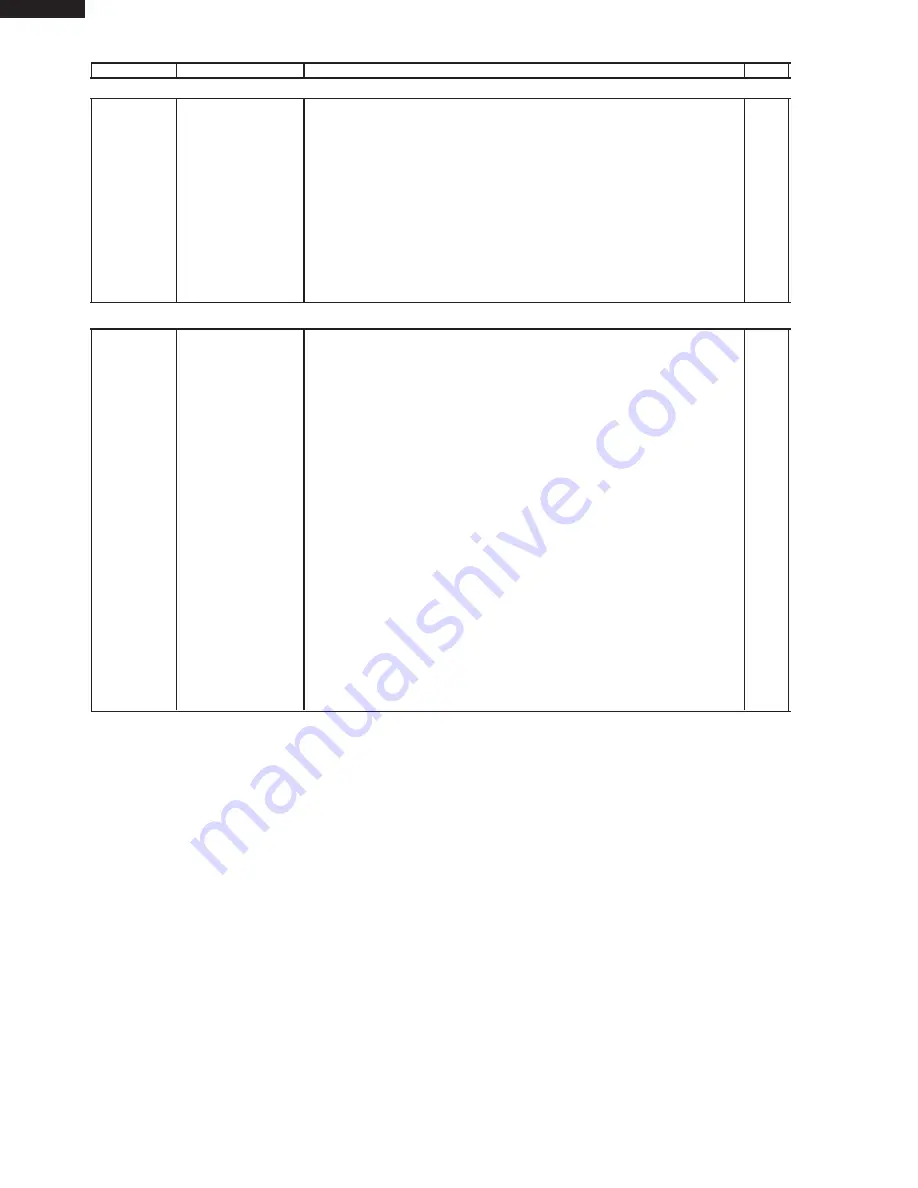
36
Rev 1 (May 2011)
REF. NO.
PART NO.
DESCRIPTION
Q'TY
CODE
MISCELLANEOUS
6- 1
FAMI-A088WRM0 Low rack (Broiling trivet)
1
AW
6- 2
FAMI-A087WRM0 High rack (Baking rack)
1
AW
6- 3
FW-VZB342WRE0 Thermistor harness
1
AN
6- 4
FW-VZB880WREZ Main wire harness
1
BB
6- 5
QW-QZA198WRE0 High voltage wire B
1
AN
6 -6
QW-VZA108WRE0 Grounding wire (Cooling fan motor)
1
AF
6- 7
TCAUHB011MRR0 Monitor caution label
1
AB
6- 8
TCAUAB075MRR0 NHW caution label
1
AD
6- 9
UDSKDB002MRK3 Viking CD (Installation, Operation, Cookbook, etc.) 1
AQ
6-10
LHLDKA009WRF0 Cord holder
1
AC
6-11
TCAUHB008MRR0 User caution
1
AH
6-12
TCAUSB012MRR0 BIK label
1
AH
6-13
TCAUAB048MRR0 GND caution label
1
AH
6-14
TCAUAB033MRR0 UL screw label
1
SCREWS NUTS AND WASHERS
7- 1
XOTWW40P10000 Screw; 4mm x 10mm
14
AA
7- 2
XOTS740P12000 Screw; 4mm x 12mm
4
AA
7- 3
XCTWW40P08000 Screw; 4mm x 8mm
2
AA
7- 4
XHTS740P08RV0 Screw; 4mm x 8mm
4
AA
7- 5
LX-CZ0052WRE0 Special screw
2
AA
7- 6
XWVS760-07000 Washer; 6mm x 0.7 mm
1
AA
7- 7
LX-WZA004WRE0 Washer
1
AA
7- 8
LX-CZA074WRE0 Special screw
6
AA
7- 9
XBPS730P14K00 Screw; 3mm x 14mm
1
AA
7-10
XBPS740P25000 Screw; 4mm x 25mm
2
AA
7-11
XBTWW40P06000 Screw; 4mm x 6mm
3
AA
7-12
XCTS740P08000 Screw; 4mm x 8mm
7
AA
7-13
LX-NZ0082MRE0 Special nut
1
AA
7-14
LX-CZA070WRE0 Screw; UL
2
AA
7-15
XNES740-32000 Nut; 4mm x 3.2mm
2
AB
7-16
LX-BZ0531FCZZ Screw; 4mm x 8mm
6
AA
7-17
XCPS730P06000 Screw; 3mm x 6mm
3
AA
7-18
LX-CZA038WRE0 Special screw
1
AA
7-19
XFPS740P08K00 Screw; 4mm x 8mm
3
AA
7-20
XBPS740P06000 Screw; 4mm x 6mm
1
AB
7-21
XCBWW30P06000 Screw; 3mm x 6mm
4
AA
7-22
XFPS740P08000 Screw; 4mm x 8mm
6
AA
7-23
XFPS760P14JS0 Screw; 6mm x 14mm
2
AB
7-24
XOTS740P12000 Screw; 4mm x 12mm
21
AA
7-25
XFPS730P08000 Screw; 3mm x 8mm
2
AA
Summary of Contents for Professional VMOC205SS
Page 3: ...3 Rev 1 May 2011 Notes ...