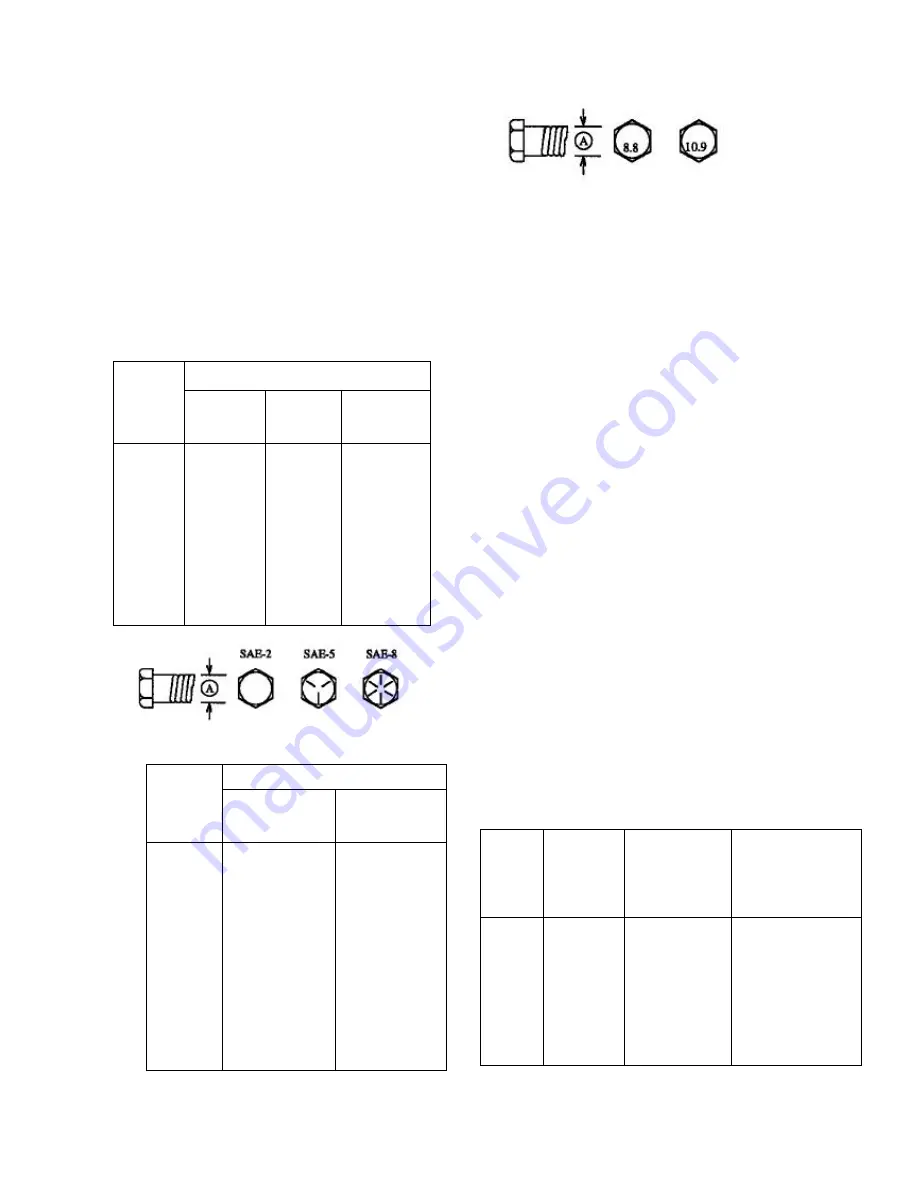
ENGLISH
TORQUE
SPECIFICATIONS
METRIC
TORQUE
SPECIFICATIONS
6.2
BOLT
TORQUE
CHECKING
BOLT
TORQUE
The
tables
shown
below
give
correct
torque
values
for
various
bolts
and
cap
screws.
Tighten
all
bolts
to
the
torques
specified
in
chart
unless
otherwise
noted.
Check
tightness
of
bolts
periodically,
using
bolt
torque
chart
as
a
guide.
Replace
hardware
with
the
same
strength
bolt.
Torque
figures
indicated
above
are
valid
for
non-greased
or
non-oiled
threads
and
heads
unless
otherwise
specified.
Therefore,
do
not
grease
or
oil
bolts
or
cap
screws
unless
otherwise
specified
in
this
manual.
When
using
locking
elements,
increase
torque
values
by
5%.
*
Torque
value
for
bolts
and
cap
screws
are
identified
by
their
head
markings.
6.3
HYDRAULIC
FITTING
TORQUE
Tightening
Flare
Type
Tube
Fittings
*
1.
Check
flare
and
flare
seat
for
defects
that
might
cause
leakage.
2.
Align
tube
with
fitting
before
tightening.
3.
Lubricate
connection
and
hand
tighten
swivel
nut
until
snug.
4.
To
prevent
twisting
the
tube(s),
use
two
wrenches.
Place
one
wrench
on
the
connector
body
and
with
the
second
tightens
the
swivel
nut
to
the
torque
shown.
5.
The
torque
values
shown
are
based
on
lubricated
connections
as
in
rears.
Bolt
Diameter
"A"
Bolt
Torque*
8.8
(N.m)
(lb-ft)
10.9
(N.m)
(lb-ft)
M3
M4
M5
M6
M8
M10
M12
M14
M16
M20
M24
M30
M36
.5
.4
3
2.2
6
4
10
7
25
18
50
37
90
66
140
103
225
166
435
321
750
553
1495
1103
2600
1917
1.8
1.3
4.5
3.3
9
7
15
11
35
26
70
52
125
92
200
148
310
229
610
450
1050
774
2100
1550
3675
2710
Tube
Size
OD
(in.)
Nut
Size
Across
Flats
(in.)
Torque
Value
(N.m)(lb-ft)
Recommended
Turns
To
Tighten
(After
Finger
Tightening)
(Flats)
(Turn)
3/16
1/4
5/16
3/
1/2
5/8
3/4
7/8
7/16
9/16
5/8
/
6
7/8
1
1-1/4
1-3/8
8
6
12
9
16
12
24
46
34
62
46
102
75
122
90
1
1/6
1
1/6
1
1/6
/6
1
1/6
1
1/6
3/4
1/8
3/4
1/8
Bolt
Diameter
"A"
Bolt
Torque*
SAE
2
(N.m)
(lb-ft)
SAE
(N.m)
(lb-ft)
SAE
(N.m)
(lb-ft)
1/4"
5/16"
3/8"
7/16"
1/2"
9/16"
5/8"
3/4"
7/8"
1"
8
6
13
10
27
20
41
30
61
45
95
60
128
95
225
165
230
170
345
225
12
9
25
19
45
33
72
53
110
80
155
115
215
160
390
290
570
420
850
630
17
12
36
27
63
45
100
75
155
115
220
165
305
220
540
400
880
650
1320
970
Summary of Contents for BXH-5x10
Page 1: ...Victory Tractor Implements WOOD CHIPPER USER MANUAL Owner s Manual BXH 5x10 BXH 7x12...
Page 26: ......
Page 27: ......
Page 28: ......
Page 29: ......