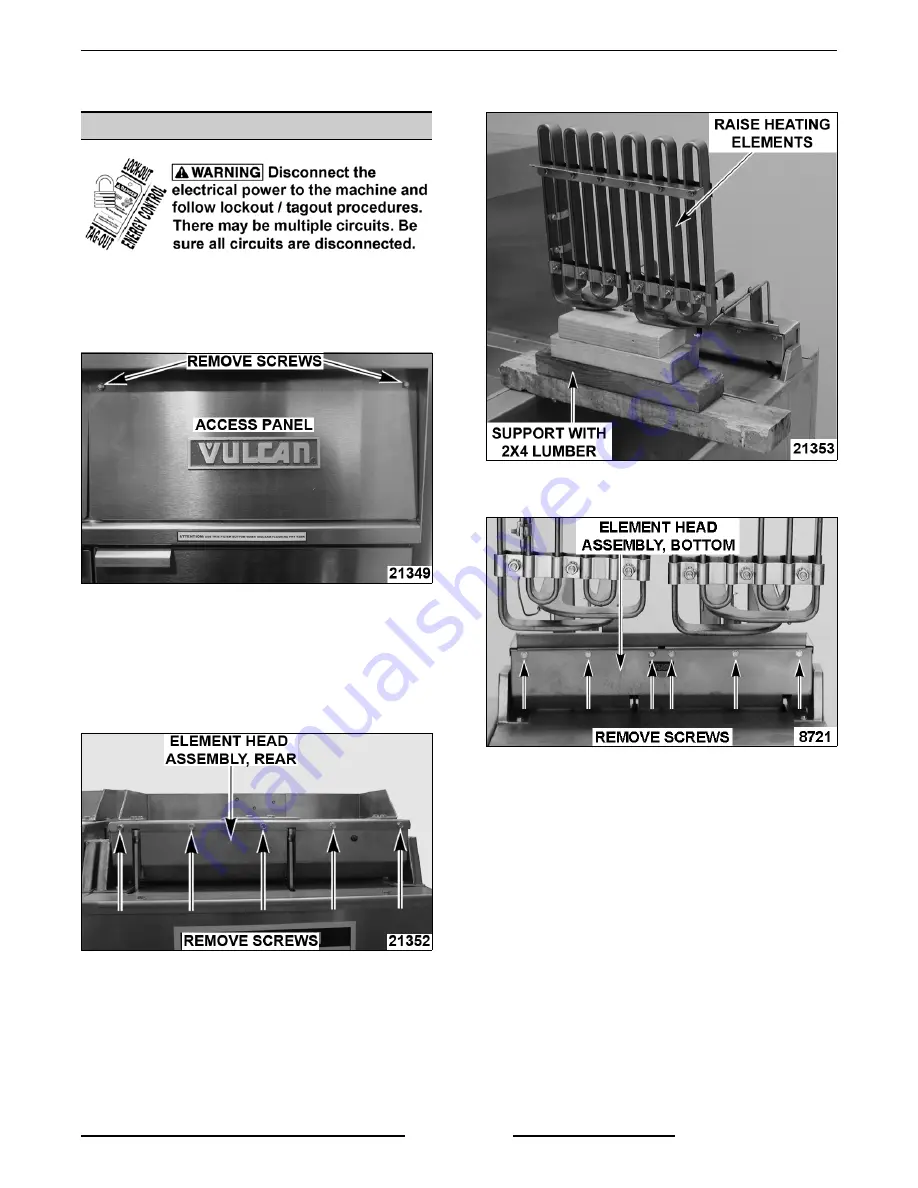
ERA & EBD SERIES ELECTRIC FRYERS - REMOVAL AND REPLACEMENT OF PARTS
REMOVAL AND REPLACEMENT OF PARTS
COVERS AND PANELS
Electrical Components Access Panel
1.
Remove screws at top of access panel and
lower panel.
2.
Lift from hinge then remove panel.
3.
Reverse procedure to install.
Element Head Cover
1.
Drain shortening from fry tank.
2.
Remove screws from rear of element head
assembly.
3.
Raise heating elements and place 2x4 lumber
under them for support.
4.
Remove screws from the bottom of element
head assembly.
5.
Grasp heating elements and remove 2x4
lumber. Lift the elements and pull toward rear of
fryer. Head cover will separate from element
head base.
A.
Lower the heating elements and place
them in fry tank.
NOTE
: Heating elements remain attached to
element head cover.
6.
Reverse procedure to install.
F25385 (May 2010)
Page 5 of 32