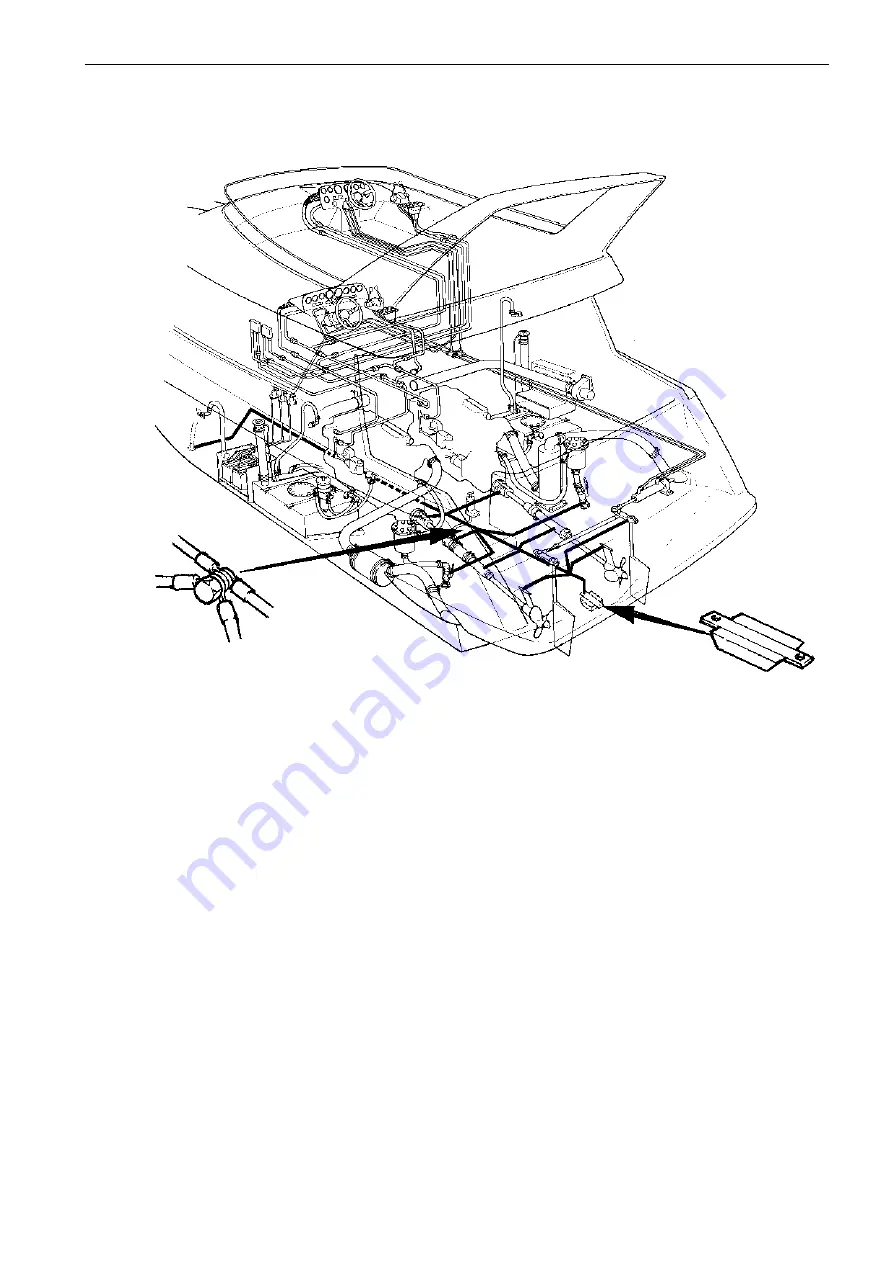
Electrochemical corrosion
97
To avoid galvanic corrosion on components sub-
merged in the water it is important that they are pro-
tected. Our recommendation is to bond all of them to
a protective anode, normally made of zinc.
Protection against electrochemical corrosion
NOTE! This bonding system with its individual compo-
nents should normally have no contact to the negative
circuit of the boats electrical system.
Local requirements, i.e. ABYC, may demand a battery
minus connected to the galvanic bond.
Summary of Contents for KAMD300
Page 1: ...Inboard Marine Diesel Engines TAMD31 41 42 KAMD43 44 300 Installation 1 1 B ...
Page 2: ......
Page 13: ...Engine application ratings 11 Examples of pleasure crafts Rating 5 ...
Page 135: ...133 Notes ...
Page 136: ...134 Notes ...
Page 137: ...135 Notes ...
Page 138: ...136 References to Service Bulletins Group No Date Concerns ...
Page 140: ...7741513 1 English 08 2001 ...