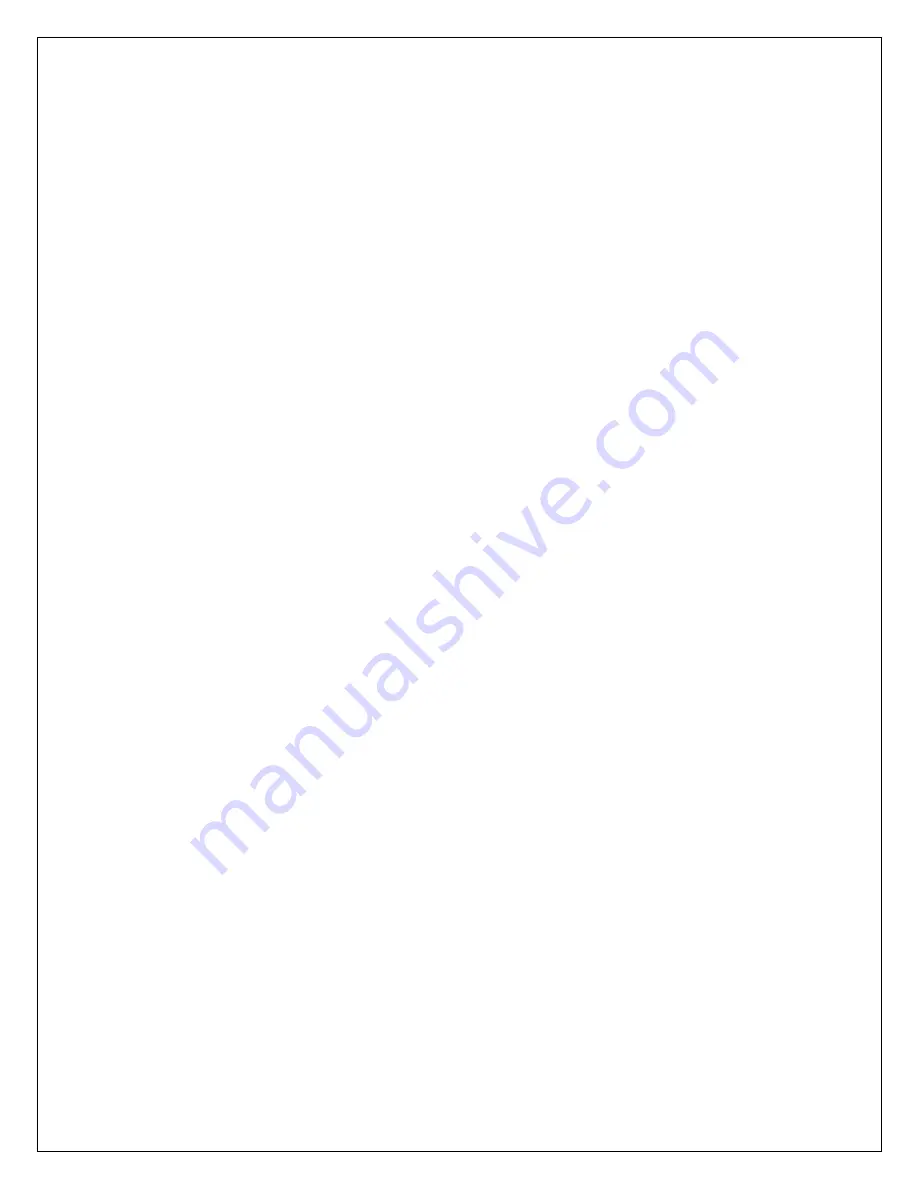
- 9 -
4. Piping, Evacuating, Charging and Starting
CAUTION:
•
ALWAYS USE THE SUPERHEAT AND SUBCOOLING, PRESSURE
READINGS TO CHARGE REFRIGERANT PROPERLY, THE LISTED
CHARGES ARE FOR REFERENCE ONLY.
•
CHARGE 15% MORE REFRIGERANT IF THE UNIT IS EQUIPPED WITH A
LOW AMBIENT CONDITION KIT AND INSTALLED IN THE SUMMER.
NOTES:
•
THE LINE CONNECTION SIZES OF LIQUID FILTER & INDICATOR, THE
VALVE CONNECTION SIZES OF CONDENSING UNIT AND THE LINE
CONNECTION SIZES OF EVAPORATOR UNIT ARE NOT NECESSARY
THE SAME AS THE ABOVE SPECIFIED LINE SIZES.
•
IF THE CONDENSING UNIT IS INSTALLED ABOVE THE EVAPORATOR
UNIT, USE THE SUCTION LINE ONE LISTED SIZE SMALLER.
•
EXPANSION VALVE AND SOLENOID VALVE ARE INSTALLED ON
LIQUID LINE IN THE EVAPORATOR UNIT.
1) The installation order starts from condensing unit (including receiver and
discharge valve), liquid line filter-drier, moisture-liquid indicator, liquid line,
to evaporator unit (including liquid line connection, solenoid valve,
expansion valve, and suction line connection), returning to insulated
suction line, suction valve and then back to condensing unit.
2) If the condensing unit is located below the evaporator unit, use inverted U
trap to prevent liquid from flooding back to the compressor; if the elevation
difference is more than 10 ft or the line set exceeds 75 ft, use both
inverted U trap and suction accumulator.
3) If the condensing unit is located more than 10 ft above the evaporator unit,
use U trap to aid oil returning to the compressor.
4) Complete pipe brazing, check solenoid valve and expansion valve
restrictions and test leak.
5) Hook up the drain line and check if water drains.
6) Both discharge and suction valves must be in the middle positions during
evacuating and charging.
7) Charge the system after pipe brazing, leak testing and evacuating. Liquid
must always be charged into the hide side.
8) The subcooling at the condensing unit shall be around 10°F. The charge
may be complete when there are no more bubbles forming in the liquid
indicator.
9) Head pressure range: 125 ~ 150 psig at 70 ~ 90 °F condensing unit
ambient temperature.
10) The evaporator superheat is set around 8 ~ 10 °F at factory.
11) Suction pressure: 30 ~ 35 psig.
12) The temperature split crossing the evaporator shall be 8 ~ 10°F at 55°F
wine room temperature.