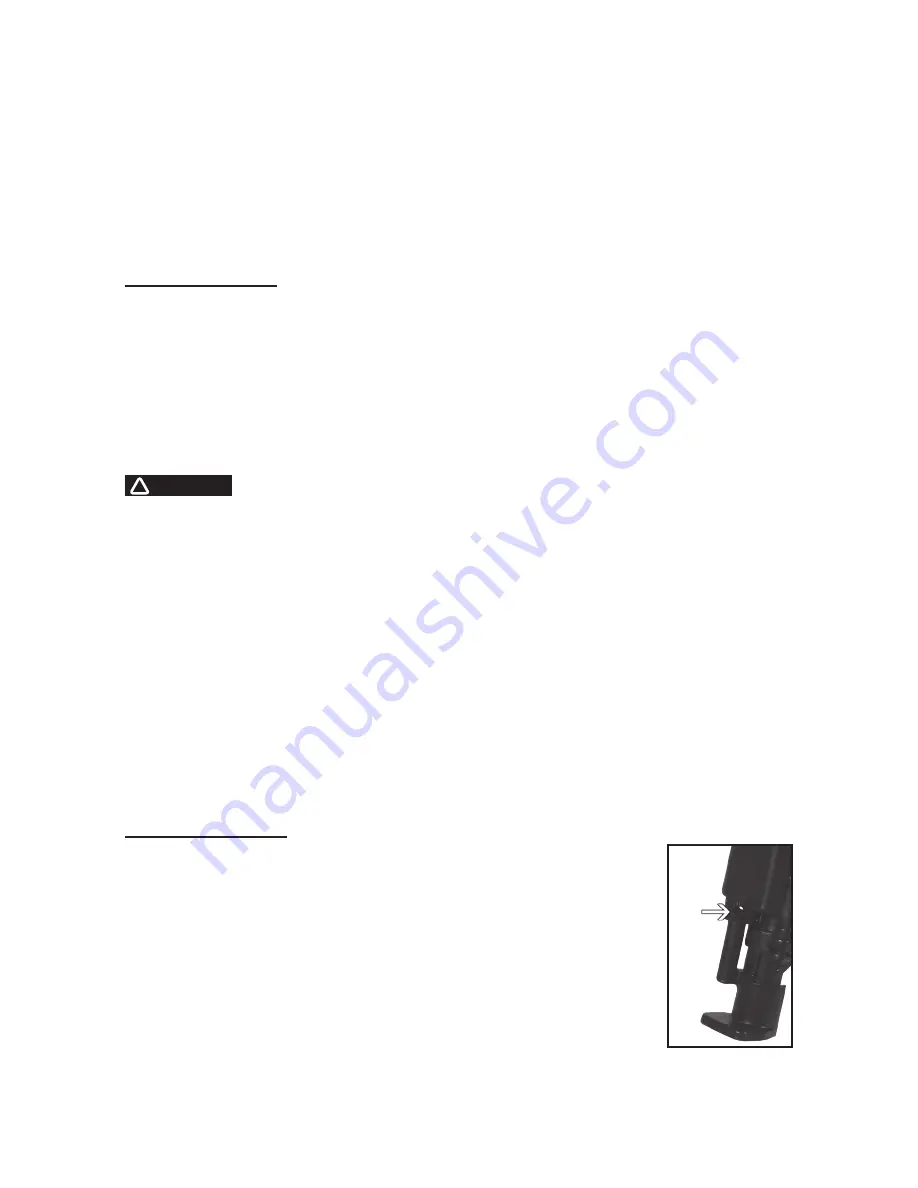
9
USING THE TOOL
This tool can be fired in two different ways:
1. Position the nose of the tool onto the work surface, push forward on the tool
to depress the safety, and squeeze the trigger to fire a nail. This “sequential”
method provides the most accurate fastener placement.
2. Squeeze and hold the trigger while pushing the nose of the tool against the
work surface. The tool will fire a nail every time the safety is depressed. This
“bump fire” method allows very fast, repetitive fastener placement.
CAUTION
!
=
Remove finger from the trigger when not driving fasteners.
=
Never carry tool with finger on trigger: tool will fire a fastener if the safety is
bumped.
=
Keep tool pointed in a safe direction at all times.
=
Never attempt to drive nails into materials too hard to penetrate, or at too
steep an angle, or too near the edge of the workpiece. The fastener can
ricochet causing personal injury.
=
Disconnect tool from air supply before doing any disassembly, maintenance,
clearing a jammmed fastener, leaving the work area, moving the tool to another
location, or handing the tool to another person.
=
Clean and inspect the tool daily. Carefully check for proper operation of trigger
and safety mechanism. Do not use the tool unless both the trigger and
the safety mechanism are functional, or if the tool is leaking air or needs any
other repair.
The depth to which a nail is driven is controlled by the depth
adjustment knob (
fig.6
), reachable through the window in the front
of the clear plastic guard. The depth of drive is factory adjusted to
maximum.
Test fire a nail into a sample of the material you will be working
on and check depth. If a change is desired, rotate the adjustment
knob clockwise (upward)
to increase the depth, counterclockwise (downward) to decrease it.
Test fire another nail and check depth again. Adjust as necessary.
FASTENER DEPTH
Fig.6
8. Re-connect the tool to the air supply, being careful to aim the nosepiece
in a safe direction, and careful to avoid touching the trigger or the safety
mechanism. This is to prevent harm from fasteners accidentally discharging
should the fastener driving mechanism cycle when the tool is connected to the
air supply.
9. The tool is ready to operate.
Summary of Contents for 039-8438
Page 16: ...16 SCHEMATIC DRAWING...