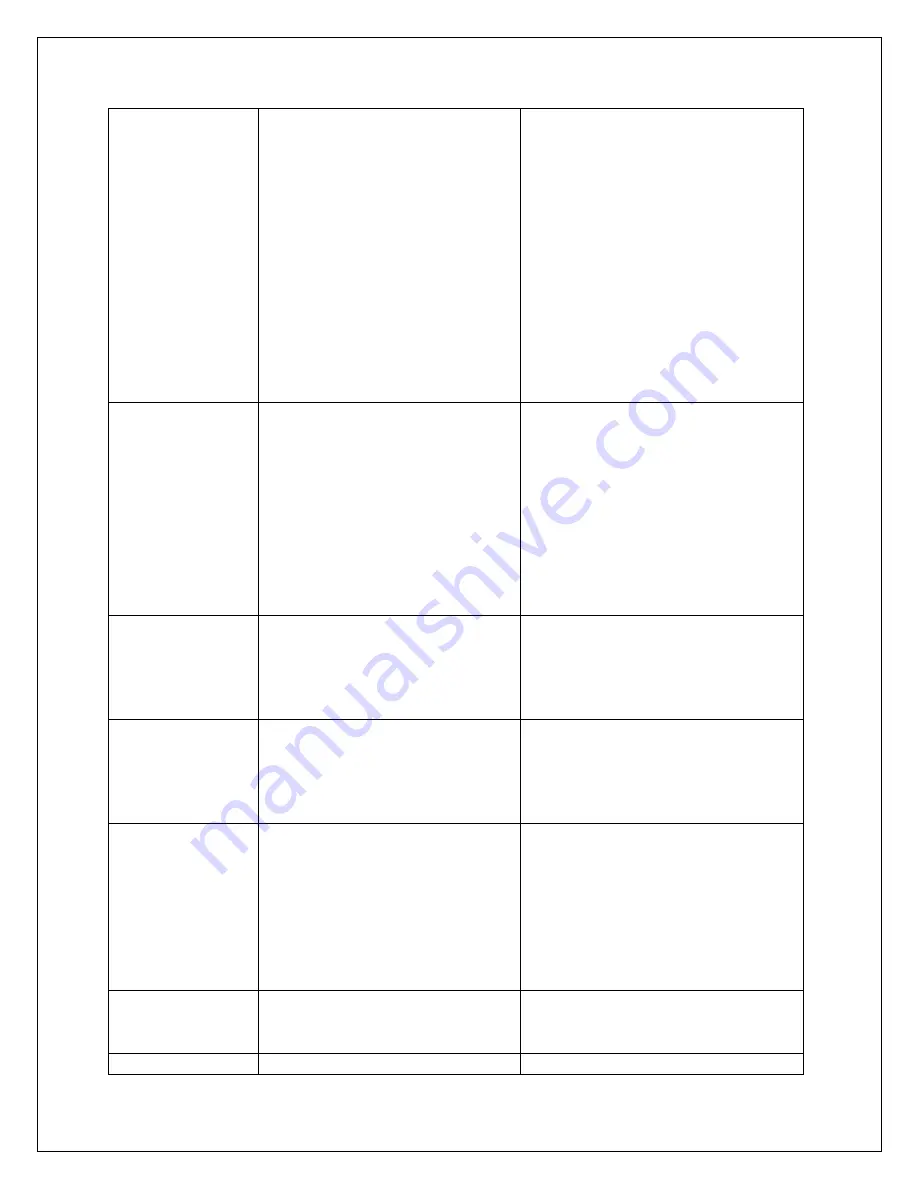
- 12 -
high or not
cooling and
running
continually
b. Cellar too large
c. Ambient temperature too high
d. Exhaust restricted
e. Malfunctioning
fans
f.
Evaporator or condenser airflow
g. Dirty
Condenser
h. Iced
evaporator
i. Refrigeration
system
restriction
j. Refrigerant
leak
k. Undercharge or overcharge
l. Failed
components
b. Check for excessive size
c. Check installation location
d. Leave minimum 3 feet clearance for
the hot air exhaust side and leave
minimum 1 foot clearance for the
ambient air intake side
e. Check for both evaporator and
condenser fans
f. Check for air restrictions, air short-
circulation, grille directions
g. Clean
condenser
h. Defrost and reset temperature
i. Call
service
j.
Call service
k. Call service
l. Check compressor windings, start
relay and overload protector
7. Unit running
too long
a. Improper cellar insulation & seal
b. Exhaust restricted
c. Cellar too large
d. Ambient temperature higher >
90
°
F
e. Dirty Condenser
f. Improper condenser air flow
a. Check insulation, gasket and door
opening
b. Leave minimum 3 feet clearance for
the hot air exhaust side and leave
minimum 1 foot clearance for the
ambient air intake side
c. Check for excessive size
d. Check for installation location
e. Clean condenser
f. Check for fan and air short
circulation
8. Condenser
fan running
but
compressor
not running
a. Incorrect or loose wirings
b. Failed
components
c.
Liquid refrigerant in the
compressor
a. Check all wirings and connections
b. Check start relay, start capacitor,
overload protector, compressor.
c. Call
service.
9. Compressor
running but
condenser
fan not
running
a. Fan blade stuck
b. Incorrect or loose wirings
c. Failed
motors
d. Fan cycle control
a. Check for proper clearance
b. Check all wirings
c. Call
service
d. Check for setting
10.Temperature
high,
compressor
stopping
and starting
but very
short
running time
a. Failed
components
b. Improper
condenser
airflow
c. Dirty
condenser
d. Overcharge of refrigerant
e. Discharge or suction pressure
too high
a. Check compressor windings, start
relay and overload protector.
b. Check for condenser fan
c. Clean
condenser
d. Call service for removing refrigerant
e. Call service for information
11.Evaporator
fan running
too long
a.
Post-compressor fan running
mode for humidity modulation
a. Reset FON
12. Evaporator
a. Incorrect or loose wirings
a. Check all wirings and connections