE
The robot powder spray gun is designed for the electrostatic coating of work pieces with
organic powders.
WAGNER explicitly prohibits any other use!
The robot powder spray gun may only be operated in a temperature range from 5–40 °C; 41–
104 °F.
Electrostatic coating systems may only be used in spray areas equipped in accordance with
EN 16985 or under equivalent ventilation conditions.
The device may only be operated under the following conditions:
4
Use the device only to work with the materials recommended by WAGNER.
4
Do not deactivate safety fixtures.
4
Use only WAGNER original spare parts and accessories.
4
The operating personnel must be trained on the basis of this operating manual.
4
Follow the instructions in the operating manual.
2.3 FOR USE IN POTENTIALLY EXPLOSIVE AREAS
This type A-P electrostatic powder spray gun is suitable for processing industrial powder
lacquers for coating electrically conductive objects and can be used in potentially explosive
areas (zone 22). (see chapter Identification [
In explosion hazard areas, only use approved explosion-proof electrical devices.
2.4 PROCESSIBLE WORKING MATERIALS
– Types of powder which can be charged electrostatically
– Metallic powder
Info
Contact your local WAGNER dealer and the lacquer manufacturer if you encounter
application problems.
2.5 MISUSE
Misuse can lead to physical injury and/or property damage! Special attention must be paid
that:
4
No liquid coating products, e.g. solvents or water-based lacquers, are processed.
4
No food, medicine or cosmetics are processed.