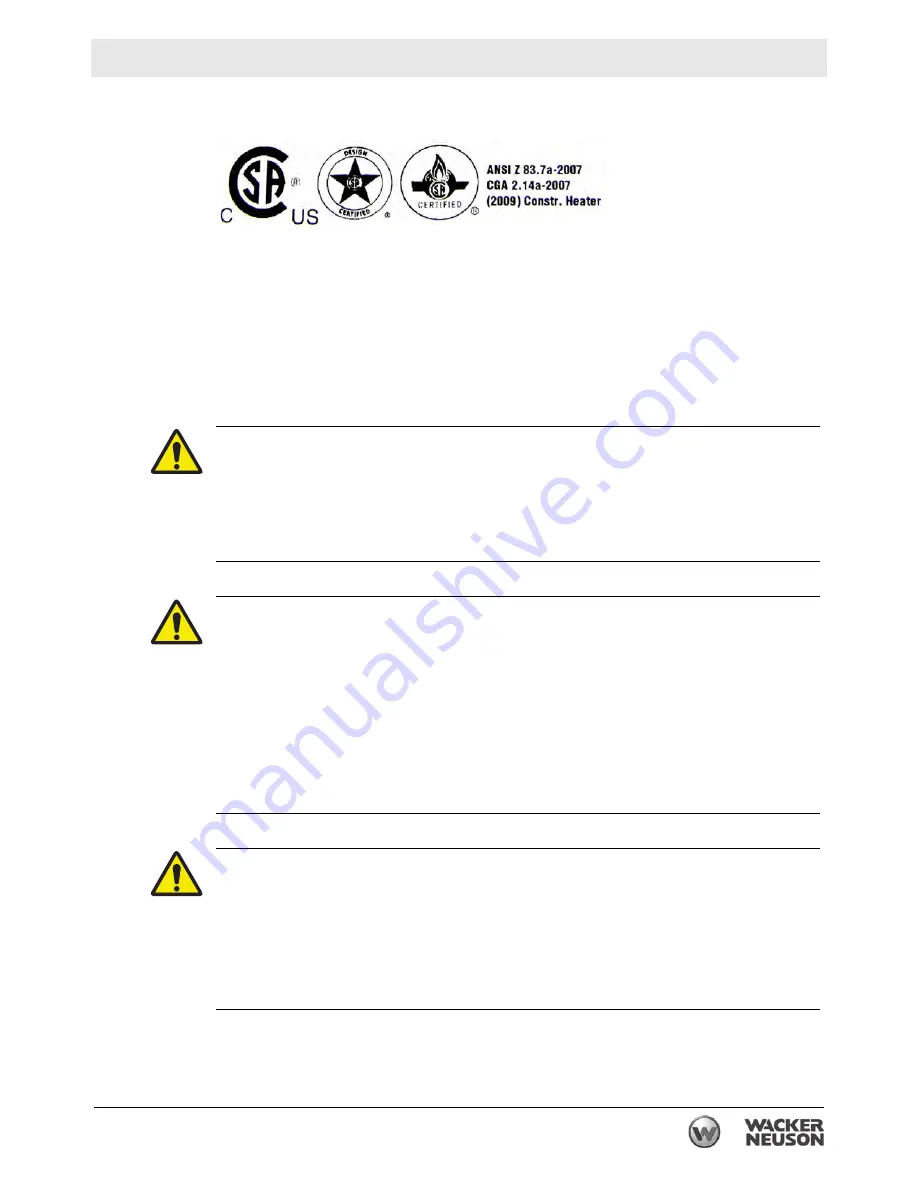
ghi_tx001257gb_FM10.fm
3
HI750
Foreword
Foreword
This heater is designed and approved for use as a construction heater in
accordance with Standard ANSI Z83.7–CSGA 2.14. CHECK WITH YOUR LOCAL
FIRE SAFETY AUTHORITY IF YOU HAVE QUESTIONS ABOUT APPLICATIONS.
Other standards govern the use of fuel gases and heat producing products in
specific applications. Your local authority can advise you about these.
THE INSTALLATION OF THE UNIT SHALL BE IN ACCORDANCE WITH THE
REGULATIONS OF THE AUTHORITIES HAVING JURISDICTION.
WARNING
Risk of personal injury or machine damage from improper use.
►
Before using the machine, read and understand all instructions and follow them
carefully.
►
The manufacturer is not responsible for damages to goods or persons due to
improper use of this machine.
WARNING
Failure to comply with the precautions and instructions provided with this machine
can result in death, serious injury, and property loss or damage from fire, explosion,
burns, asphyxiation, carbon monoxide poisoning, and/or electric shock.
►
Before using the machine, read and understand all precautions and instructions
that have been provided. Follow them carefully.
►
Only persons who can understand and follow the precautions and instructions
should use or service this machine.
►
Contact the manufacturer if you need assistance with operating the machine or
need replacement manuals or labels.
WARNING
Work site fire, burn, inhalation, and explosion hazards.
►
Keep solid combustibles, such as building materials, paper, or cardboard at a
safe distance away from the machine.
►
Never use this machine in spaces which do or may contain volatile or airborne
combustibles, or products such as gasoline, solvents, paint thinner, dust
particles, or unknown chemicals.
Summary of Contents for 5000620856
Page 6: ...ghi_tx001257gb_FM10 fm 6 Foreword HI750 ...
Page 27: ...HI750 Labels ghi_si000380gb_FM10 fm 27 BB CC FF ...
Page 115: ...wc_tx003699gb_FM10 fm 115 Kubota Genset Genset Maintenance ...
Page 122: ...ghi_td000360gb_FM10 fm 122 Technical Data HI750 Notes ...
Page 142: ......
Page 143: ......