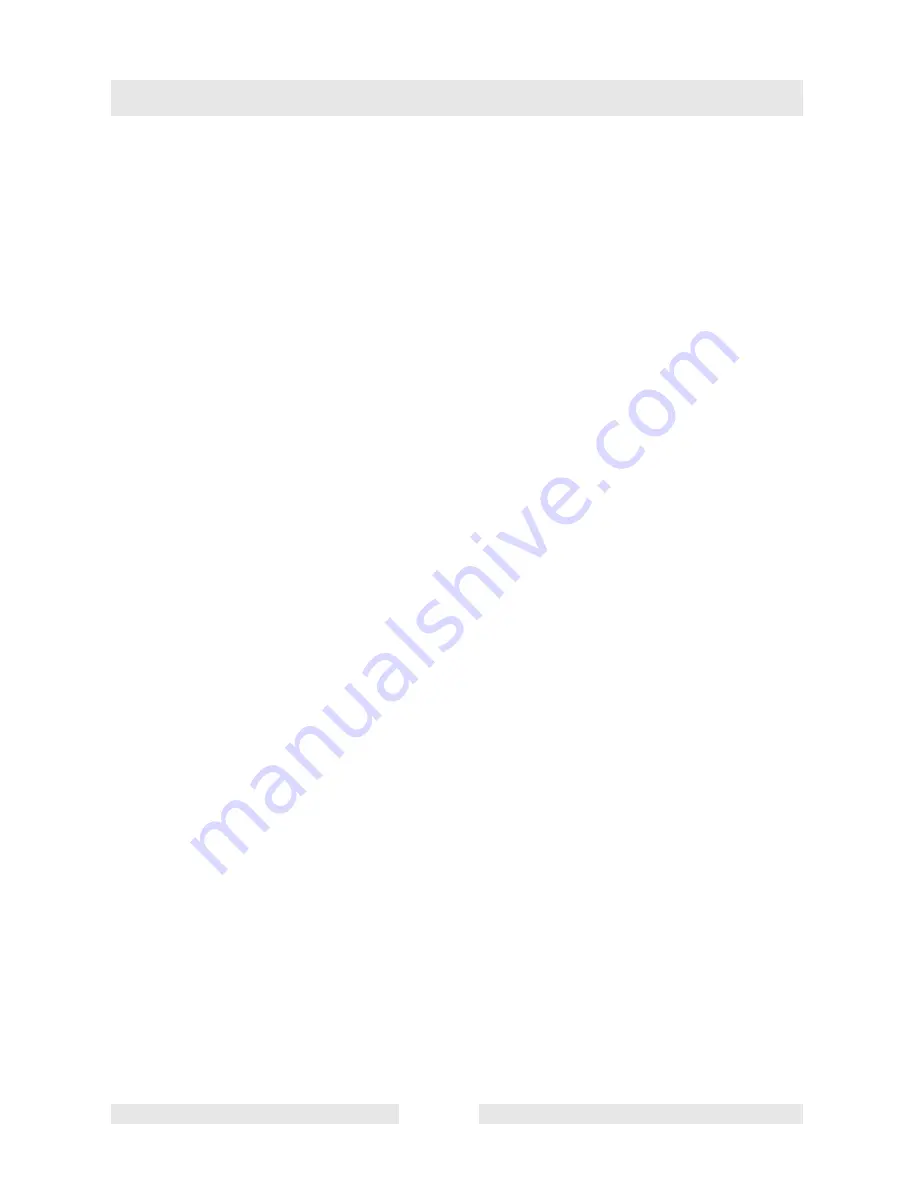
Safety instruction
SV00053GB.fm
8
2.2.14 When traveling backwards the operator has to guide the vibration plate
laterally by its guide handle so that he will not be squeezed between
the handle and a possible obstacle. Special care is required when work
ing on uneven ground or when compacting coarse material. Make sure
of a firm stand when operating the machine under such conditons.
2.2.15 Vibratory plates are to be guided such that hand injuries caused by
solid objects are avoided.
2.2.16 Vibratory plates have to be guided such that their stability is
guaranteed.
2.2.17 Machines with integrated transport trolley may not be parked or stored
on the trolley. This device has only been designed to transport the
machine.
2.3
Safety checks
2.3.1
Vibratory plates may only be operated with all safety devices installed.
2.3.2
Before starting operation, the operator has to check that all control and
safety devices function properly.
2.3.3
If defects in the safety equipment or other defects are detected which
impair the safe operation of the internal vibrator, the supervisor is to be
notified without delay.
2.3.4
The machine must to be switched off immediately in case of defects
jeopardizing the operational safety of the equipment.
2.3.5
Process materials and operating fuels must be stowed away in
receptacles or containers marked according to the respective
manufacturers specifications.
Summary of Contents for DPU 4045H
Page 1: ...www wackergroup com Operator s Manual Vibratory plate DPU 4045H 0109984en 003 04 2008 ...
Page 2: ......
Page 4: ...T00940GB fm 2 ...
Page 34: ......
Page 37: ......
Page 38: ......