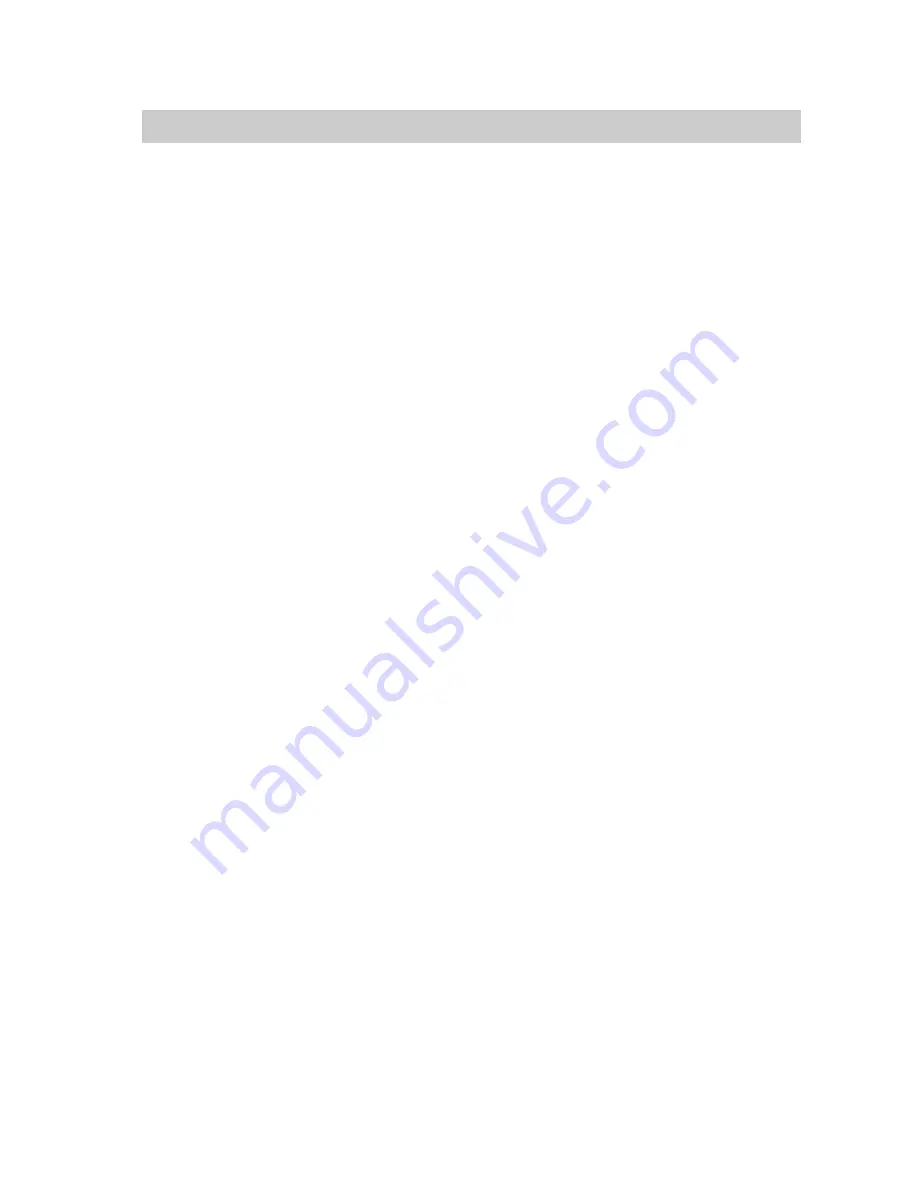
31
Appendix
Keyword index
B
Boiler door and clean−out cover,
opening,9
Boiler door and clean−out cover,
security12
Burner adjustment,17
C
Clean−out cover insertion,12
Clean−out cover opening,9
Commissioning/service report,28
Completion notice,3
Connections on water and steam
side, checking,16
D
Declaration of conformity,29
Diagnostics,18
H
Heating surface, cleaning,11
F
Flue outlet and flue pipe,
cleaning,11
Further details regarding the
individual steps,5
I
Inspection ports, checking for leaks
after filling the boiler,16
M
Manufacturer’s certificate,30
Multiple level electrode, cleaning,15
P
Parts list,21
Pressure regulator and pressure
limiter adjustment,6
Pressure regulator, pressure limiter
and thermostat (standby),
checking,17
S
Safety instructions,2
Safety valve, checking,17
Sight glass in boiler door,
cleaning,16
Specification,27
Steps,4
System shutdown,8
System start−up,7
T
Turbulator insertion,12
Turbulator removal and cleaning,10
V
Vitoair draught stabiliser, checking
(if installed),17
Vitoair draught stabiliser, closing
(if installed),9
W
Water chamber, checking for
deposits,14
Water level indicator, cleaning,15
Water quality requirements,26
5692729 GB