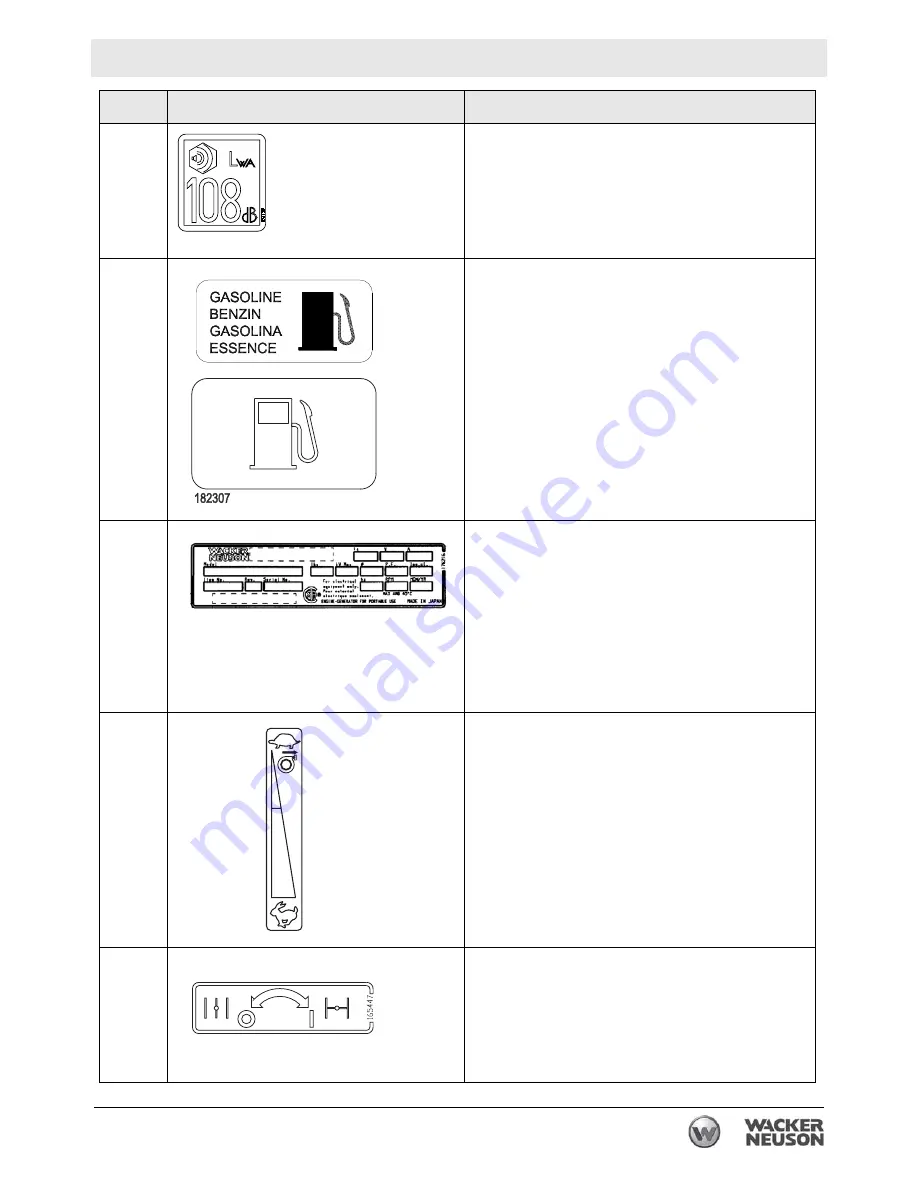
BS 60-4s
Labels
wc_si000494gb.fm
25
E
Guaranteed sound power level in dB(A).
F
CAUTION!
Use only clean, filtered gasoline fuel.
This label is molded into the cover. If it
becomes illegible, the cover must be
replaced. Refer to the Parts Book for ordering
information.
G
A nameplate listing the model number, item num-
ber, revision number, and serial number is
attached to each unit. Please record the informa-
tion found on this plate so it will be available
should the nameplate become lost or damaged.
When ordering parts or requesting service infor-
mation, you will always be asked to specify the
model number, item number, revision number, and
serial number of the unit.
H
Turtle = Idle/slow engine speed
Rabbit = Full/fast engine speed
This label is molded into the cover. If it
becomes illegible, the cover must be
replaced. Refer to the Parts Book for ordering
information.
K
Choke:
0 = Open
l = Closed
Label
Meaning
Summary of Contents for BS 60-4s
Page 1: ...0170873en 001 0410 0 1 7 0 8 7 3 E N Operator s Manual Rammer BS 60 4s...
Page 21: ...BS 60 4 Safety Information wc_si000440gb fm 21 Notes...
Page 46: ......
Page 48: ......