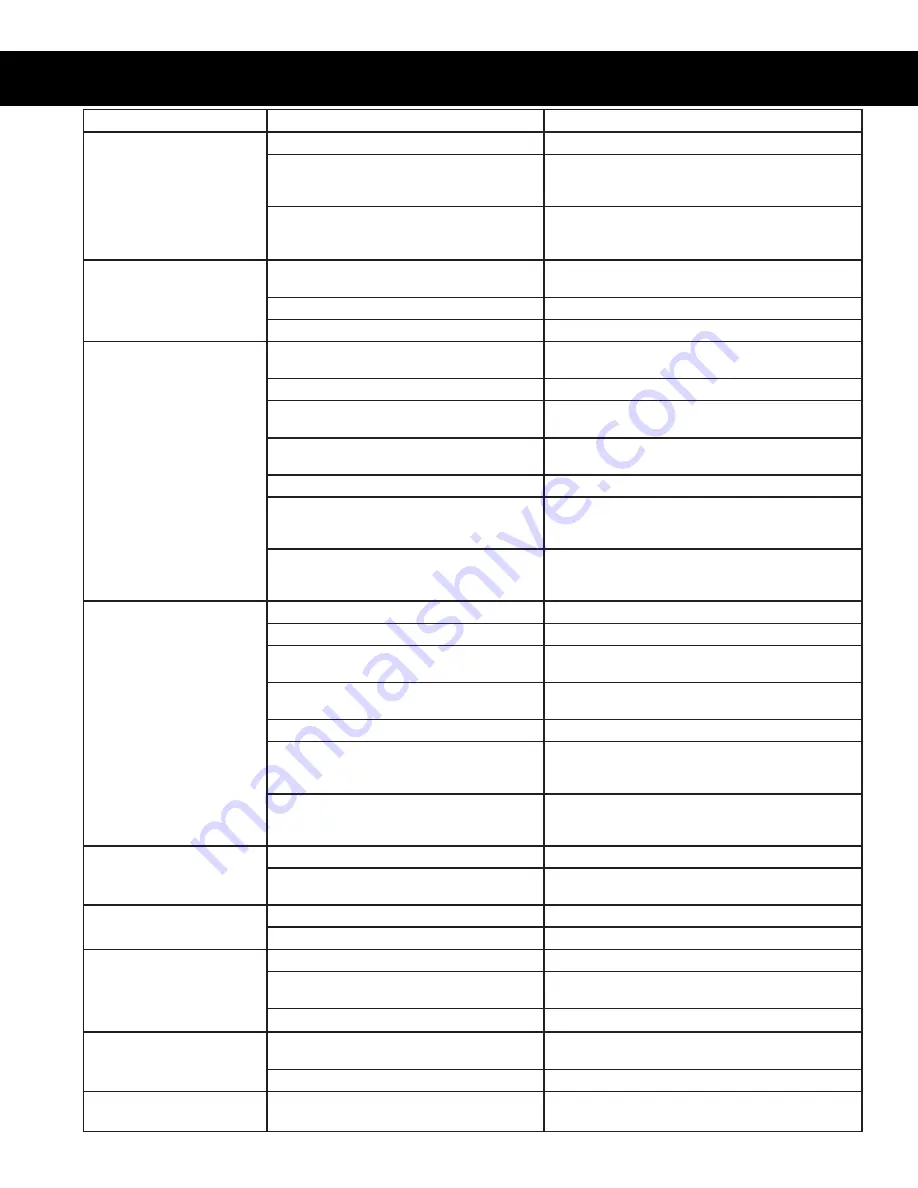
10
PROBLEM
POSSIBLE CAUSE
REMEDY
Controller Display does
not illuminate
Fuse blown or circuit breaker tripped
Replace fuse or reset circuit breaker
Power cord unplugged
Plug in power cord to designated receptacle.
Cabinet cannot share same outlet with other
equipment.
Control or main power switch turned off
Turn on control or main power switch (refer
to page 3 "
V-TEMP
™
Keypad Buttons &
Functions" section)
Cabinet not running
Improper voltage supplied to cabinet
(voltage does not match Data-Plate)
Correct supply voltage (remove extension cords
or other equipment on circuit, etc).
Controller set too high
Set controller to lower temperature
Cabinet in defrost cycle
Allow defrost cycle to fi nish
Condensing Unit on
Refrigerator or Freezer
runs for prolonged
period or continuously
Excessive amount of warm product loaded
in cabinet
Allow adequate time for product to cool down
No product in cabinet
Load cabinet with product
Prolonged door opening or door ajar
Make sure door is closed when not in use. Avoid
prolonged door openings.
Door gasket not sealing properly
Check door gasket condition. Adjust door or
replace gasket.
Dirty condenser coil
Clean the condenser coil
Improper air fl ow around condensing unit
Insure adequate air space, relocate away from
heat generating equipment, direct sunlight, or
direct path of air conditioning or heating ducts
Evaporator coil blocked with ice
Turn unit off and allow coil to defrost. Make sure
controller temperature is not set too low and that
door gasket is sealing properly.
Refrigerator or Freezer
cabinet temperature too
high
Controller set too high
Set controller to lower temperature
Poor air circulation in cabinet
Re-arrange product to allow proper air circulation
Excessive amount of warm product loaded
in cabinet
Allow adequate time for product to cool down
Prolonged door opening or door ajar
Make sure door is closed when not in use. Avoid
prolonged door openings.
Dirty condenser coil
Clean the condenser coil
Insuffi cient clearance around cabinet or
excessively high ambient temperature
Insure adequate air space, relocate away from
heat generating equipment (ovens, fryers, heating
ducts, etc.), and out of direct sunlight
Evaporator coil blocked with ice
Turn unit off and allow coil to defrost. Make sure
controller is not set too cold and that door gasket
is sealing properly.
Cabinet is noisy
Part(s) loose
Locate and tighten loose part(s)
Tubing vibrating
Insure tubing is free from contact with other
tubing or components
Refrigerator is freezing
product
Controller set too low
Set controller to higher temperature
Cabinet overloaded with product
Remove or re-arrange product
Refrigerator or Freezer
compressor will not
start - hums and trips
on overload protector
Dirty condenser coil
Clean the condenser coil
Excessive heat generated from nearby
equipment
Relocate cabinet or adjust heat generating
equipment
Voltage to cabinet too high or too low
Check and correct supply voltage
Door won't close tight
Cabinet is not level
Level cabinet by adjusting legs or shimming
casters
Hinge(s) may need slight adjusting.
Apply shim(s) to hinge until door seals properly.
Controller Alarm &
Error Codes
----
Refer to page 5 of manual. If problem(s) persist,
contact the factory for further assistance.
TROUBLESHOOTING GUIDE FOR COMMON PROBLEMS
TROUBLESHOOTING GUIDE FOR COMMON PROBLEMS
Caution:
Caution: Disconnect Power Supply Prior To Attempting Any Service!
Disconnect Power Supply Prior To Attempting Any Service!