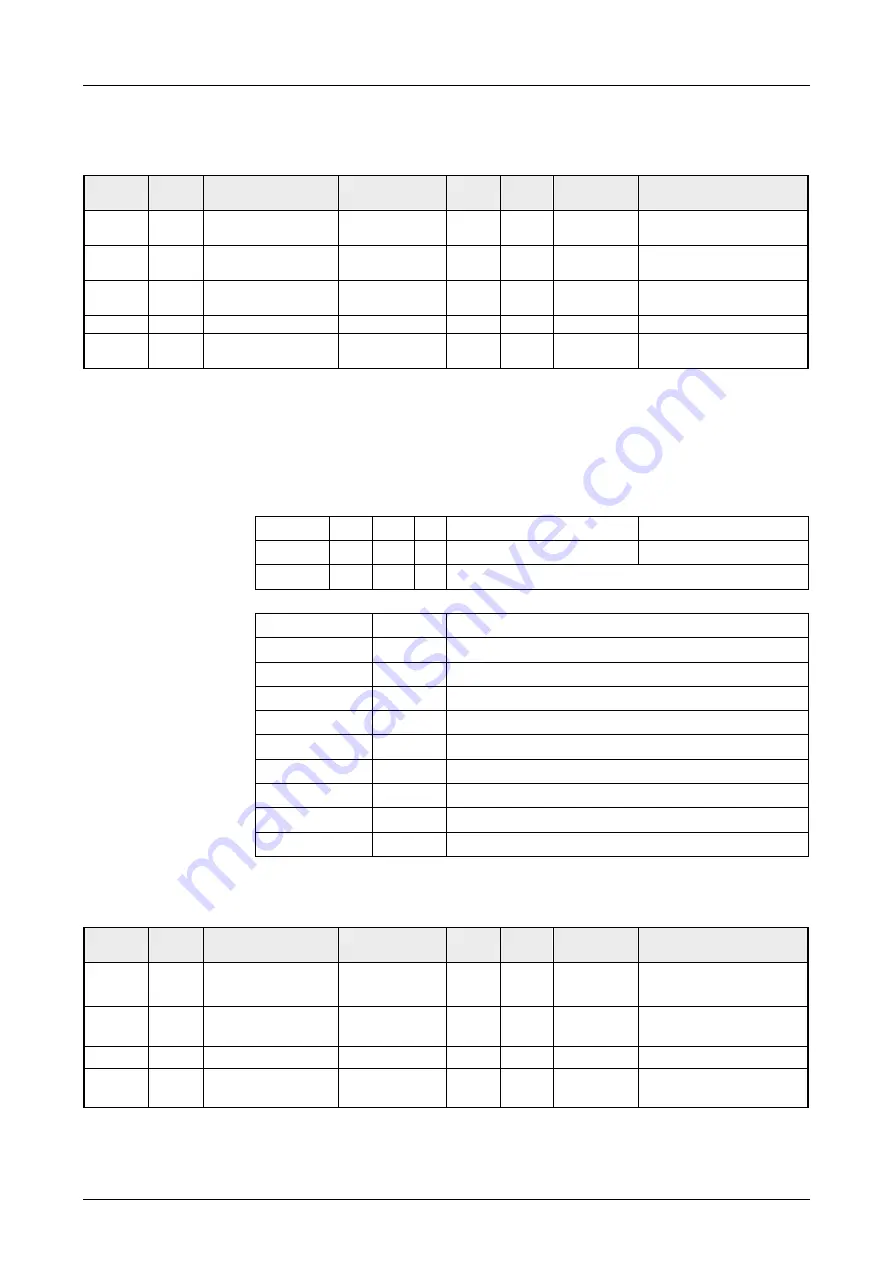
Chapter 4 Deployment
Manual VIPA System 300S SPEED7
4-32
HB140E - CP - RE_342-1CA70 - Rev. 09/46
Index
Sub-
index
Name
Type
Attr.
Map. Default
value
Meaning
0x2000
0 Number
of
elements
Unsigned8
ro
N
8
Number of available
entries.
1
1. COB-ID
Unsigned32
rw
N
0
COB-ID which
generates OB57
2
2. COB-ID
Unsigned32
rw
N
0
COB-ID which
generates OB57
... ...
...
... ... ...
...
8
8. COB-ID
Unsigned32
rw
N
0
COB-ID which
generates OB57
With this index COB-IDs may be defined which release the OB57 in the
PLC.
UNSIGNED32
MSB
LSB
Bits
31 30 29 28-11
10-0
11-bit-ID 0/1 0/1 0 000000000000000000 11-bit
Identifier
29-bit-ID 0/1 0/1 1 29-bit
Identifier
Bit number
Value Meaning
31 (MSB)
0
PDO exists / is valid
1
PDO does not exist / is not valid
30 0
1
no RTR allowed on this PDO
29
0
11-bit ID (CAN 2.0A)
1
29-bit ID (CAN 2.0B)
28-11
0
if bit 29=0
X
if bit 29=1: bits 28-11 of 29-bit-COB-ID
10-0 (LSB)
X
bits 10-0 of COB-ID
Index
Sub-
index
Name
Type
Attr.
Map. Default
value
Meaning
0x2001 0x00 Number
of
elements
Unsigned8
ro
N
0
Number of available
entries
0x01
1. Node-ID for
PLC-STOP
Unsigned8 rw N 0
Node-ID
(value range:1...127)
... ...
...
... ... ...
...
0x10
16. Node-ID for
PLC-STOP
Unsigned8 rw N 0
Node-ID
(value range:1...127)
At PLC-RUN
Æ
PLC-STOP transition the CAN devices listed here, were
set to state preoperational by the NMT command
Preoperational
.
Initialize Rx-COB-
ID for OB57
Structure of
COB-ID
Node-ID - PLC-
STOP
Summary of Contents for 300S SPEED7 - CP
Page 1: ...VIPA System 300S SPEED7 CP 342 1CA70 Manual HB140E_CP RE_342 1CA70 Rev 09 46 November 2009...
Page 4: ...Contents Manual VIPA System 300S SPEED7 ii HB140E CP RE_342 1CA70 Rev 09 46...
Page 8: ...Safety information Manual VIPA System 300S SPEED7 4 HB140E CP RE_342 1CA70 Rev 09 46...
Page 92: ...Chapter 4 Deployment Manual VIPA System 300S SPEED7 4 54 HB140E CP RE_342 1CA70 Rev 09 46...
Page 94: ...Index Manual VIPA System 300S SPEED7 A 2 HB140E CP RE_342 1CA70 Rev 09 46 M Stich...