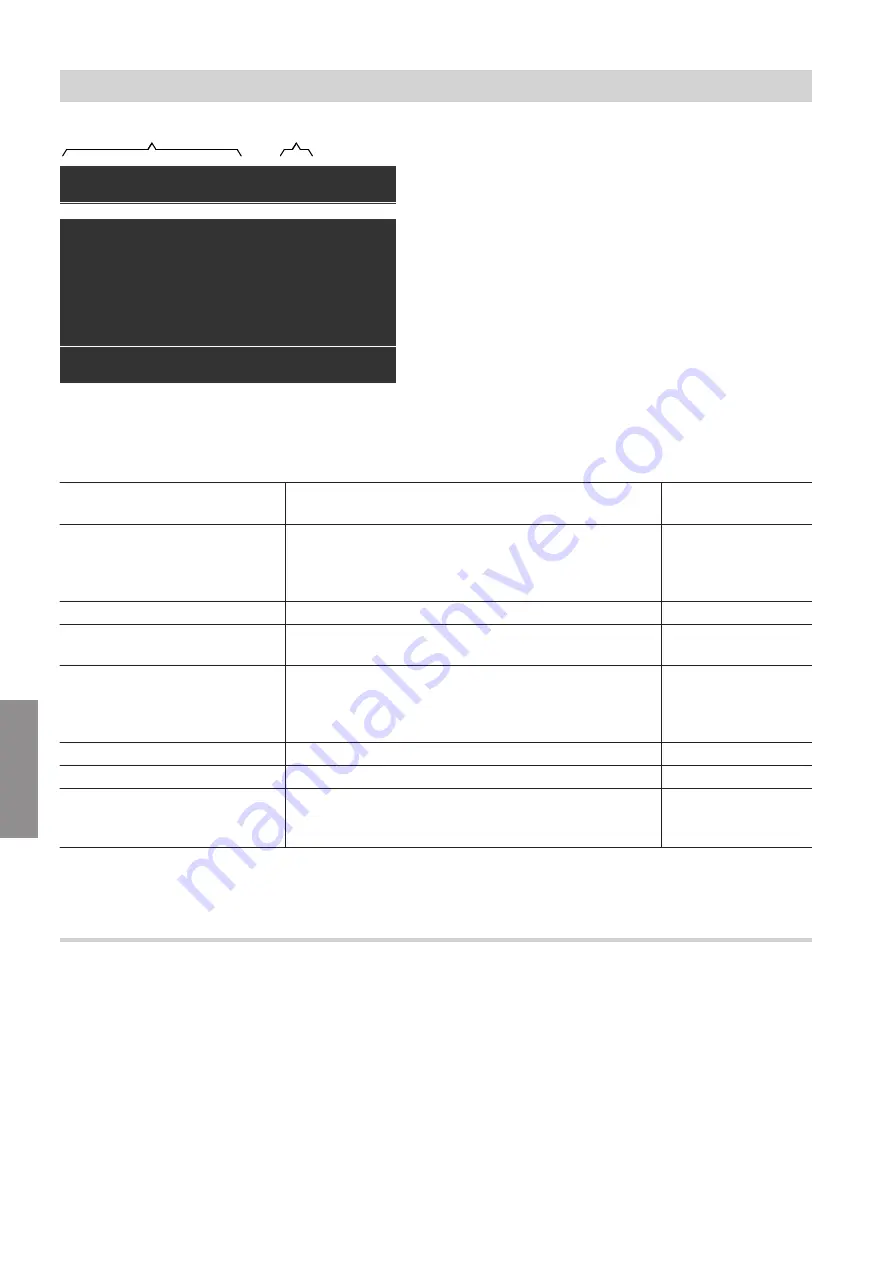
32
Timer
Select with
(
A
B
Ü
Min. runtime heat pump
Opt. runtime heat pump
106
6118
30
Start-up time heat pump
Heat pump blocking time
426
Fig. 10
A
Active events
B
Remaining time in s
Active events
Meaning
Factory-set time de-
faults
"Start-up time heat pump"
Advance runtime for primary pump and secondary
pump:
Of no significance, as primary pump and secondary
pump are not connected.
60 or 120 s
"Min. runtime heat pump"
Minimum runtime for increasing heat pump efficiency
120 or 180 s
"Opt. runtime heat pump"
Time during which the COP has an almost linear pat-
tern.
10 or 20 min
"Pump run-on time heat
pump"
Secondary pump run-on time, after which heating op-
eration with the heat pump ends:
Of no significance, as secondary pump is not connec-
ted.
—
"Heat pump blocking time"
Pause to reduce compressor wear
180 or 600 s
"Refrigerant circuit functions"
Max. time for suction gas pressure control
10 min
"HP protection functions"
Max. time, during which the minimum temperature dif-
ferential between condenser and evaporator does not
have to be reached.
10 min
Note
If no process is active, the display shows
"No timer
active"
.
Integral
Excessively frequent starting and stopping reduces the
service life of the compressor. For this reason, the
compressor only starts when the min. return tempera-
ture is consistently undershot. The heat pump control
unit takes into account the extent and duration of the
undershooting via the output integral.
The compressor only starts if the output integral has
exceeded the
"Start threshold 730E"
.
The
"Integral"
display indicates the current extent of
the output integral.
1. Service menu:
Press
OK
+
å
simultaneously and hold for
approx. 4 s.
2. "Diagnosis"
3. "System"
4. "Integral"
Diagnosis
System
(cont.)
5800 917 GB
Diagnosis