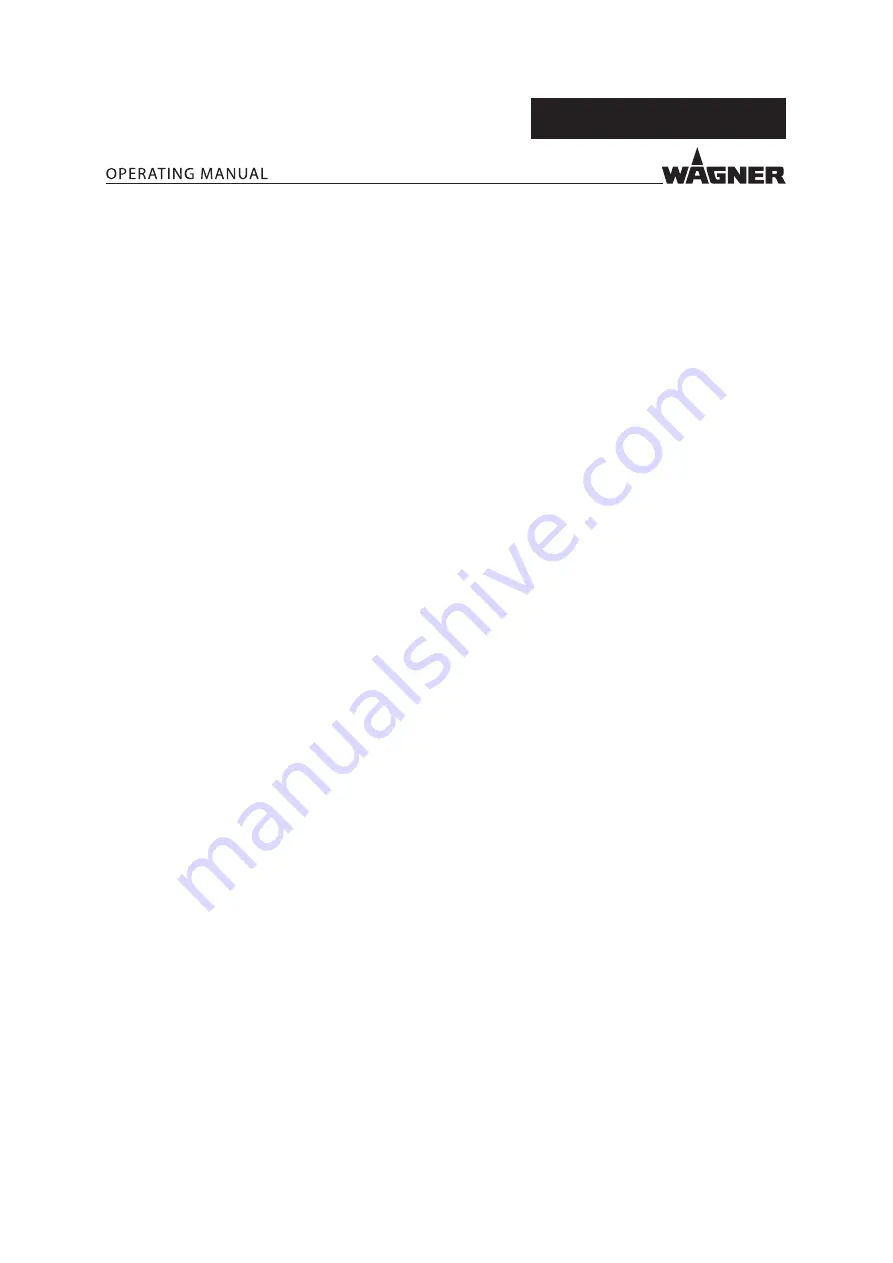
4
EDITION 08/2021
ORDER NUMBER DOC241936
IP 5000
How to Handle the Hose Coupling
Commissioning in Connection with the Powder Center
Commissioning as Transfer Pump (BigBag)
Pin Assignment in the Control Cabinet
Training the Operating Personnel
Operation with WAGNER Powder Center
Setting Elements in the Control Cabinet
Function 1 "Use of Powder Center/BigBag"
Function 3 "Set After-run Time"
Function 4 "Set Cleaning Time"
Function 6 "Set Service Interval"
Conditions for Operating the Pump
Cleaning in Case of Paint Change
SuperCenter Cleaning Procedure
Safety Checks and Maintenance Intervals
Storage Conditions for Pump and Valve Hoses
Summary of Contents for IP 5000
Page 2: ......
Page 78: ...78 EDITION 08 2021 ORDER NUMBER DOC241936 IP 5000 P_00030 Supply Release Display Display...
Page 79: ...79 EDITION 08 2021 ORDER NUMBER DOC241936 IP 5000 P_00031...
Page 80: ...80 EDITION 08 2021 ORDER NUMBER DOC241936 IP 5000 P_00032...
Page 81: ...81 EDITION 08 2021 ORDER NUMBER DOC241936 IP 5000 P_00033 Powder center...
Page 82: ...82 EDITION 08 2021 ORDER NUMBER DOC241936 IP 5000 P_00034 Cleaning box...
Page 86: ...86...
Page 87: ......