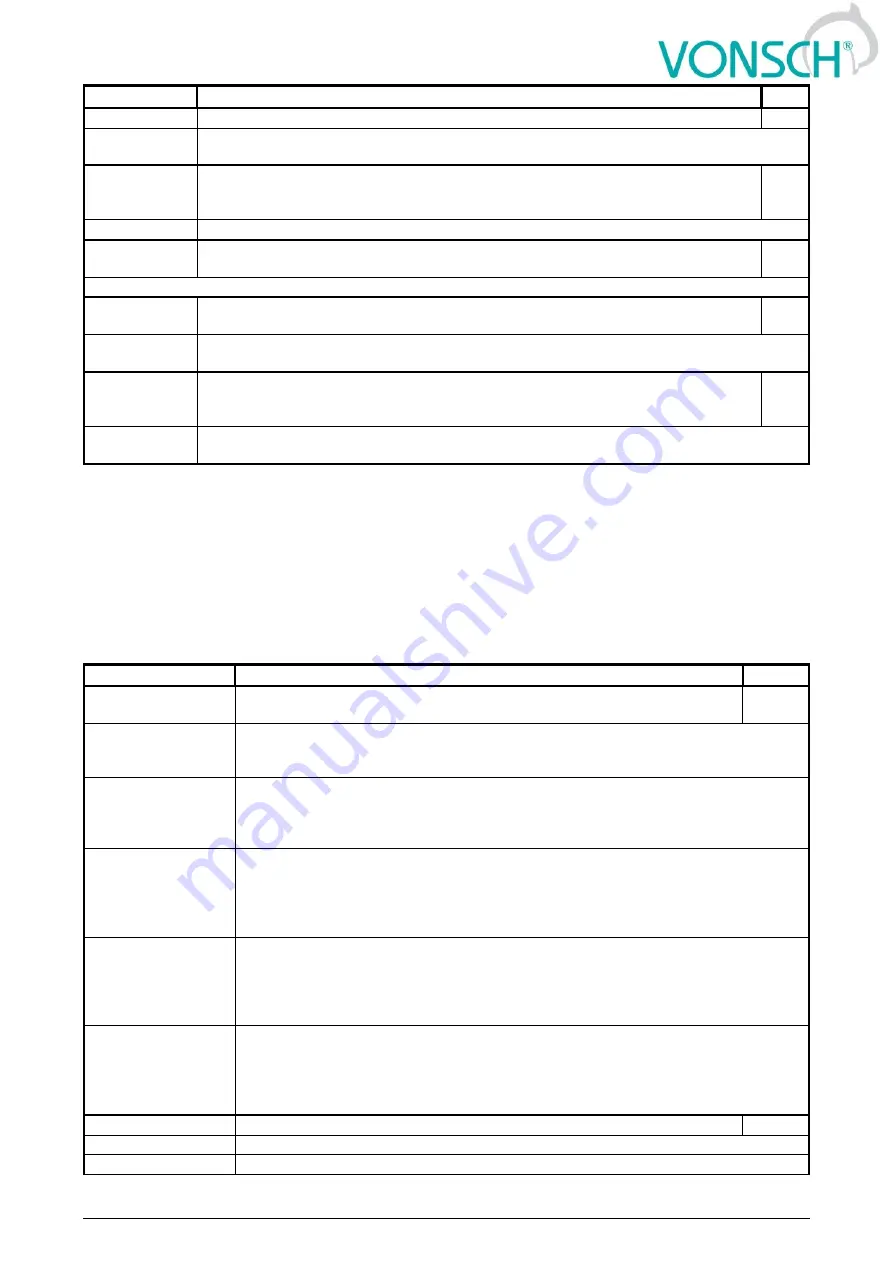
UNIFREM v.3.41x
10 May 2017
Page 57 from 180
Name [ID]
Description
Def.
[1574]
time set by Meas. time [1570] (page 57), auto off is performed.
Hz
0,00 ÷
Min. cos phi
[1575]
If the value of Cos Phi [67] (page 16) does not exceed this value for the time set by
Meas. time [1570] (page 57), auto off is performed. Negative values of this
parameter represent minimum regenerative power factor.
0,500
-
1,000 ÷ 1,000
Spec.
signal
[1576]
If the corresponding signal is active longer than the time set by Meas. time [1570]
(page 57), auto off is performed.
Look choises of parameter's Logical blocks [8] (page 20)
Meas.
time
[1570]
Measurement time; minimal period of time for the any of the auto off conditions to be
fulfilled to perform auto off.
1,0
min
0,1 min ÷ 120,0
min
Off time [1571]
Off time after auto-off. After the expiration of this timer after auto-off, inverter starts
and tries again whether the run conditions are met. Time to next start is shown in
ON / OFF time [1577] (page 15).
30,0
min
0,1
min
÷
2000,0 min
Time to next start can be reset by cancelling and resending the Start command or by a
short Reset command.
7.5 CONTROL AND REGULATION
Group of parameters number [11]
Settings of the motor control parameters.
7.5.1 CONTROL METHOD
Group of parameters number [450]
Control mode setting.
MENU \ SETTINGS \ CONTROL AND REGULATION \ CONTROL METHOD
Name [ID]
Description
Def.
Motor
control
method [451]
Setting the motor control method. Individual control methods differ by
principle, control quality, robustness and difficulty to setup.
V/f open
V/f open
V/f control (scalar) without the speed feedback. Less accurate slip compensation.
High stability and robustness of the control. Suitable for pumps, fans, conveyors and
low momentum applications.
V/f closed
V/f control (scalar) with the speed feedback from the motor rotation speed (IRC
sensor). Accurate slip compensation with a higher control quality, mainly at low
speed. Suitable for applications with lower requirements for the dynamics of
regulation. Very simple configuration.
VIM closed
Dynamic vector motor control with the rotation feedback designed for induction motor,
where the FLUX and the TORQUE of the motor are controlled using the motor
mathematical model. For high-demanding applications, where fast and exact control
of torque and speed is required, e.g. CNC machines, lift, elevators, traction drives.
The source of the feedback is set by the parameter Speed source [1000] (page 58).
VIM open
Dynamic vector motor control without the rotation feedback designed for induction
motor. Current motor speed is evaluated from the mathematical model. This control is
of worse quality in the zero frequency vicinity. Because of this it is not suitable for
applications where the motor has to hold the desired speed in the zero vicinity at the
very high load.
V-SMPM
Dynamic vector motor control with the rotation feedback designed for synchronous
motors, at which the FLUX and the TORQUE of the motor are controlled using the
motor mathematical model. For applications, where quick and accurate control of the
motor speed and torque are required. Requires special rotor position sensor types! Its
setting is in the group [826] (page 85).
Control type [835]
Selection of main controlled quantity. Position, speed or torque.
Speed
Position
Main controlled quantity is the rotor position Position [1147] (page 17).
Speed
Main controlled quantity is the rotor speed Freq. RT [937] (page 15).