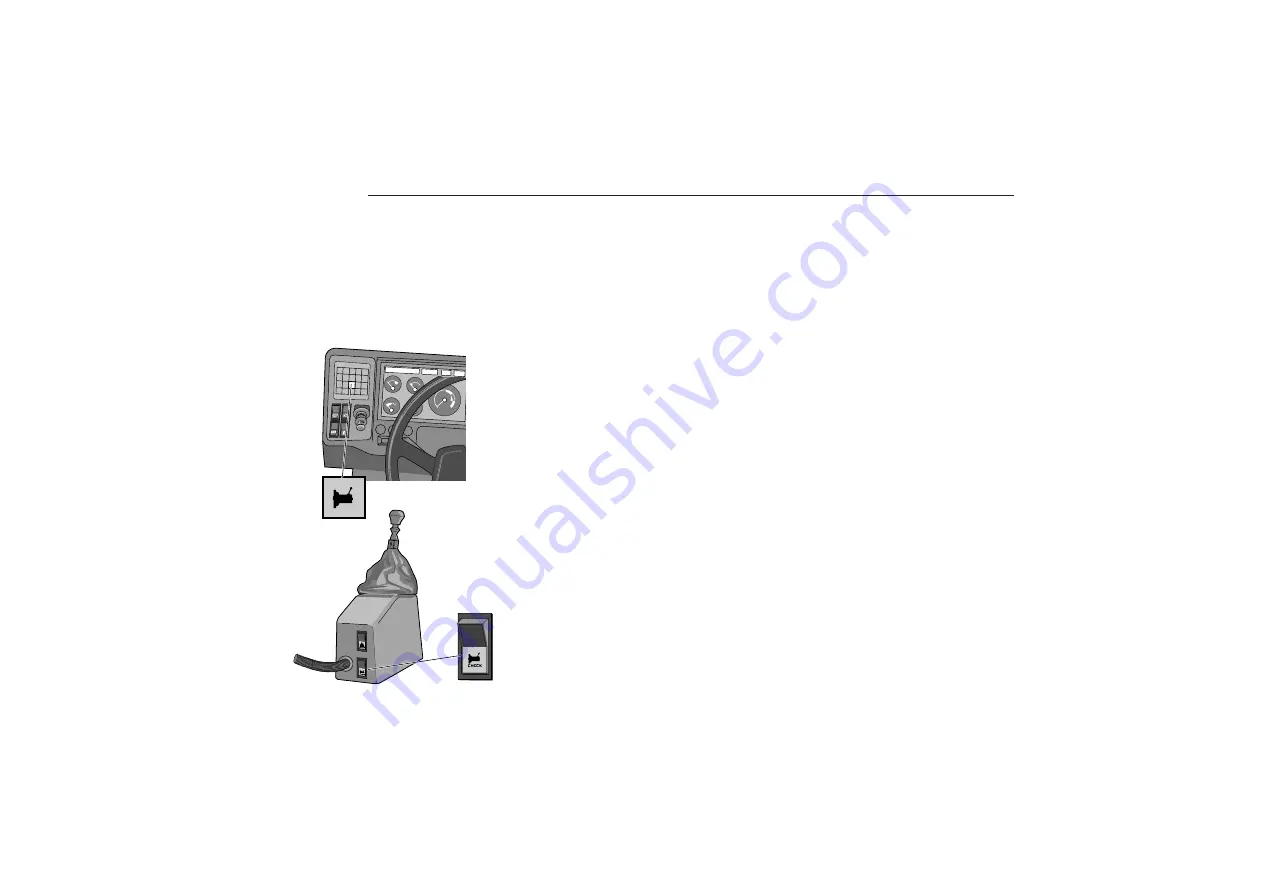
90
If anything happens
Fault in EGS system
The EGS system is powered via fuse ”10” on the main circuit
board (see page 78) and fuse ”43” on the EGS circuit board
(see page 80).
The EGS diagnostic lamp will go on for one second when
the engine is started. This is the time it takes for the EGS
system to perform its internal check. If the lamp does not go
out after this time, or if it goes on while driving, there is a
major fault in the system. In most cases, it will not then be
possible to change gear.
Diagnostics
There is a diagnostic program integrated in the electronic
control unit. It can be activated with the diagnostic switch as
follows:
–
Put the starter key in drive position.
–
With the gear lever in neutral and the bus stationary, press
the bottom of the diagnostic switch.
–
A fault will be indicated by the diagnostic lamp flashing
at two different rates (resulting in a fault code, see the
fault code table).
–
Slow rate indicates the fault code in tens, fast rate in
ones. Example: one slow and one fast flash indicates
fault code 11, two slow and three fast indicates fault
code 23.
–
Check to see whether there are any other faults present
by pressing the diagnostic switch again. If there any fur-
ther fault codes present, they will be displayed. (Repeat
the procedure until the first fault code returns.)
Gearbox G8 EGS
Diagnostics
switch
Diagnostics
lamp
Summary of Contents for B10M
Page 1: ...Driver s Manual...
Page 6: ...4 Pay attention to warning and indicator lights Their purpose is to warn of danger...
Page 131: ...129 TechnicalData Type plates 130 Specifications Data 132...
Page 142: ...140 Notes...
Page 143: ...141 Notes...
Page 144: ...142 Notes...
Page 145: ...143 Notes...
Page 146: ...144 Notes...
Page 147: ...3 Notes...