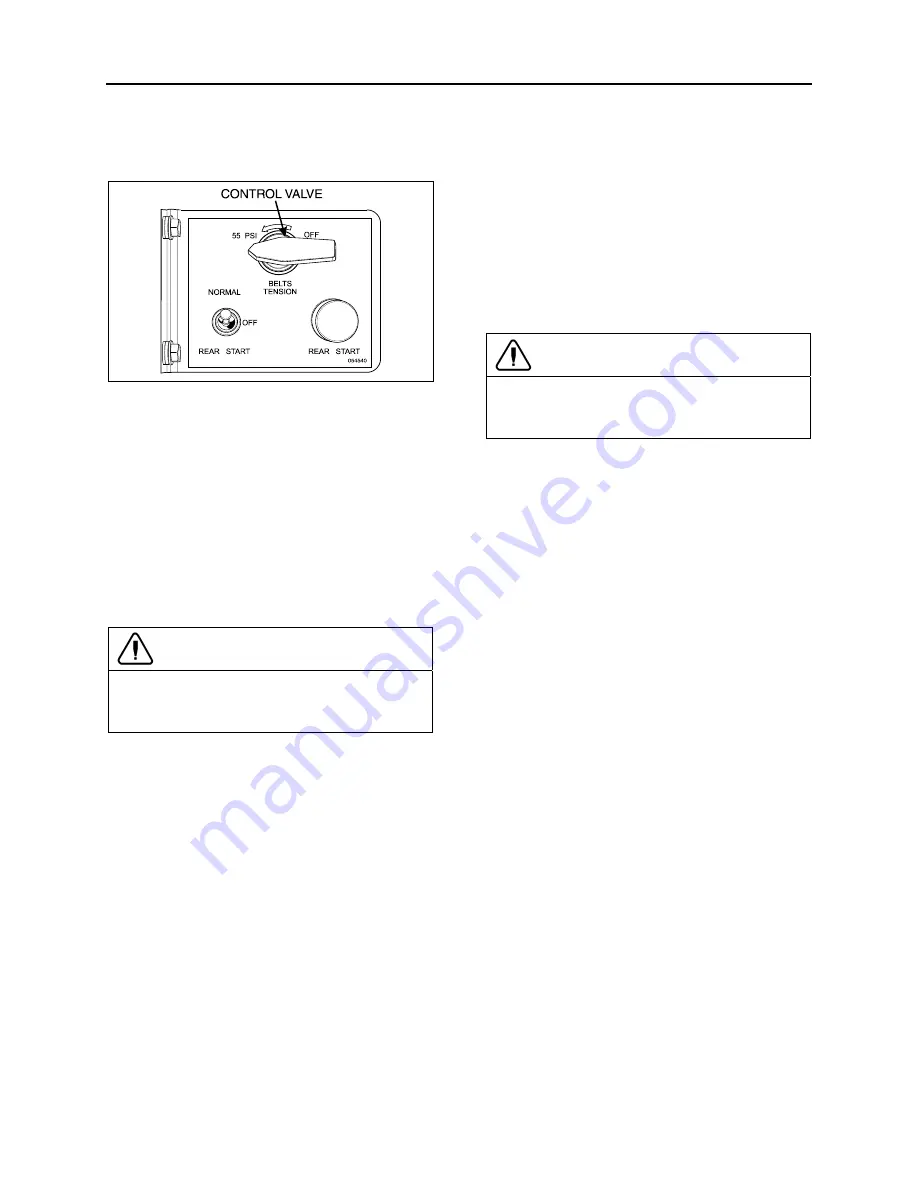
Section 01: ENGINE
PA1561
42
3. Drain the engine cooling system. Refer to
Section 05
COOLING
under "Draining Cooling
System".
FIGURE 20: ENGINE COMPARTMENT
01044
4. Locate the A/C compressor drive belt
tensioner control valve (Fig. 23). Turn handle
clockwise in order to release pressure in belt-
tensioner air bellows and loosen belts.
Remove the belt.
5. Release all pressure from the air system.
Refer to Section 12 BRAKES & AIR
SYSTEM for instructions.
6. Disconnect and remove the engine-air
intake duct mounted between air cleaner
housing and turbocharger inlet.
CAUTION
To avoid damage to turbocharger, cover the
turbocharger inlet opening to prevent foreign
material from entering.
7. Disconnect and remove the air intake duct
mounted between the turbocharger outlet
and the charge air cooler inlet.
8. Disconnect and remove the air intake duct
mounted between the charge air cooler outlet
and the engine intake.
9. Disconnect and remove section of coolant
pipe assembly mounted between the radiator
outlet and the water pump inlet.
10. Disconnect and remove a section of coolant
pipe assembly mounted between the
thermostat housing and the radiator inlet.
11.
Disconnect the coolant delivery hose
mounted between the coolant surge tank and
the water pump.
12.
Disconnect two vent hoses from the
thermostat housing and from the coolant pipe
assembly.
13.
Disconnect the fan-clutch electrical
connector.
14. Disconnect the radiator fan drive shaft.
15. Disconnect the small heater hose located on
the cylinder head at the back of the engine.
16. Disconnect and remove the exhaust pipe
mounted between the turbocharger outlet
and the exhaust bellows. If necessary, refer
to Section 04
EXHAUST SYSTEM
under “AFT
Removal and Installation".
CAUTION
To avoid damage to turbocharger, cover the
turbocharger outlet opening to prevent foreign
material from entering.
17. Disconnect the block heater connector
above the power steering pump.
18. Disconnect the steel-braided airline from the
A/C compressor air bellows.
19. Disconnect the oil delivery hose from the
valve located at the reserve tank drain.
20. Remove the power steering pump, leaving
the supply and discharge hoses connected t
it.
21. Close engine fuel supply shutoff valve on
primary fuel filter. Disconnect the fuel line
connected to inlet port. On vehicles equipped
with the optional water-separator-fuel-filter,
disconnect the connector and remove cable
ties from cradle.
22. Disconnect fuel return line from bulkhead
fixed on engine cylinder head end.
23. Disconnect the air compressor discharge
airline.
24. Disconnect the coolant hose to the sump
tank heater system.
25. Disconnect positive (+) cable (red terminal)
from starter motor solenoid.
26. Disconnect starter motor ground cables from
rear subframe ground-stud located close to
the starter motor.
27. Disconnect VIH (vehicle interface harness)
main connectors from MCM and VSS
(vehicle speed sensor).
28. On vehicles equipped with an automatic
transmission provided with a hydraulic output
retarder, disconnect steel-braided airline from