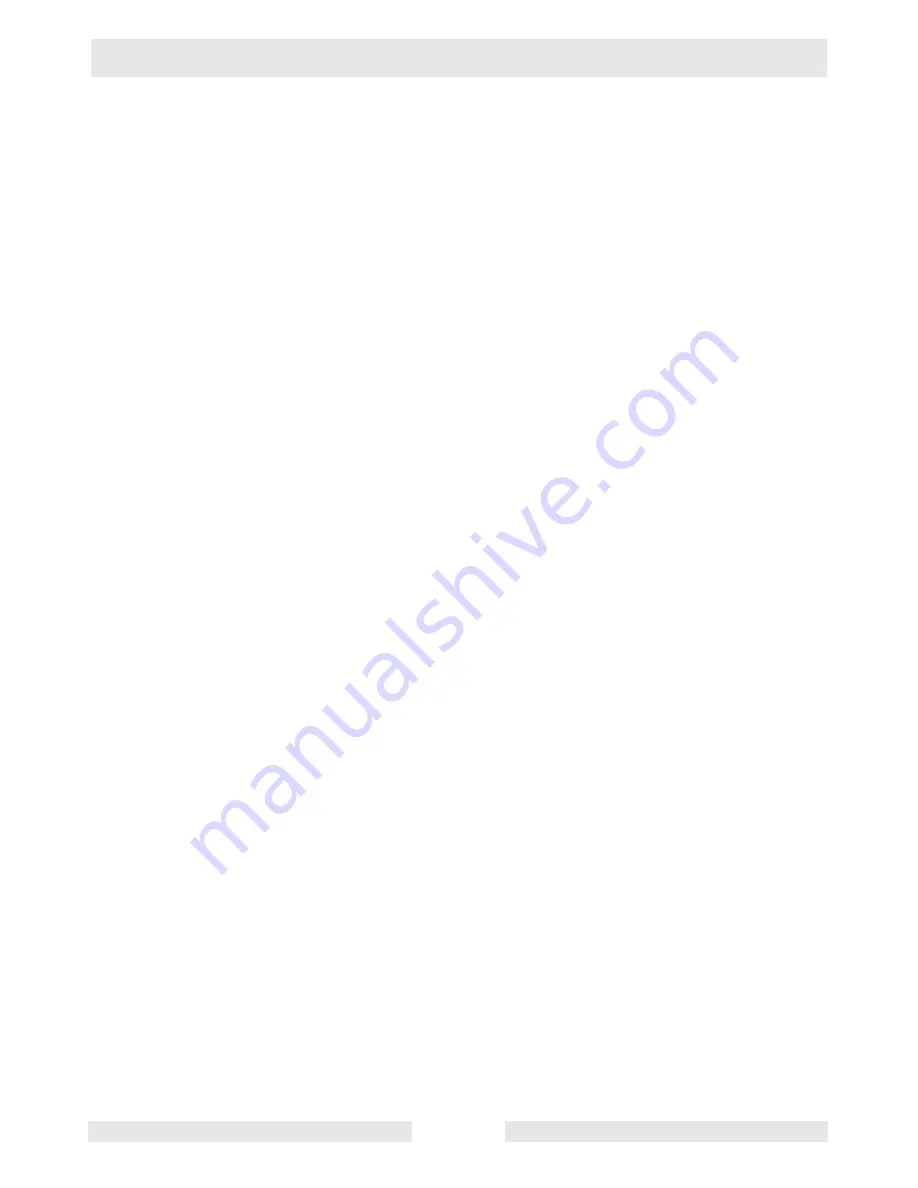
Oil Injection (if equipped)
Rammer Repair
wc_tx000288gb.fm
92
6.2
Oil Line Check Valve
See Graphic: wc_gr001527
The the function of the oil line check valve
(a)
is to prevent raw fuel
from backing up to the oil pump. It is important that the check valve be
installed in the correct direction. Looking at the side of the check valve,
one should notice recessed areas with pointed ends or an arrow
(b)
.
The pointed ends or the arrow must point towards the fuel line. This is
the direction of oil flow.
To test the check valve:
The oil line check valve is spring operated and is designed to release
at 1.5 psi.
Note:
Initial release can be as high as 4.5 psi
.
6.2.1
Remove the oil line check valve from the oil line.
6.2.2
Attach a hand-operated vacuum pump to the outlet side (pointed end)
of the oil line check valve and operate the vacuum pump until the
vacuum overcomes the oil line check valve spring. Measure how much
vacuum it takes to operate the oil line check valve. A vacuum reading
of more than 2 psi (after initial release) is grounds for replacing the oil
line check valve.
Note:
The oil line check valve is only available by replacing the entire
hose assembly.
Newly installed oil line check valves (and those that have lost their
prime) require priming. There are two methods of priming the oil line
check valve line with oil.
Vacuum method
:
6.2.3
Attach a hand-operated vacuum pump to the fuel line end of the oil
hose.
6.2.4
Place the oil pump side of the hose in a container of 2-cycle oil.
6.2.5
Operate the vacuum pump until the oil reaches the vacuum pump.
6.2.6
Install the oil line to the oil pump and to the fuel line.
Pressure method:
6.2.7
Attach a syringe filled with 2-cycle oil to the oil pump end of the hose.
6.2.8
Inject the oil into the hose until it passes through the oil line check
valve.
6.2.9
Attach the oil line to the oil pump.
NOTICE:
The oil line check valve is an important part of the oil injection
system and should not be bypassed. Engine failure may occur.
Summary of Contents for BS 50-4
Page 2: ......
Page 27: ...Rammer Repair General wc_tx000284gb fm 27 Notes ...
Page 29: ...Rammer Repair Guide Handle and Engine wc_tx000285gb fm 29 ...
Page 41: ...Rammer Repair Guide Handle and Engine wc_tx000285gb fm 41 wc_gr001313rm a b d e c f ...
Page 43: ...Rammer Repair Guide Handle and Engine wc_tx000285gb fm 43 e b c d wc_gr004562 a g f ...
Page 47: ...Rammer Repair Guide Handle and Engine wc_tx000285gb fm 47 w c _ g r 0 0 1 3 1 5 r m a c b d ...
Page 49: ...Rammer Repair Guide Handle and Engine wc_tx000285gb fm 49 wc_gr002935 d a b e c d ...
Page 53: ...Rammer Repair Guide Handle and Engine wc_tx000285gb fm 53 w c _ g r 0 0 1 3 1 7 r m a ...
Page 57: ...Rammer Repair Guide Handle and Engine wc_tx000285gb fm 57 c a b wc_gr001319rm DS 720 Models ...
Page 59: ...Rammer Repair Guide Handle and Engine wc_tx000285gb fm 59 DS 70 Models wc_gr002372rm a b c ...
Page 69: ...Rammer Repair Ramming System wc_tx000286gb fm 69 wc_gr001324rm Hydraulic Press Method ...
Page 71: ...Rammer Repair Ramming System wc_tx000286gb fm 71 wc_gr001325rm Threaded Rod Method ...
Page 81: ...Rammer Repair Ramming System wc_tx000286gb fm 81 Notes ...
Page 84: ...Crankcase Rammer Repair wc_tx000287gb fm 84 wc_gr001333rm p o n m f ...
Page 93: ...Rammer Repair Oil Injection if equipped wc_tx000288gb fm 93 wc_gr001527 a b ...
Page 115: ...Rammer Repair Technical Data wc_td000112gb fm 115 NOTES ...
Page 120: ...Technical Data Rammer Repair wc_td000112gb fm 120 ...
Page 125: ......