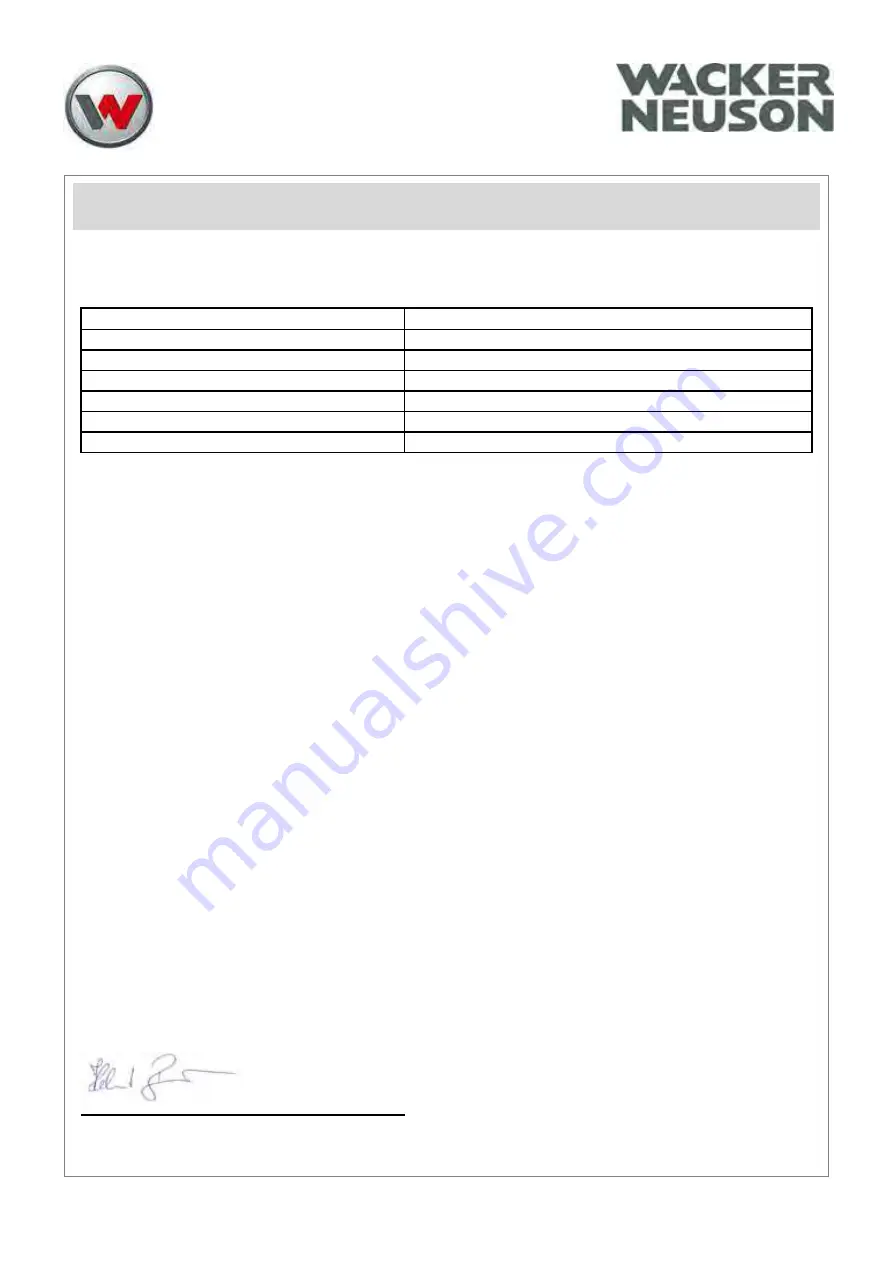
5100010141_07_BPU4045_CE_en
2006/42/EC, 2000/14/EC, 2014/30/EU, EN 500-1:2006 +A1:2009, EN 500-4:2011, EN ISO 13766-
1:2019, EN ISO 13766-2:2019
Person responsible for technical documents
Wacker Neuson Produktion GmbH & Co. KG, Wackerstraße 6, D-85084 Reichertshofen
Reichertshofen, 03.06.2019
Managing Director
Net installed power
5,1 kW
Measured sound power level
107 db(A)
Guaranteed sound power level
108 db(A)
EC Declaration of Conformity
Manufacturer
Wacker Neuson Produktion GmbH & Co. KG, Wackerstraße 6, D-85084 Reichertshofen
This declaration of conformity is issued under the sole responsibility of the manufacturer.
Product
BPU4045
Product type
Vibratory plate
Function of product
Soil compaction
Material number
5100009663
Helmut Bauer
Original Declaration of Conformity
Conformity assessment procedure
2000/14/EC, Annex VIII
Notified body
TÜV Rheinland LGA Products GmbH, Tillystr. 2, D-90431 Nürnberg (NB 0197)
Guidelines and standards
We hereby declare that this product complies with the relevant provisions and requirements of the
following directives and standards: