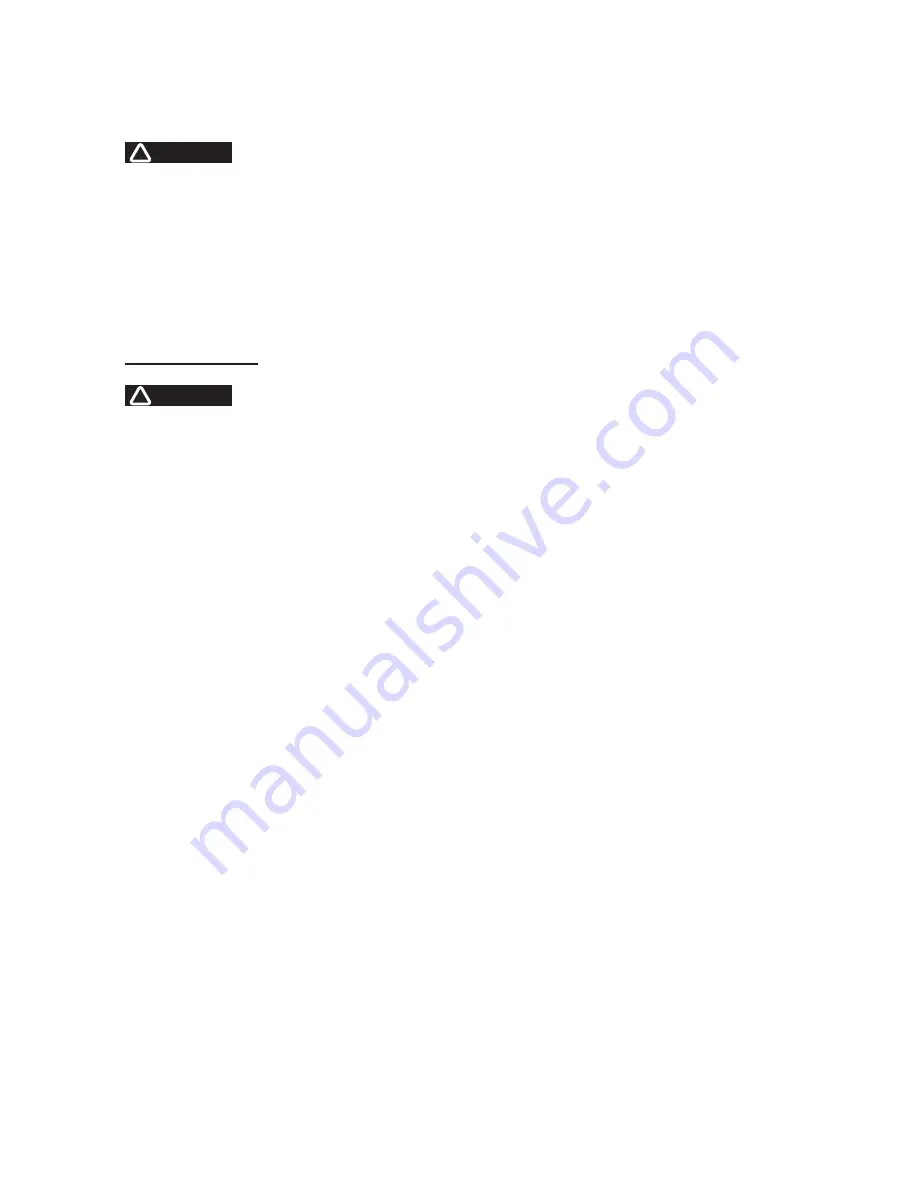
11
MAINTENANCE
CAUTION
!
Disconnect the tool from the air supply before cleaning and
inspecting the tool. Correct all problems before operating.
CLEAN AND INSPECT DAILY
=
Add pneumatic tool oil into the oiler regularly to assure that all moving.
Frequent, but not excessive lubrication is required for the best performance.
Oil added through the air line connection will lubricate the inside parts. An
automatic oiler is recommended, but 2 drops of oil may be added manually into
the tool’s air intake at the male quick-connect fitting (
F, fig.1
) at the beginning
of each workday and after about every hour of continuous use. Only a few
drops at a time are necessary. More than this will pool inside the tool and be
expelled from the tool’s exhaust during firing.
USE ONLY PNEUMATIC TOOL
OIL
. Do not use detergent oil or oil with other additives, as these can cause
accelerated wear on the seals.
=
Check the filter of the compressor weekly. Open drain cock to drain all water
and contaminants out of the air tank.
=
Wipe the tool clean.
=
Blow the tool clean using high compressed air, and then use non-flammable
cleaning solutions to wipe exterior of tool if necessary.
=
Do not soak tool in cleaning solutions. Such solutions can damage internal
parts. The exposed portion of the small piston rod and feed hook must be kept
clean.
=
Inspect trigger and safety mechanism daily to assure system is complete and
functional.
=
Keep all screws tight. Loose screws can cause personal injury or damage to
the tool. Check if there are worn and damaged parts. If any, please replace
immediately.
CAUTION
!
=
Keep the tool pointed away from yourself and others at all times.
=
Always connect the tool to air supply before loading fasteners.
=
Do not load fasteners with safety or trigger depressed.
=
Always wear approved safety glasses and hearing protection when preparing
or operating this tool.
=
Never use a tool that leaks air or needs repair.
Summary of Contents for 019-4274
Page 17: ...17 SCHEMATIC DRAWING...