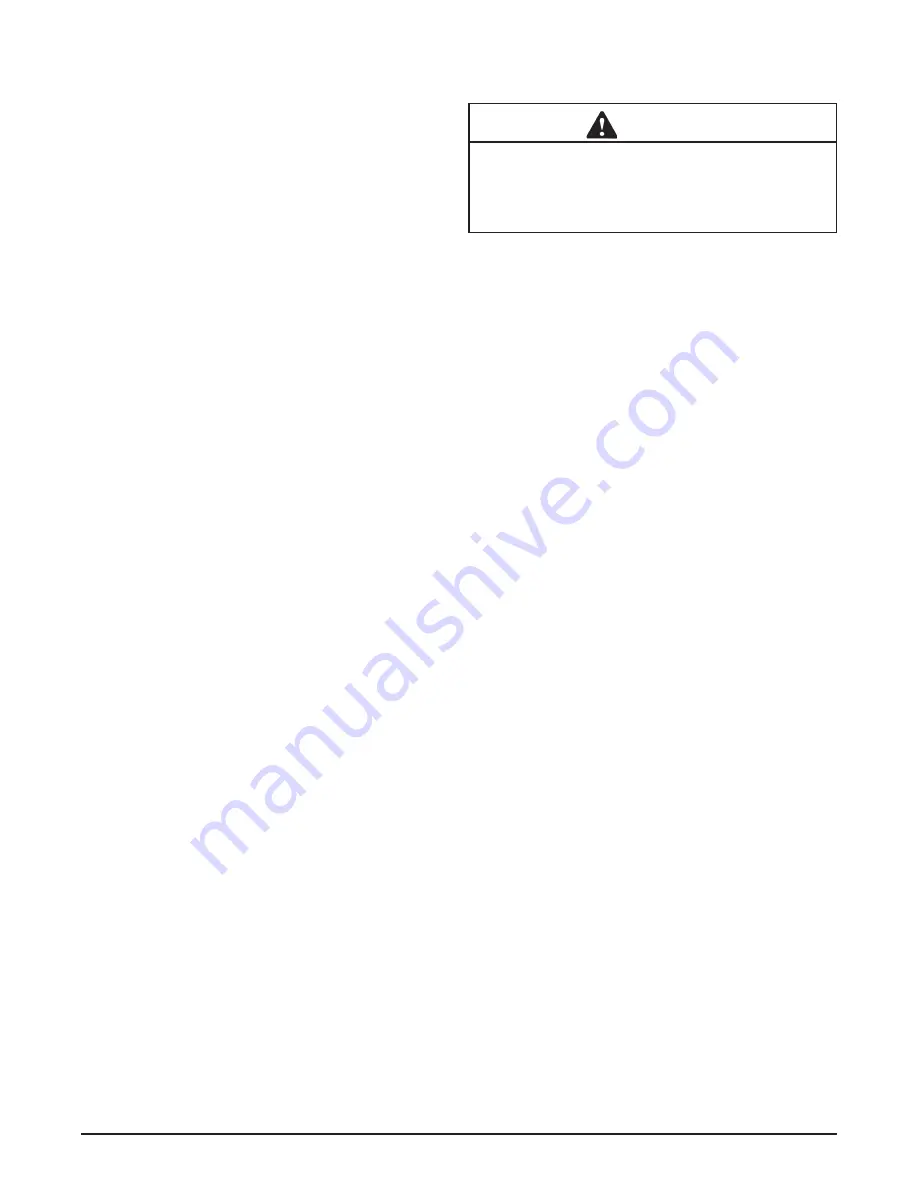
Operators Manual #513852
10
CBD Model Machines
C.
Place the top cover onto the tank.
D.
Press the Auger Movement button and the Cold
Selection button. Press the Cold Selector button
multiple times to toggle between “motor on” mode,
slush, and cold drink. The Cold Selector button
also changes consistency (density) in slush mode
from 1 (lowest density) to 3 (highest density).
NOTE
If it is the fi rst time operating the machine in Slush
mode, a one-minute motor calibration occurs before
starting the refrigeration cycle. During calibration
the “3” Slush Density Indicator blinks.
E.
The time it takes the product to be ready is
dependent upon many variables including the
mix temperature when poured into the tank, the
amount of sugar in the mix and the consistency
setting.
F.
After the product is ready, pull the spigot handle
to serve.
G.
Do not operate the machine when the mix level
is low. Refi ll the tank immediately.
3.6 REMOVING MIX FROM MACHINE
To remove the mix from the machine, refer to the follow-
ing steps:
A.
Press the Cold Selector button until the machine is
in “motor on” mode (Slush Density, Refrigeration,
Slush Mode, and Cold Mode LEDs are not lit).
C.
Drain the mix by opening the spigot. The spigot
can be locked open by moving the spigot lock
lever clockwise. A container should be placed
under the spigot to collect the liquid mix.
D.
When the mix is drained, close the spigot.
E.
Press the Auger Movement button to stop the
auger. Press the Main Power Switch to turn the
machine off.
3.7 DISASSEMBLY OF MACHINE PARTS
Inspection for worn or broken parts should be made each
time the machine is disassembled. All worn or broken
parts should be replaced to ensure safety to both the
operator and the customer and to maintain good machine
performance and a quality product.
NOTE
The frequency of cleaning the machine and ma-
chine parts must comply with local health regula-
tions.
After the mix has been removed from the machine, follow
the steps below to disassemble the parts.
A.
Remove the top cover.
B.
Remove the spigot handle cover by pressing the
sides of the cover and pulling downwards.
C.
Remove the spigot handle by moving it downwards.
D.
Remove the spigot assembly by turning the
assembly counterclockwise and pulling it out of
the tank.
E.
Remove the auger service knob by turning the
knob counterclockwise and pulling it out of the
tank.
F.
Remove the tank fastening knobs from the tank
clamps. Unclamp and remove the tank from the
machine. Remove the gasket from the bottom of
the tank.
G.
Pull the horizontal auger towards the front of the
machine to remove it. Remove the gear from the
back of the auger.
H.
Unscrew the fastening nut from the top of the
vertical auger and remove the auger. Remove
the gear from the bottom of the auger.
I.
Remove the o-rings from the spigot assembly
and auger service knob. Remove an o-ring by
squeezing the o-ring upward with a dry cloth.
When a loop is formed, roll the o-ring out of the
groove.
J.
Remove the drip tray and drip tray grid.
3.8 CLEANING AND SANITIZING THE
MACHINE PARTS
Place all loose parts in a pan or container and take to
the wash sink for cleaning. Local and state health codes
dictate the procedure required. Some health codes require
a four-sink process (pre-wash, wash, rinse, sanitize, and
air-dry), while other codes require a three-sink process
(without the pre-wash step). The following procedures
are a general guideline only. Consult your local and state
health codes for procedures required in your location.
A.
Prepare Stera-Sheen or equivalent cleaner in
2 gallons of 90° to 110°F (32° to 43°C) water
following manufacturers instructions.
CAUTION
Hazardous Moving Parts.
Revolving augers can grab and cause injury. Turn
the machine Off using the Main Power Switch be-
fore disassembling for cleaning or servicing.
Summary of Contents for Stoelting CBD117-37
Page 1: ...Model CBD OPERATORS MANUAL Manual No 513852 Rev 3 ...
Page 2: ......
Page 6: ......
Page 12: ...Operators Manual 513852 6 CBD Model Machines ...
Page 18: ...Operators Manual 513852 12 CBD Model Machines ...
Page 20: ...Operators Manual 513852 14 CBD Model Machines ...