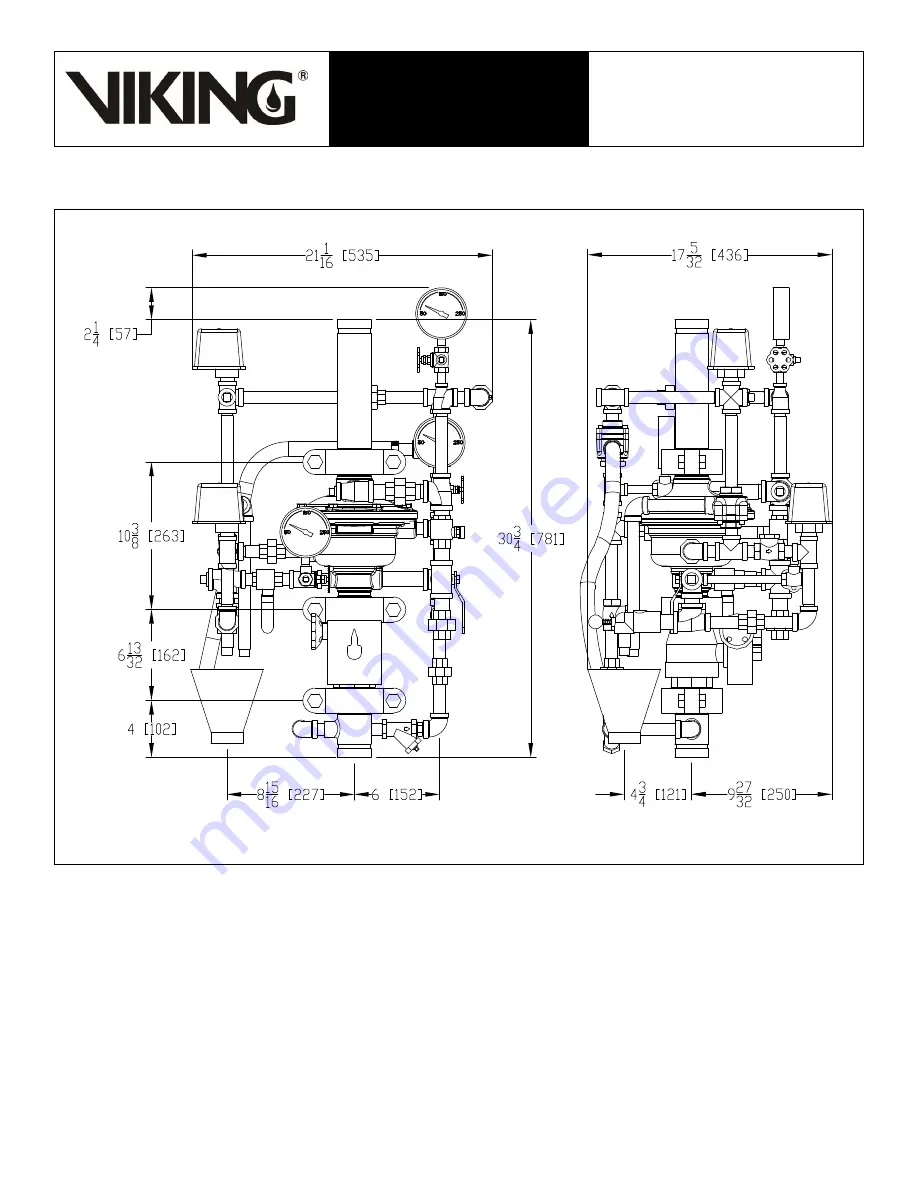
TECHNICAL DATA
2” MoDEL G-2000 Dry vALvE
rISEr ASSEMBLy
Page 11 of 13
The viking Corporation, 210 N Industrial Park Drive, Hastings MI 49058
Telephone: 269-945-9501 Technical Services: 877-384-5464 Fax: 269-818-1680 Email: [email protected]
visit the viking website for the latest edition of this technical data page www.vikinggroupinc.com.
Form No. F_011110 17.04.27 Rev 17.1
Figure 10 - Installation Dimensions