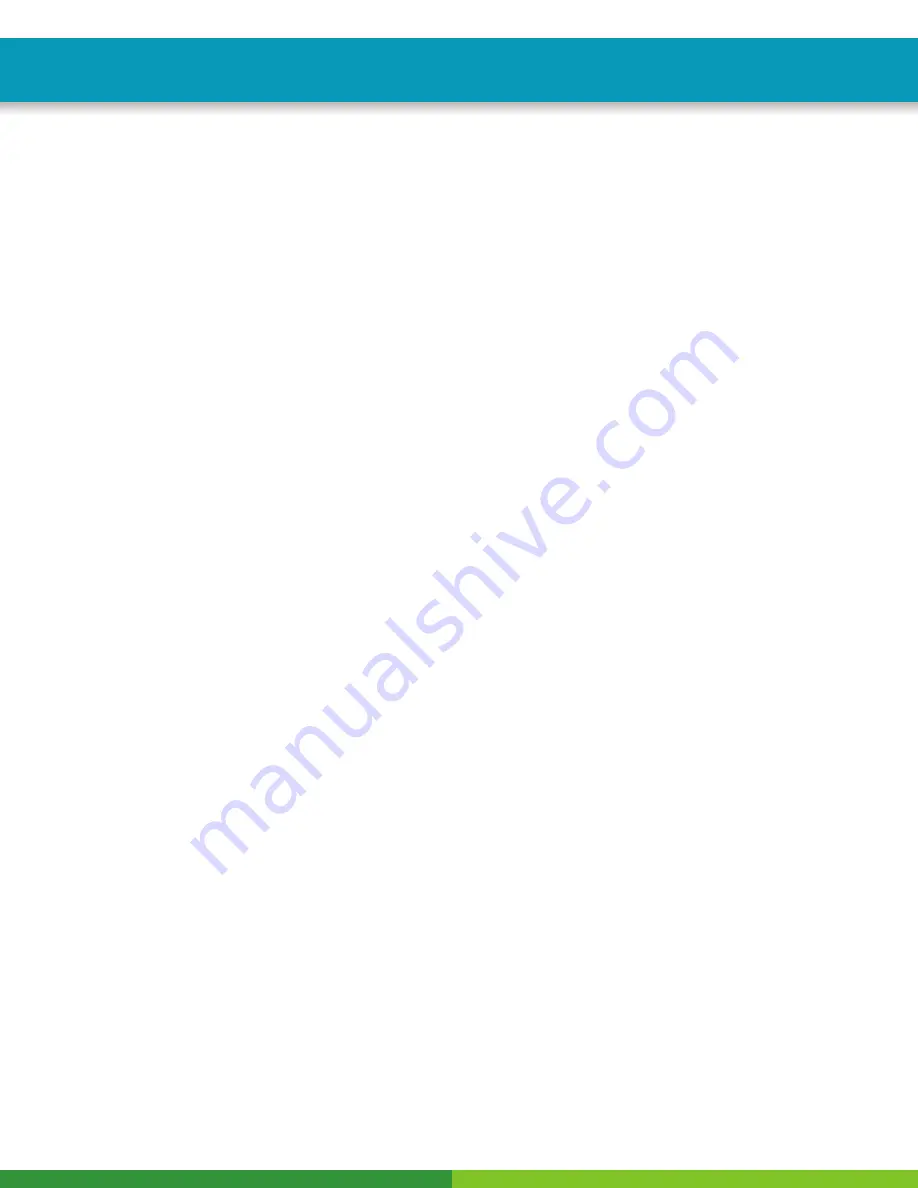
33
Appendix II
7 Appendix II
7.1 Cable Strain Relief Guidelines
It is important that cabling follow good strain relief practices to ensure maximum performance and durability.
Failure to provide adequate strain relief on the cables can result in future maintenance that is not covered
under warranty.
Strain relief is de
fi
ned as a small amount of slack in the cable at the area of connection. This lack of cable
tension allows for slight movement of the cable during times when components of the suspension and air
system may be in motion. A small amount of slack also eases access to other system components.
A taut cable can affect the lifespan of the cable. Cables without adequate strain relief can potentially stress
a cable connection enough that moisture could intrude. Unnecessary wear at bend points can be the result
of a cable under tension.
Cable strain relief is a universal practice. It applies to all WABCO product lines from Anti-Lock Brake
Systems (ABS) to Roll Stability Systems (RSS).
7.1.1 Excess Cable Length
In cases where the length of cable exceeds what is required, the excess must be bundled in an ef
fi
cient
manner. It should not be draped or wrapped around components or left unsecured. Any slack remaining in
the cable once the connections are made can be gathered up in a Z-shaped loop. Do not coil the cable and
pinch into a bowtie or dog-bone shape. All cable zip ties should be tightened in a manner only to the extent
that the cable is held suf
fi
ciently in place. Fasten the excess cable to an area that is free of sharp edges
and moving components.
WABCO has many lengths of cables available so it is a best practice to obtain a length that best suits the
requirements of the installation. Refer to the Parts List in Appendix IV to
fi
nd the different cable lengths that
WABCO offers.
7.1.2 Strain Relief at the ECU — Bracket Mounting
WABCO recommends that cable connections to a component, such as an ECU valve assembly, display
a visible amount of slack in the cable up to the
fi
rst tie or clip that secures the cable to the trailer structure
or air line. This
fi
rst anchor point should be a minimum 6-inches (152 mm) of cable length from the cable/
component connection and maximum of 12-inches (305 mm). This applies to all sensor, power, valve and
GIO cables. Regardless of whether zip ties or cable clips are used, cables should be secured at intervals
not greater than 18-inches (457 mm) to avoid cable vibration.