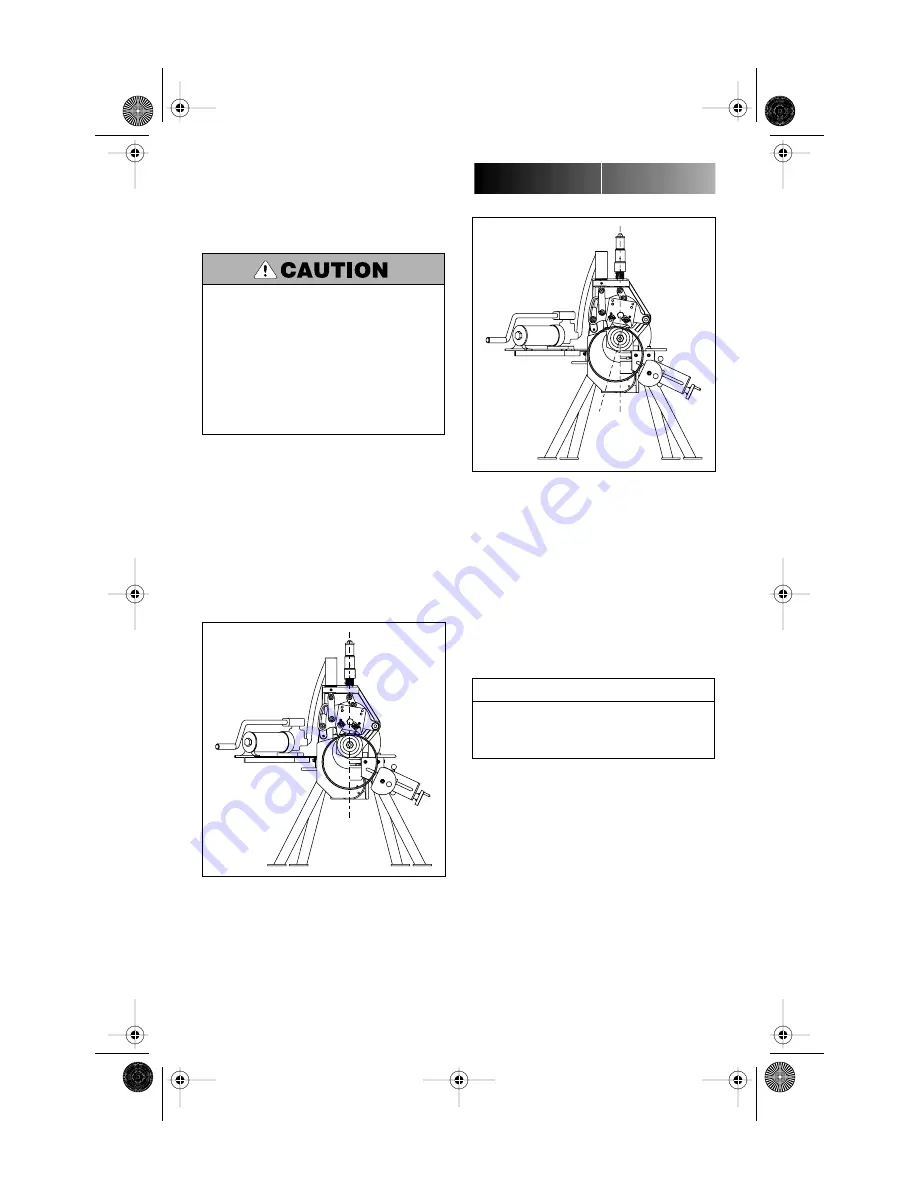
12
6.
Advance stabilizer roller inward with hand-
wheel to the position indicated in Figure 3
below, then tighten locking handle.
7.
Complete the
Pre-Operation Adjust-
ments
and groove the pipe (see Grooving
Operation pages 14 - 16.) Observe the stabilizer
roller while grooving. It should remain in con-
tact with the pipe most of the time and the
pipe should rotate smoothly without swaying
from side to side. If not, advance stabilizer
roller further inward. Retest and make further
adjustments as necessary. Remember, do not
adjust stabilizer too far inward as it will skew
the pipe to the left and possibly result in exces-
sive pipe end flaring.
“CORRECT”
Figure 3
Do not adjust stabilizer to push pipe to the left and off
center from the rolls (see Figure 4 at right). Doing so
will cause increased pipe end flare and shorten roller
life.
• Assembly of couplings on pipe exceeding Maximum
Allowable Flare, Column 8 in the Roll Groove
Specifications charts, pages 29 - 32, may prevent
closure of couplings pad-to-pad, allowing possible
pipe separation and result in property damage.
• Also, joint leakage may result due to excessive
gasket distortion/damage.
VE270FSD
“INCORRECT”
Figure 4
GROOVE DIAMETER STOP
ADJUSTMENT
The groove diameter stop must be adjusted for
each pipe size or change in wall thickness.
Groove diameter, identified as the “C” dimen-
sion for each pipe size, is listed under Roll
Groove Specifications, pages 29 - 32. For your
convenience, a “C” Diameter Chart for Steel
Pipe is also on the tool.
To achieve proper diameter:
1.
Determine the diameter and thickness of
the pipe to be grooved. (See the Dimensions
Charts on page 33.)
2.
Locate the proper diameter and thickness
on the pipe size indicator on the depth stop. It
is rotatable for easy viewing.
NOTICE
To perform the following adjustments, use several
short scrap sections of pipe (but not shorter than what
is recommended in Table 1, page 8) of the proper
material, diameter and thickness to be grooved.
TM-VE270FSD.2469 Rev.B Page 12 Sunday, October 28, 2001 4:10 PM