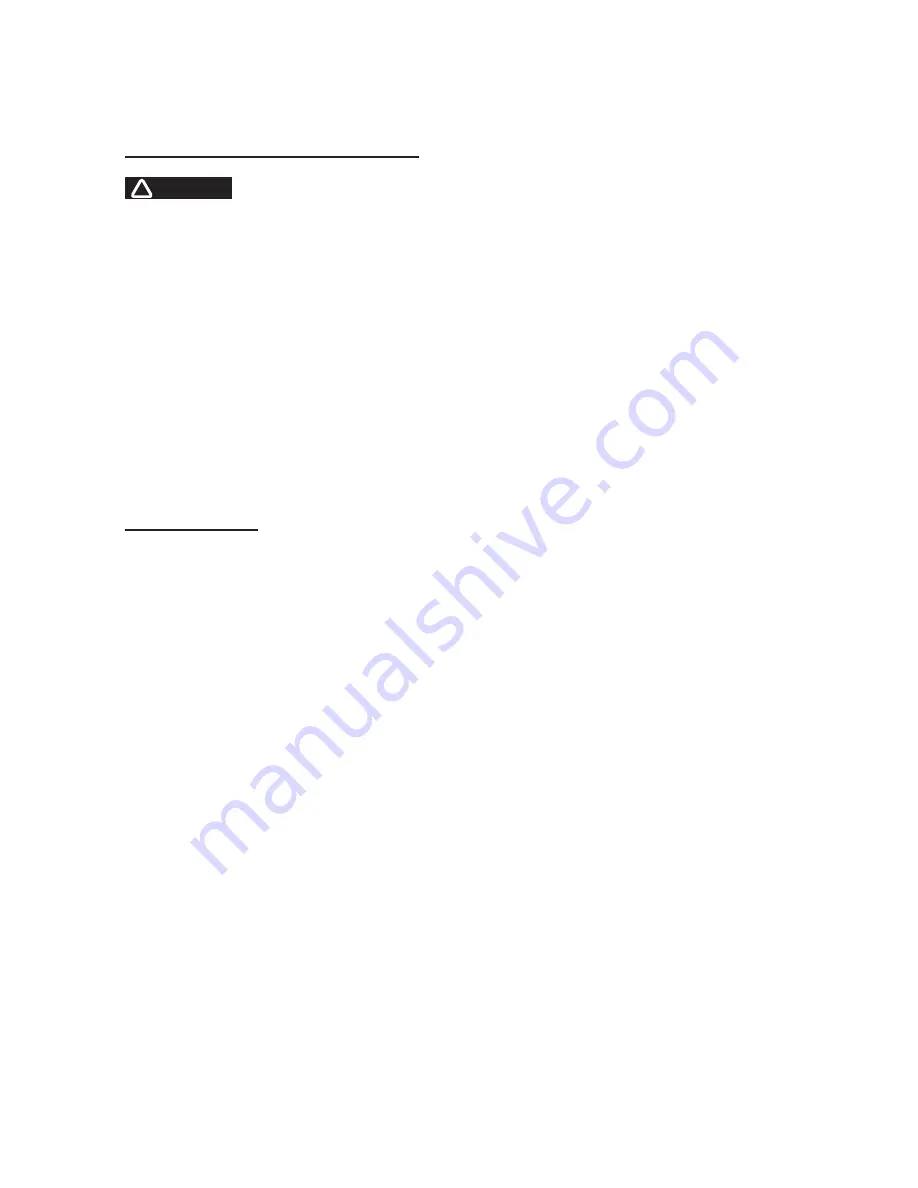
11
MAINTENANCE
=
Clean and inspect the tool daily. Make sure the tool is disconnected from the
air supply.
=
Blow the tool clean with compressed air and inspect for wear or damage. Use
non-flammable cleaning solutions to wipe the exterior of the tool only if
necessary. DO NOT SOAK tool with cleaning solutions. Such solutions can
damage internal parts.
=
Inspect the trigger and the safety mechanism to assure the system is complete
and functional. Check for loose or missing parts, and any parts that may be
sticking.
=
Keep all the screws tight. Loose screws may cause personal injury.
=
Place two or three drops of pneumatic oil (included) into the air inlet of the tool
daily.
CLEARING A JAMMED FASTENER
CAUTION
!
Disconnect the tool from the air supply.
1. Remove any remaining fasteners from the nailer.
a.
Pull feeder all the way to the rear until it latches
b.
Slide the fasteners to the rear, and remove fasteners from the
magazine
2. Use a pair of needle nose pliers and/or a flat screwdriver to remove bent
fasteners from the back of the nosepiece. If fastener cannot be removed as
described, it may be necessary to disassemble the magazine as follows:
a.
Remove the screws on the left front of the magazine and remove
screws on the right front.
b.
Remove screws from support
c.
Slide the magazine back, off the nosepiece.
d.
After clearing bent fastener, reassemble in reverse order.
Summary of Contents for 467-6789
Page 15: ...15 SCHEMATIC DRAWING...