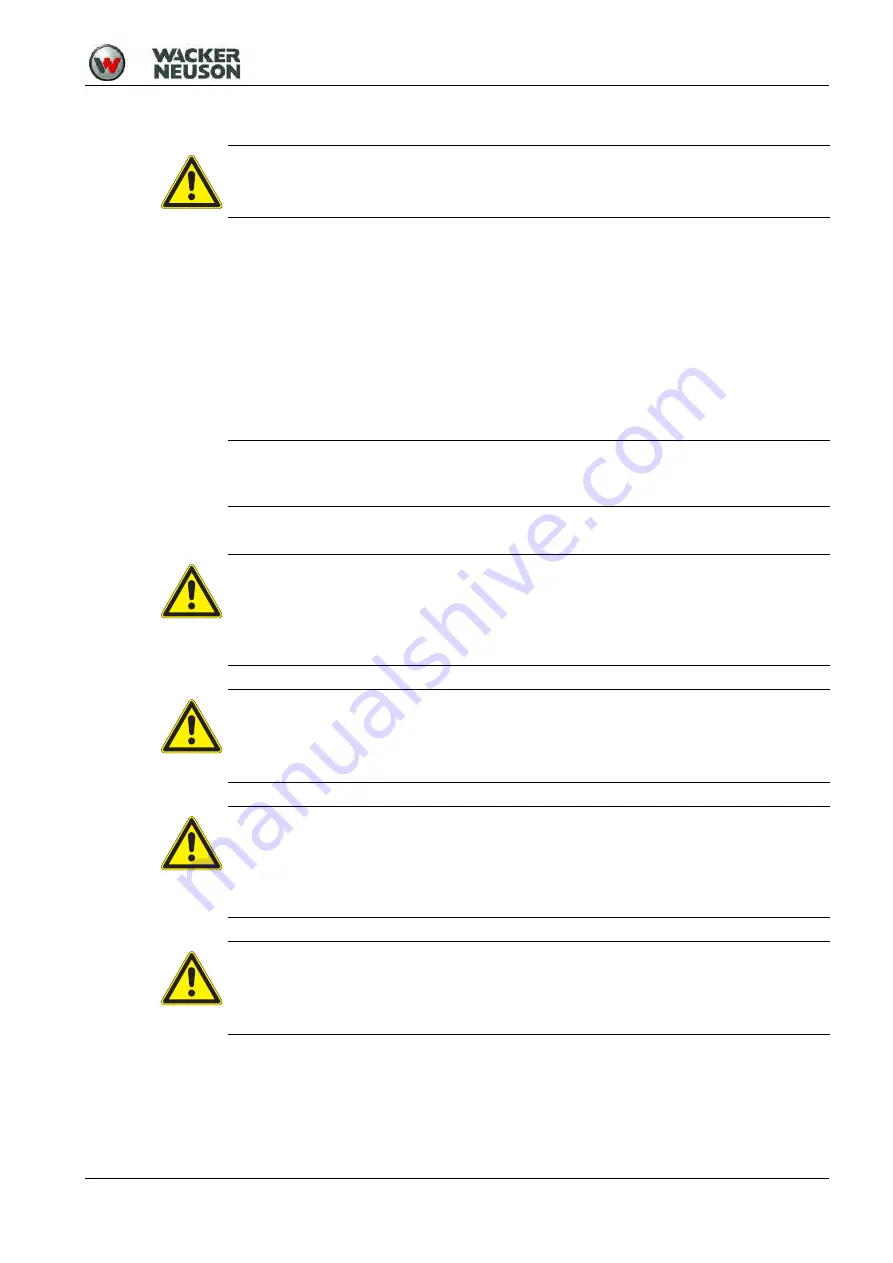
9 Operation and use
100_0201_op_0004.fm
21
9
Operation and use
9.1
Inspection before commissioning
Check the machine and components for damage. In the event of visible damage, do not operate the
machine and immediately contact a Wacker Neuson dealer.
Check the operator's controls for functionality.
Ensure that loose packaging material has been removed from the machine.
Current regulations of the local authorities for noise emissions are to be observed.
Check the fuel level.
Check the oil level.
Check to ensure the screwed connections are firmly seated.
Check the air intake area for contamination.
9.2
Notes about operation
In accordance with the intended purpose, the operator should stand behind the machine.
Guide and steer the machine using the control handle.
Utilize the machine's dead weight when working.
Allow the machine to pull forward independently. Do not push or pull forward or backward with muscle
power.
WARNING
Improper handling may result in injury or serious material damage.
Please read and follow all safety instructions in this operator's manual.
NOTICE
Perform control procedures according to the
Maintenance
chapter. If necessary, top off
missing fuel, lubricants and coolants, see chapter
Technical Data.
WARNING
Danger of tipping
There is a serious risk of injury from slipping or tipping over of the machine.
Always secure the machine from tipping over.
Place the machine on level surface with a firm substrate.
WARNING
Danger of crushing
It is possible to crush hands and feet.
Work carefully.
CAUTION
Beware of physical impairments caused by vibration.
Increasing hand and arm vibrations.
Do not overload the machine.
Take breaks periodically.
CAUTION
Injuries or material damage.
There can be strong recoils on firm, hard or rigid bottoms.
Avoid these bottoms.
Summary of Contents for BS Series
Page 50: ......