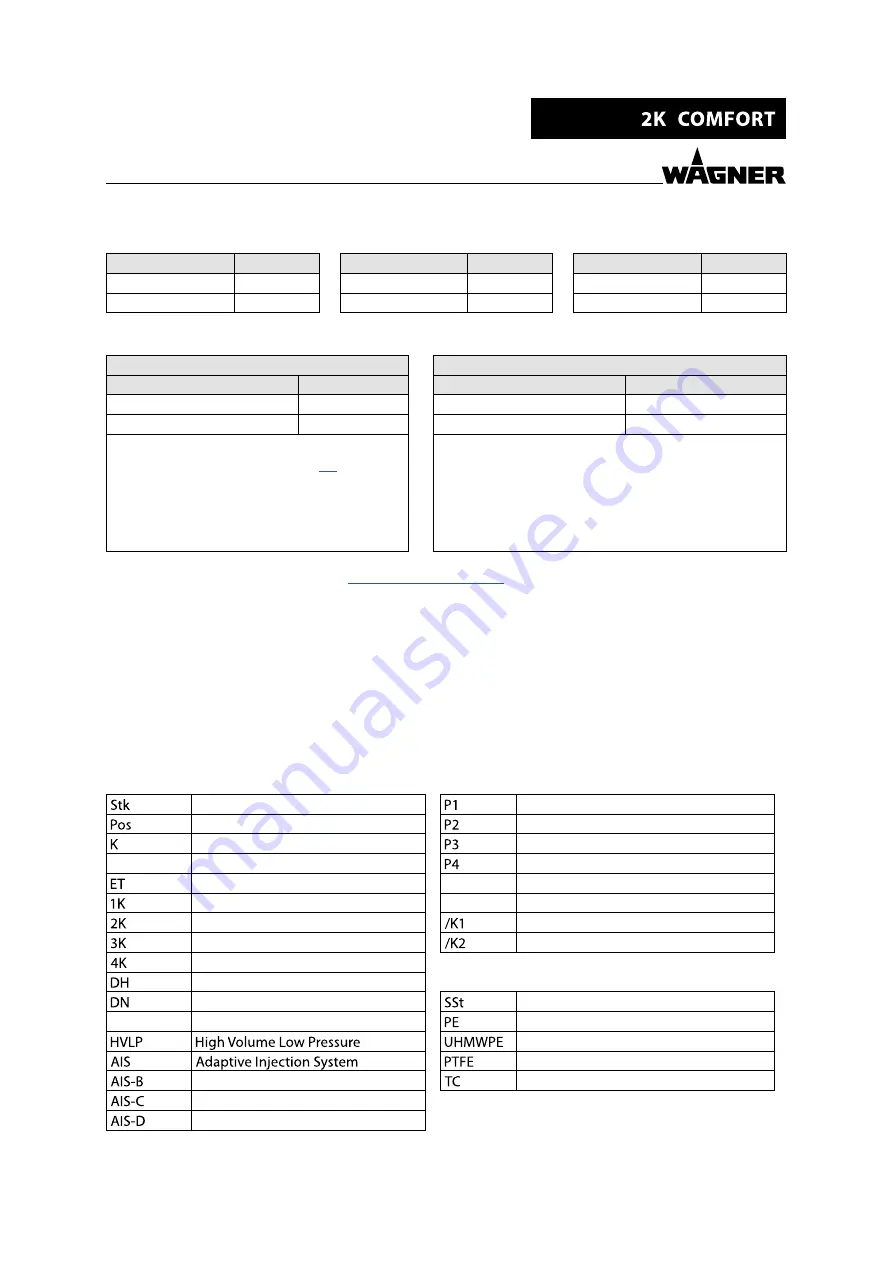
9
OPERATING MANUAL
VERSION 05/2017
ORDER NUMBER DOC 2357061
T0170.00BI pressure regulators
operating manual
Language
Order No.
Language
Order No.
Language
Order No.
German
ZZB019GER
English
ZZB019ENG
Spanish
ZZB019SPA
French
ZZB019FRE
Italian
ZZB019ITA
--
--
2K Data
2K Archive
2K Data
software documentation
2K Archive
software documentation
Language
Order No.
Language
Order No.
German
2382353
German
2361954
English
2382354
English
2361978
The 2K Data software is contained on the
2K SMART USB stick (see Chapter
).
Purpose: Transfer system settings, names, paint
and flushing recipes and the I/O configuration
via USB stick to the PC. View or change data on
the PC.
The 2K Archive software is available as an accessory.
Purpose:
Log and archive consumption data and error messages
on the PC.
Additional languages on request or at:
1.4
USB STICK 2K COMFORT
All operating documents specified above, as well as the accessory set's assembly manuals
(with the description of the accessory's function) are also available as pdf files on a USB
stick. The USB stick is included in the system's scope of delivery.
The
Order No.
is: 2359808 (specify additionally the Serial No. of the system)
1.5
ABBREVIATIONS
Number of pieces
Position
Marking in the spare parts lists
Order No.
Order number
Spare part
One component
Two components
Three components
Four components
Double stroke
Nominal diameter
HP
High pressure
AIS for component B
AIS for component C
AIS for component D
Spray gun 1
Spray gun 2
Spray gun 3
Spray gun 4
Q
Flow
cc
Cubic centimeters (cm
3
)
Fluid circuit 1 (in 2-circuit system)
Fluid circuit 2 (in 2-circuit system)
Materials
Stainless steel
Polyethylene
Ultra-high molecular weight polyethylene
Polytetrafluorethylene
Carbide