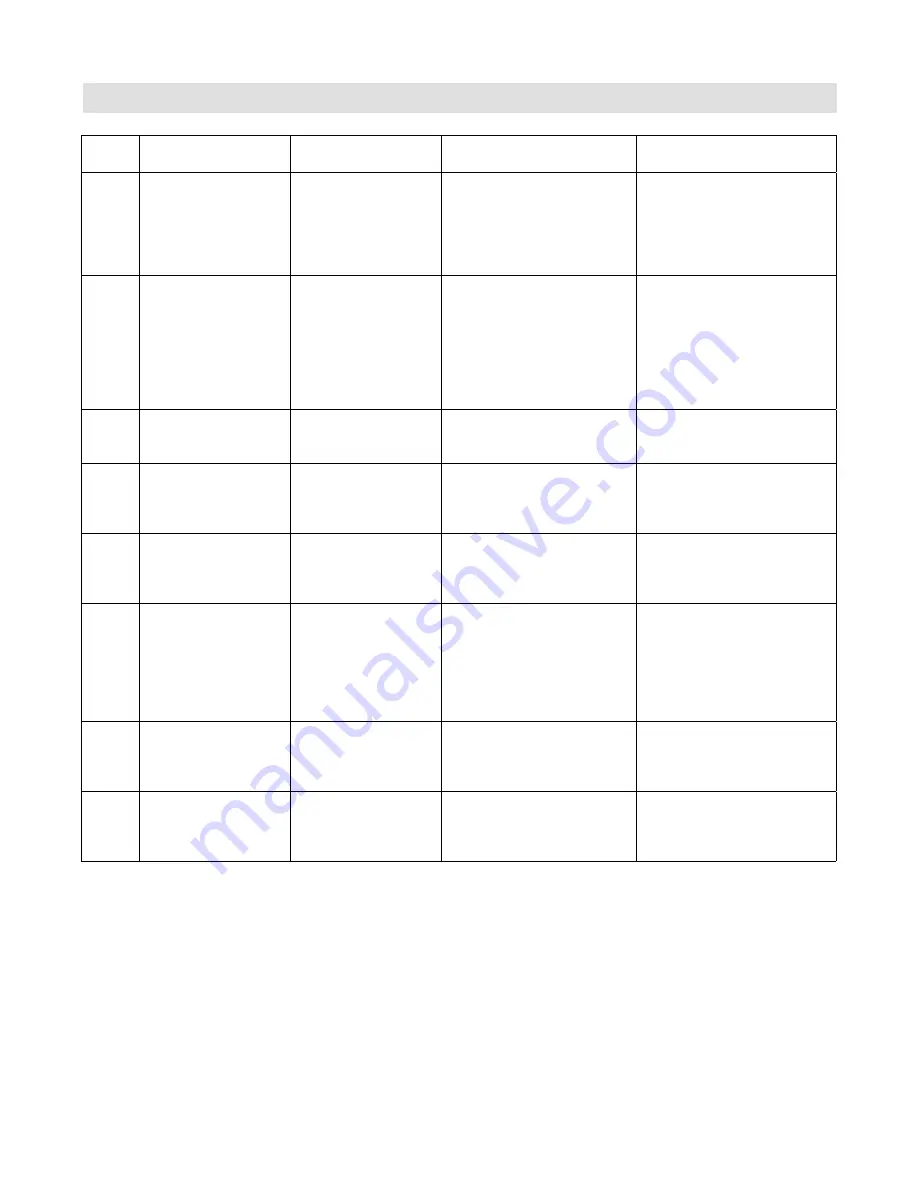
27
5603 880 - 01
Pyrot Service & Maintenance
Troubleshooting
Loader System Faults
Fault
No.
Text displayed
Indicator
Possible cause
Check / remedy
01
Material shortage
(red light at F4)
- Light barrier in the
metering container
- Light barriers for the
ember monitoring
system
- Silo is empty
- Conveyance system is
clogged/jammed
- Fill silo
- Turn off main switch and
remove material clogging
- Acknowledge with OK
11-24
Soft starter …
(red light at F4)
- Soft starter
- Red light at the soft
starter
- Phase sequence mixed up
- Motor overloaded
- Other causes, depending
on the malfunction displayed
- Correct the phase sequence
(clockwise rotating
magnetic field)
- Remove clogging
- Refer to documentation for
soft starter
- Acknowledge with OK
30
Feed auger
(red light at F4)
- Reversed control of
in-feed auger
- Material clogging in the
in-feed auger
- Remove material clogging
31-45
Conveyor device …
(red light at F4)
- Maintenance cover
limit switch
- One of the maintenance
covers is open or not
closed properly
- Check and close all the
maintenance covers
- Acknowledge with OK
51-52
Extraction system …
(red light at F4)
- Maintenance cover
limit switch
- One of the maintenance
covers is open or not
closed properly
- Check and close all the
maintenance covers
- Acknowledge with OK
53-54
Extraction system
… Hydraulic drive,
temperature/level
(red light at F4)
- Level float switch
in the oil container
for the walking floor
extraction system
- Thermostat in the
oil container
- Oil level too low, (possible
loss of oil)
- Oil has been overheated by
too high pressure
- Refill oil. Check oil line for
leakage
- Check and adjust operating
pressure
- Acknowledge with OK
53-54
Extraction system …
silo door open
(red light at F4)
- Limit switch for silo
door
- Silo door open
- Check and close silo door
- Acknowledge with OK
01-27
Interruption or short-
circuit, sensor …
(red light at F4)
- Sensor . . .
- Damaged sensor
connection line
- Indicator defective
- Call a qualified electrician