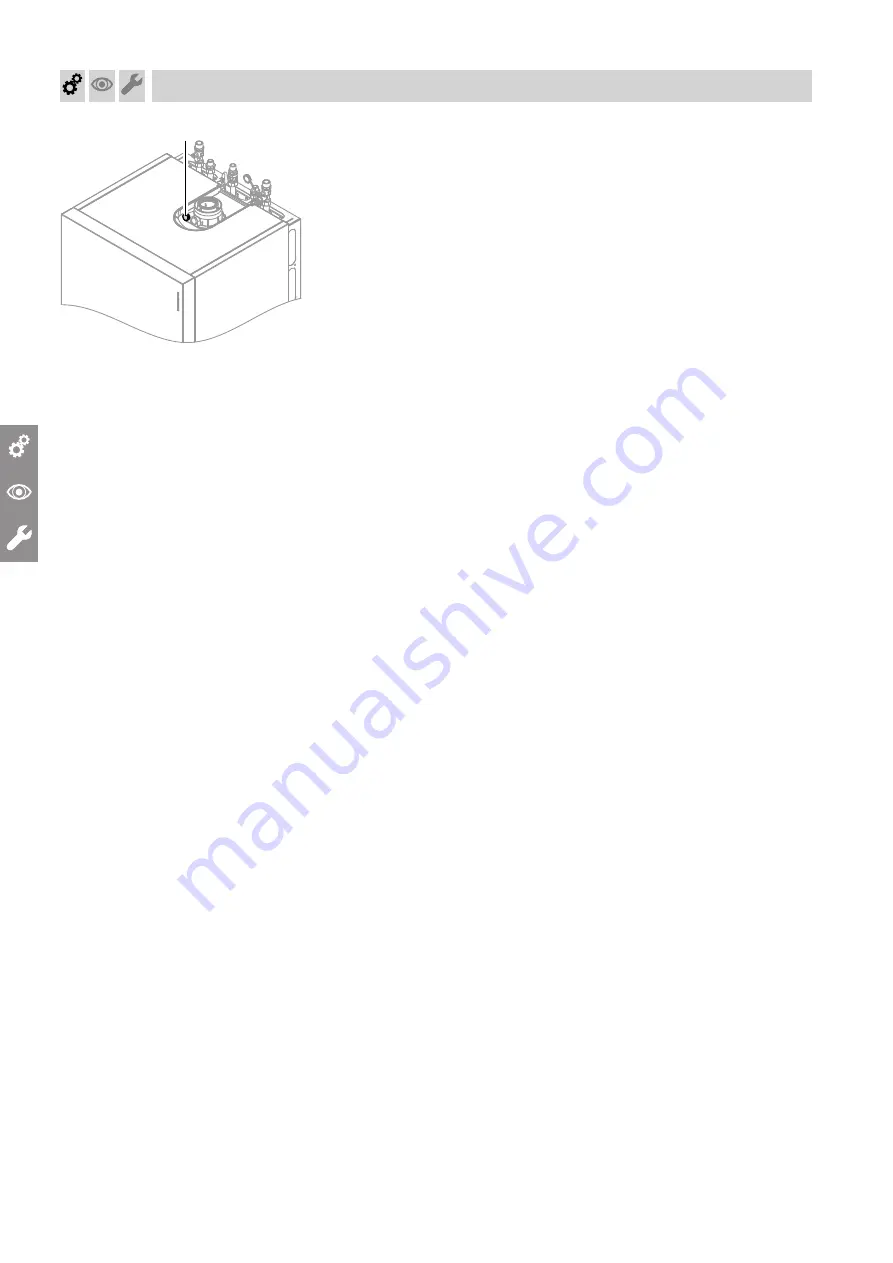
40
A
Fig. 28
A
Combustion air aperture (ventilation air)
For balanced flue systems tested together with the
heat source, there is no requirement for a tightness
test (overpressure test) during commissioning by the
flue gas inspector.
In this case, we recommend that your heating contrac-
tor carries out a simple tightness test during the com-
missioning of your system. For this it would be suffi-
cient to check the CO
2
or O
2
concentration in the com-
bustion air at the annular gap of the balanced flue
pipe.
If the CO
2
concentration is less than 0.2 % or the O
2
concentration is greater than 20.6 %, the flue pipe is
deemed to be sufficiently gas tight.
If actual CO
2
values are higher or actual O
2
values are
lower, a pressure test with a static pressure of 200 Pa
will need to be carried out on the flue pipe.
Commissioning, inspection, maintenance
Tightness test on balanced flue system (annular gap check)
5789 302 GB
Summary of Contents for B2TB
Page 6: ...6 15 Keyword index 152 Index Index cont 5789 302 GB ...
Page 117: ...117 Parts lists Hydraulics 5789 302 GB Components ...
Page 154: ...154 5789 302 GB ...
Page 155: ...155 5789 302 GB ...