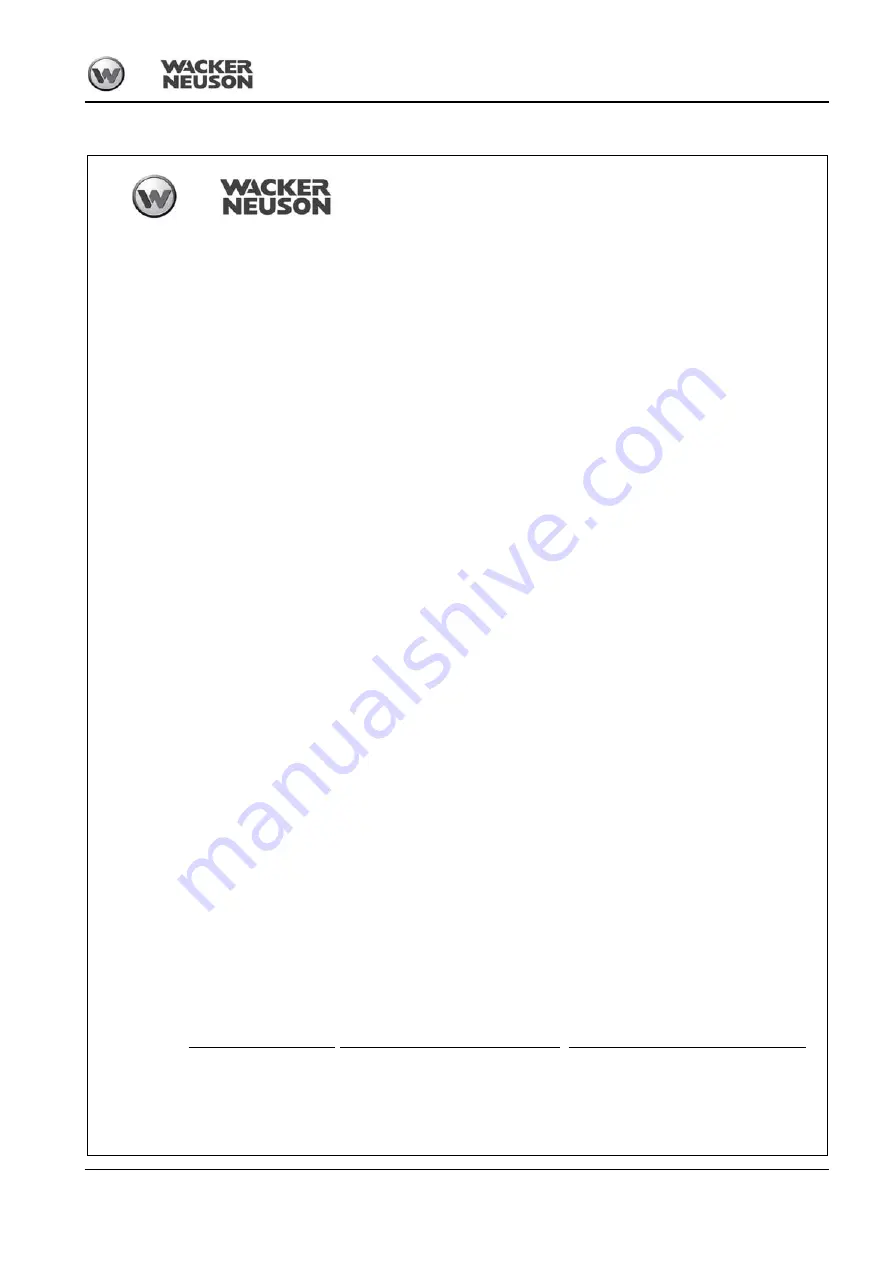
BA DT08 SL EN – Edition 1.0 * dt08b110.fm
1-5
Introduction
1.6 Declaration of conformity model DT08-P, for machines without CE mark on type label
Declaration of conformity
Manufacturer
Wacker Neuson Linz GmbH
Haidfeldstr. 37
A-4060 Linz-Leonding
Product
Machine designation:
Compact Dumper
Machine model:
DT08-P
Serial no.:
______________
Output (kW):
6.6 kW
Measured sound power level:
100 dB (A)
Guaranteed sound power level:
101 dB (A)
Directives and standards
We hereby declare that this product corresponds to the relevant regulations and requirements of the following Directives and
standards:
2004/108/EC, 2000/14/EC, 97/68/EC, EN ISO 12100;
EN 474-1 (except 5.5.8.1, 5.9, 5.19.1), EN 474-6 (except 5.7.3.3)
Managing director
Responsible for documentation
Leonding,
Place, date