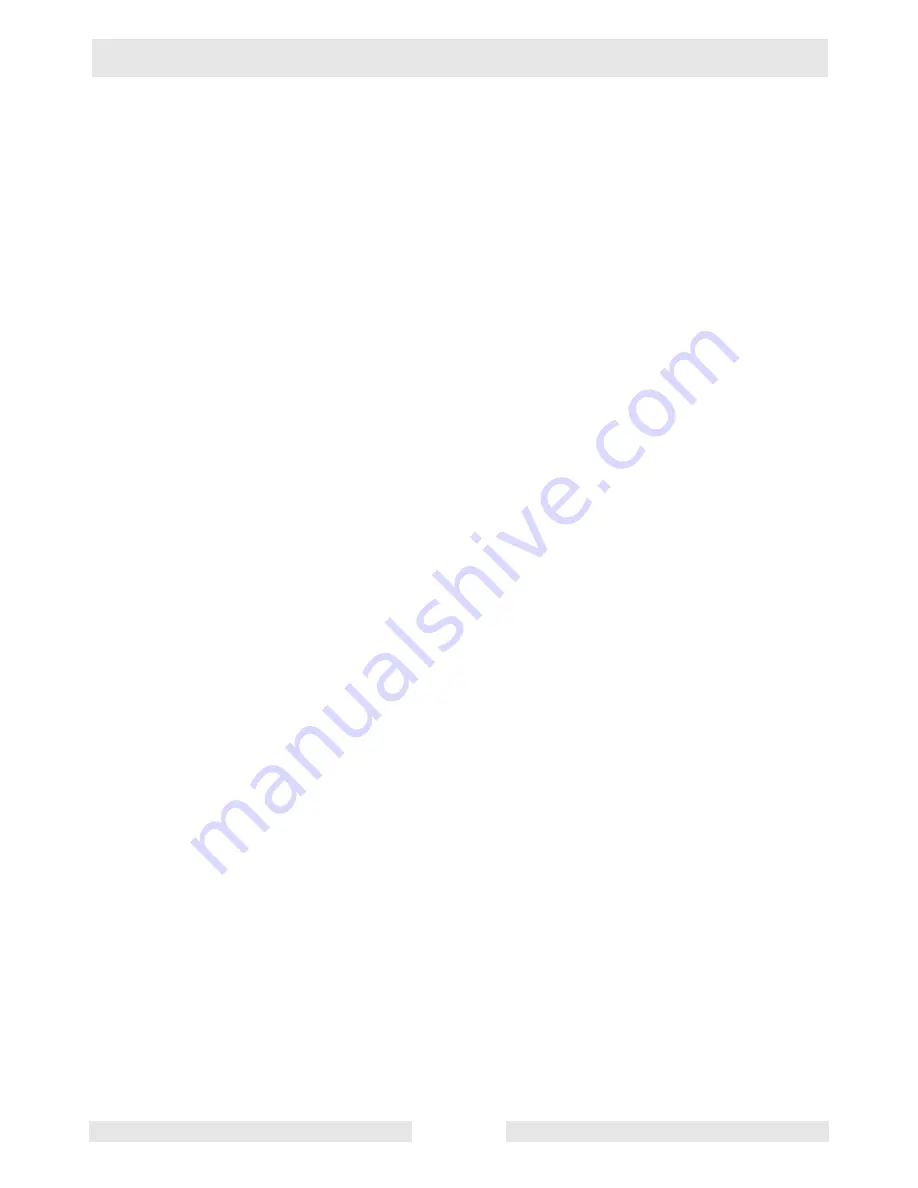
Operation
CRT 48-31V
wc_tx000141gb.fm
22
4.6
Stopping
To stop trowel movement, return joystick(s) or control levers
to their
neutral position and release pressure on the throttle foot pedal.
To stop the engine, turn the keyswitch to “O” (off).
4.7
Operation
To utilize your WACKER Riding Trowel to its fullest capacity, the
machine should be driven in the direction that the operator is facing.
This will finish the widest possible area, while giving the operator an
excellent view of the slab surface about to be troweled. When the
machine reaches the end of the slab, make a 180° U-turn, and repeat
the straight line of direction to the other end of the slab.
Note:
During the break-in period, run the engine at 50% of full throttle.
Refer to Section New Machines.
NOTICE
: DO NOT
use excessive pressure on the control levers.
Excessive pressure does not increase the reaction time of the machine
and can damage the steering controls.
NOTICE
:
Attempting to use the trowel too early in the curing stage of
the concrete may result in an undesirable finish. Only experienced
concrete finishers should operate the trowel.
Summary of Contents for CRT 48-31V
Page 1: ...Ride On Trowels CRT 48 31V OPERATOR S MANUAL 0154550en 006 1006 0 1 5 4 5 5 0 E N...
Page 2: ......
Page 10: ...Safety Information CRT 48 31V wc_si000049gb fm 8 2 5 Label Locations...
Page 11: ...CRT 48 31V Safety Information wc_si000049gb fm 9...
Page 35: ...CRT 48 31V Maintenance wc_tx000142gb fm 33...
Page 42: ...Maintenance CRT 48 31V wc_tx000142gb fm 40 Notes...
Page 43: ......
Page 56: ...AEM_ConcretePowerTrowel qxd 7 23 03 6 31 AM Page 1...