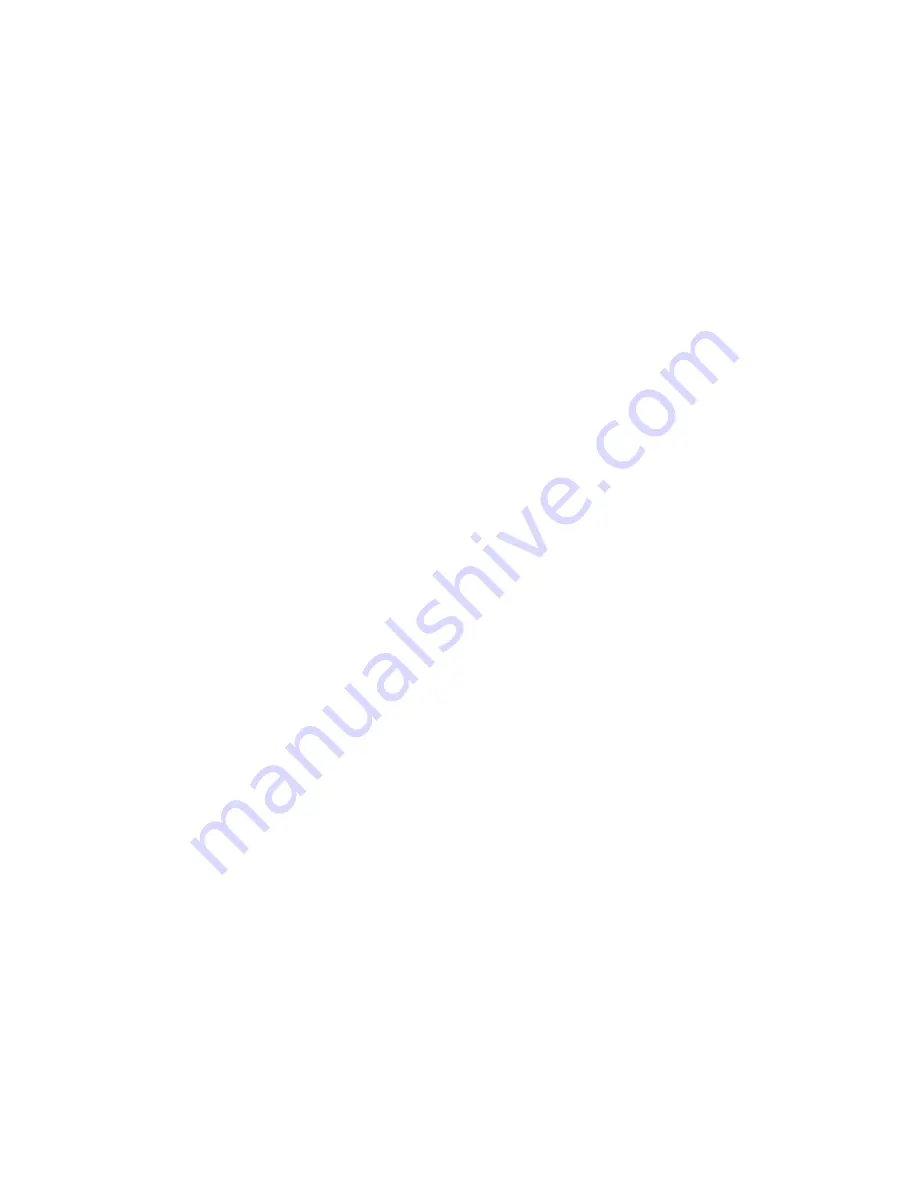
MICO, Inc.
(2)
Form No. 81-460-044 Revised 2017-04-17
DISASSEMBLY
(Refer to Figure 1)
1. Remove ring (22) and boot (21) from control section housing (10).
2. Remove piston (20), shim(s) (19), spring (18) and spring (17)
from control section housing (10). Note the number of shim(s)
removed for reassembly purposes.
NOTE: Not all models use
spring (17).
3. Remove o-ring (16). Depress plunger (13) and remove retaining
ring (15).
4. Remove washer (14), plunger (13), and spring (11) from housing
(10). Remove cup (12) from plunger (13). Note direction of cup (12).
5. Remove plug (1) from control section housing (10).
6. Remove washer (5), spring (6) and guide (7) from housing bore.
7. Remove o-ring (2), cup (4), and back-up ring (3) from plug (1).
8. Remove valve assembly (8) from housing bore.
9. Remove o-ring (9) from valve assembly (8).
10. Remove plug (24) from control section housing (10). Remove
o-ring (25) from plug (24).
11. Remove nylon pin (23) from plug (24) using a drive pin punch.
Be careful not to damage threads.
12. Remove spring (26), seat (27) and ball (28) from housing bore.
13. Remove plug (37) from control section housing (10). Remove
o-ring (36) from plug (37).
14. Remove spring (35), stop (34), and ball (33) from housing bore.
15. Using a 6.35 mm (0.25 in) diameter wooden or plastic dowel,
carefully push insert (31) and spool (32) from housing bore.
NOTE: Be careful not to scratch or mar valve seats on
insert (31).
16. Remove spool (32) from insert (31). Remove o-rings (29 & 30)
from insert (31).
17.
Earlier models:
Loosen nut (38) on screw assembly (39) and
remove screw assembly (39) from housing (10). Remove o-ring
(40) from screw assembly (39). Remove spring (41), poppet or
ball (42), seat (43), o-ring (44), and washer (45) from housing (10).
Later models: Some later models use a directional spring (41).
Directional spring (41) is attached to screw assembly (39) by
means of the small diameter end of spring (41) being snapped
into a groove on the nose end of screw assembly (39). See
Figure 1a.
Remove nut (38) and remove screw assembly (39)
from housing (10). Remove o-ring (40) from screw assembly (39)
from nut (38) side of screw assembly. Remove shim (63), spring
(41), steel ball (42), seat (43), o-ring (44) and washer (45) from
housing (10).
18. Remove filter (46) from housing (10).
19. Depress plug (48) and remove retaining ring (47) from charging
section housing (54).
20. Remove plug (48), spring (50), and stop (51) from housing bore.
Remove o-ring (49) from plug (48).
21. Remove spool (53) from housing bore. The spool can be guided
out of the charging section by reaching into either of the large ports.
22. Remove o-ring (52) from spool (53).
23. Depress plug (56) and remove retaining ring (57). Remove
plug (56) from housing bore.
24. Remove o-ring (55) from plug (56).
25. Remove three cap screws (58 & 62) and lock washers (59).
26. Separate control section housing (10) and charging section
housing (54).
27. Remove o-rings (60 & 61) from sections.
ASSEMBLY
(Refer to Figure 1)
LUBRICATE ALL RUBBER COMPONENTS FROM REPAIR KIT WITH
CLEAN TYPE FLUID USED IN THE SYSTEM.
1. Place new o-rings (60 & 61) in the proper grooves on charging
section housing (54).
2. Assemble control section housing (10) and charging section
housing (54) using three cap screws (58 & 62) and lock washers
(59). Torque cap screws 29.8-36.6 N·m (22-27 lb·ft).
3. Install new o-ring (55) on plug (56). Install plug in charging section
housing (54). Note direction of plug (56).
4. Install retaining ring (57) in housing (54) bore.
5. Install new o-ring (52) on spool (53). Insert spool in housing bore.
Be sure spool is all the way into bore so that the end of the spool
contacts the plug on opposite end. Note direction of spool.
6. Install spring (50) and stop (51) into housing (54).
7. Install new o-ring (49) on plug (48). Install plug (48) in housing
bore. Note direction of plug.
8. Install retaining ring (47) in charging section housing (54).
9. Install new filter (46) in control section housing (10).
10.
Earlier Models:
Install new o-ring (40) on screw assembly (39).
Install washer (45), new o-ring (44), seat (43), new plastic poppet
or existing steel poppet/steel ball (42), spring (41) and screw
assembly (39) into housing (10). Torque screw assembly (39)
24.4-29.8 N·m (18-22 lb·ft). Then install nut (38) on screw
assembly (39) and torque nut 43.4-51.5 N·m (32-38 lb·ft).
NOTE: Some models use a steel ball or steel poppet in place
of plastic poppet (42), reinstall steel ball or steel poppet.
Later models: Some later models use a directional spring
(41). Directional spring (41) is attached to screw assembly
(39) by means of the small diameter end of spring (41) being
snapped into a groove on the nose end of screw assembly
(39). If necessary, reattach the small diameter of spring (41)
into the groove on the nose end of screw assembly (39) using
a slight twisting motion. See Figure 1a.
Install new o-ring (40)
on screw assembly (39) from nut (38) side of screw assembly.
Install washer (45), new o-ring (44), seat (43), steel ball (42), and
spring (41) in housing (10). Fully lubricate shim (63) with clean
system fluid and install in housing (10) on end of seat (43). Install
screw assembly (39) in housing (10). Torque screw assembly (39)
24.4-29.8 N·m (18-22 lb·ft). Then install nut (38) on screw assembly
(39) and torque nut 43.4-51.5 N·m (32-38 lb·ft).
11. Install new o-rings (29 & 30) on insert (31).
12. Install spool (32) into insert (31). Note direction of insert (31)
and spool (32). Carefully install insert (31) into control section
housing (10).
13. Install ball (33) in housing bore.
14. Put a small amount of grease on end of spring (35) to hold stop
(34) in place. Install stop and spring in housing bore. Note direction
of stop and spring.
15. Install new o-ring (36) on plug (37) and install in housing bore.
Torque plug 54.2-67.8 N·m (40-50 lb·ft).
16. Position housings so plug (24) housing bore faces up. Drop ball
(28), seat (27), and spring (26) into housing.
17. Insert new nylon pin (23) into plug (24). Be sure nylon pin is
properly aligned and evenly driven into screw. Do not damage
threads.
18. Install new o-ring (25) on plug (24). Install plug (24) in housing
bore.
19. Install new o-ring (9) on valve assembly (8). Install valve assembly (8)
into control section housing (10). Note direction of valve assembly.
20. Insert new back-up ring (3) and new cup (4) in plug (1). Note order
of back-up ring and cup. Install new o-ring (2) on plug (1).
21. Install guide (7), spring (6), and washer (5) in plug (1).
22. Install plug assembly in control section housing (10). Torque
54.2-67.8 N·m (40-50 lb·ft).
23. Install new cup (12) and spring (11) on plunger (13). Install plunger
(13) in control section housing (10). Note direction of plunger.
24. Install washer (14) in housing bore.
25. Install retaining ring (15) in housing bore.
26. Install new o-ring (16), springs (17 & 18), shim(s) (19), and piston
(20) in housing bore. Be sure to install the same number of shim(s)
as removed during disassembly.
NOTE: Not all models use
spring (17).
27. Install new boot (21) and new ring (22) on control section housing (10).
CHARGING VALVE ADJUSTMENT
The maximum accumulator pressure is adjusted by turning plug (24).
The high limit is raised by screwing plug into the body and lowered by
screwing plug out of the body.
- Attach a gauge to the accumulator port on the valve.
- Pump up the valve until a decisive click is heard,caused by the
shifting of the insert and spring.
- If the pressure is not as shown in the specifications chart on
page1, at the time the click is heard, turn adjusting plug (24) to
alter the pressure to within specification.