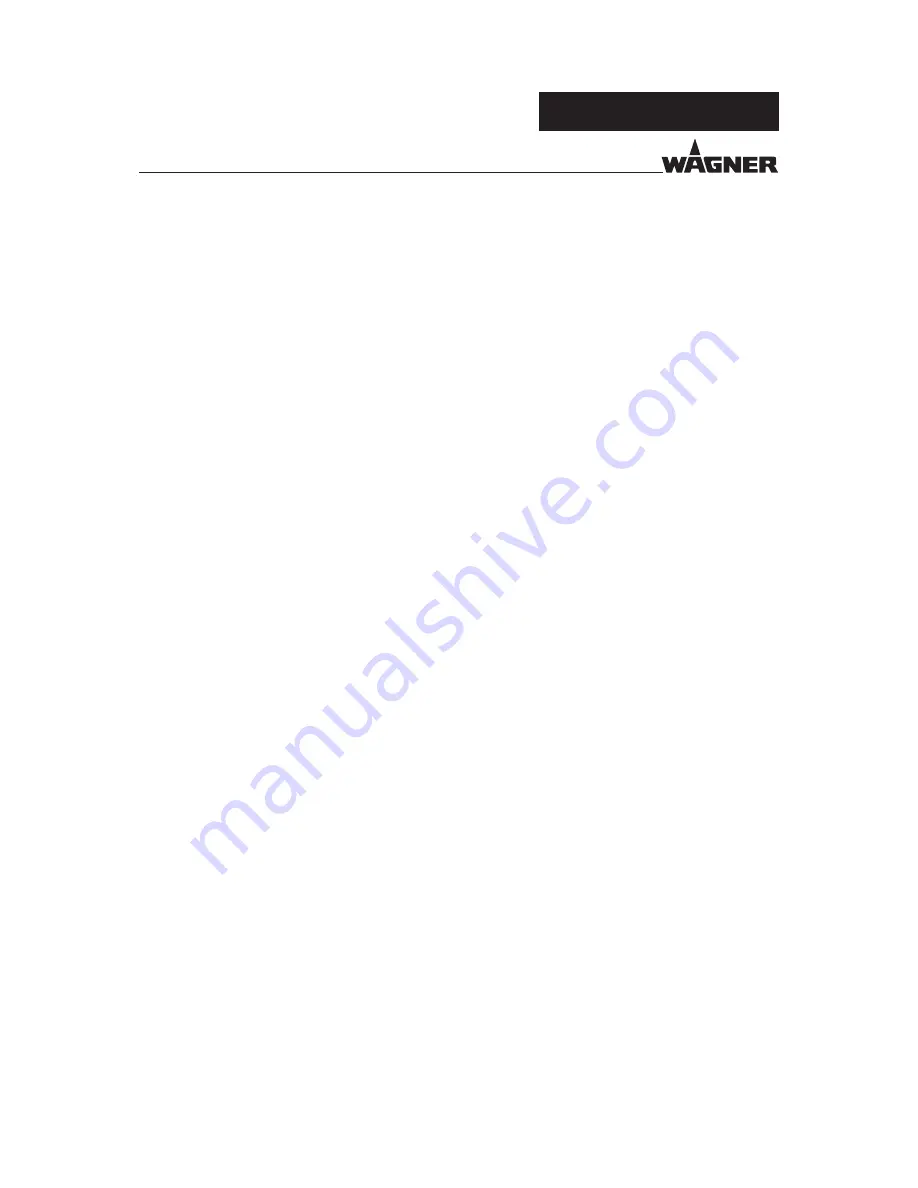
4
AC 4600 Pro
OPERATING MANUAL
EDITION 06/2012
PART NO. DOC394871
Contents
5.1.3
Air supply
17
5.1.4
Fluid (paint) hoses
17
5.1.5 Earthing
18
5.2
Preparation of paints
18
5.3 Starting-up
19
5.3.1
General rules for handling the spray gun
19
5.3.2
Preparation for starting up
20
5.4 Works
21
5.4.1
Start-up for spraying
21
5.4.2
Adjusting the spray pattern
21
5.4.3
Changing the AirCoat nozzle
22
5.4.4
Cleaning aircoat nozzle
23
5.4.5
Eliminate nozzle clogging
23
6.0 MAINTENANCE
24
6.1
Finishing work and cleaning
25
6.2
Replacing the material hose or air hose
26
6.3
Changing or cleaning fi lter insert
28
6.4
Replacing parts on the valve rod
30
6.4.1 Disassembling
30
6.4.2
Replacement of valve rocker seals
31
6.4.3
Replacing the rod seal (35)
31
6.4.4 Assembly
31
6.5
Replacing the nozzle seal
32
6.6
Replacing the „air“ sealing ring
33
7
TROUBLE SHOOTING AND SOLUTION
34
9 ACCESSORIES
35
9.1
Round jet nozzle cap
35
9.1.1
Nozzle inserts RXX
35
9.1.2
Nozzle screwed connection compl.
35
9.2
AirCoat nozzles ACF3000
36
9.3 Air
caps
38
9.4 Filter
insert
38
9.5 Hoses
38
9.6 Swivels
39
9.7 Miscellaneous
39
10 SPARE
PARTS
40
10.1
How to order spare parts?
40
10.2
Spare parts list AC4600 Professional
41