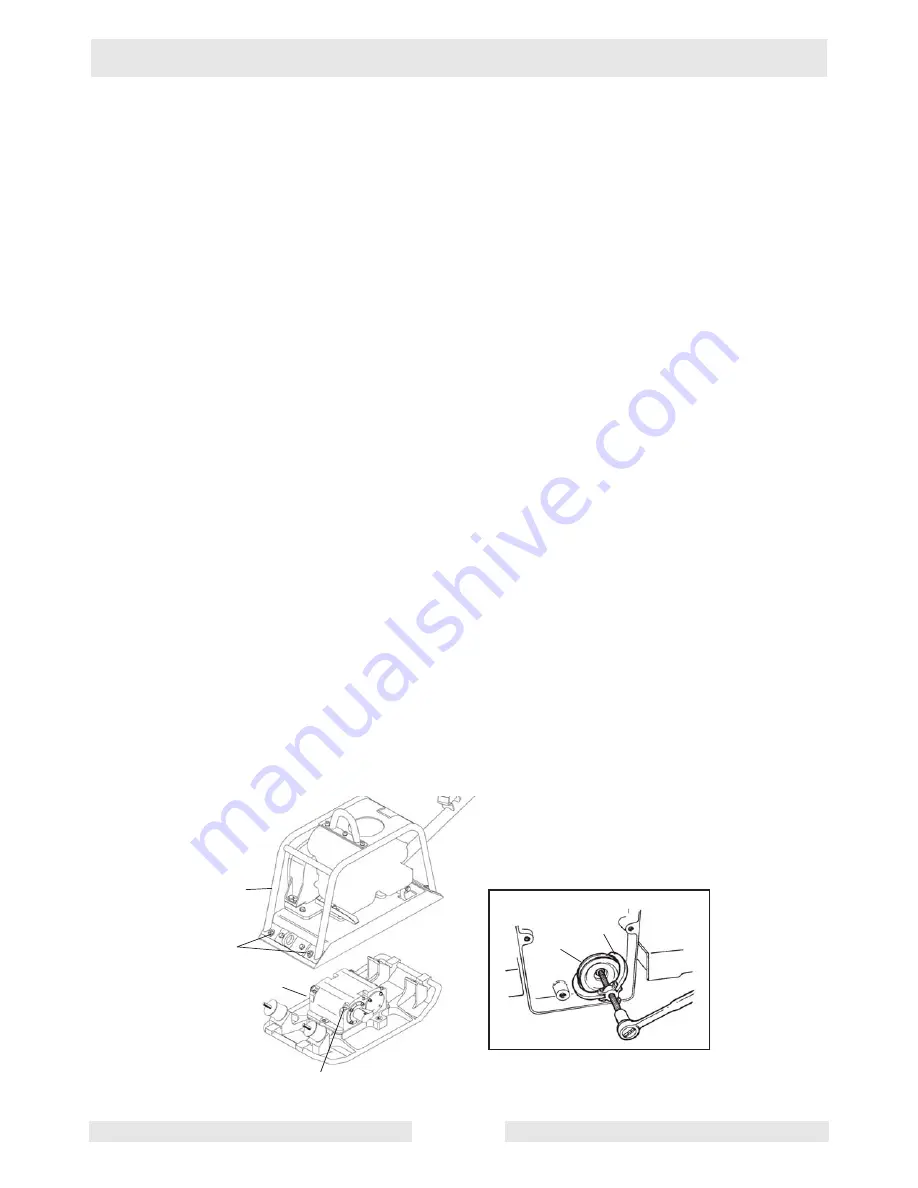
Repair Procedures
BPU 2440/2950 Repair
wc_tx000329gb.fm
34
5.5
Removing Exciter
See graphic: wc_gr001347
Recommended Tools:
Socket wrench – 19 mm
Allen wrench – 6 mm, 8 mm
Open-end wrench – 17 mm, 19 mm
Locking pliers
3-jaw puller
Rubber mallet
High-strength thread locking adhesive
Gasket eliminator
5.5.1
Turn machine’s engine off.
5.5.2
Remove belt guard and remove drive belt.
5.5.3
Using a 3-jaw puller (a), remove pulley (b) from exciter drive shaft.
5.5.4
Clamp the control line hose with locking pliers or C-clamp to prevent
leaking. Then, disconnect the line from the front exciter flange cover.
5.5.5
Using a 19 mm socket, remove the four hex nuts (c) that secure the
tubular frame (d) to the plate. Remove the frame from the plate.
5.5.6
Using an appropriate lift or crane, lift the complete upper mass from the
baseplate to expose the exciter assembly.
5.5.7
Mark the exciter housing referencing the right hand front side (e).
5.5.8
Remove the eight socket head screws (f) securing exciter and lift the
exciter from the plate.
wc_gr001437
a
b
c
d
f
e
Summary of Contents for BPU 2440 series
Page 2: ......
Page 21: ...BPU 2440 2950 Repair General Information wc_tx000264gb fm 17 wc_gr001431 1 2 3 c 90 90 a b 0...
Page 57: ......