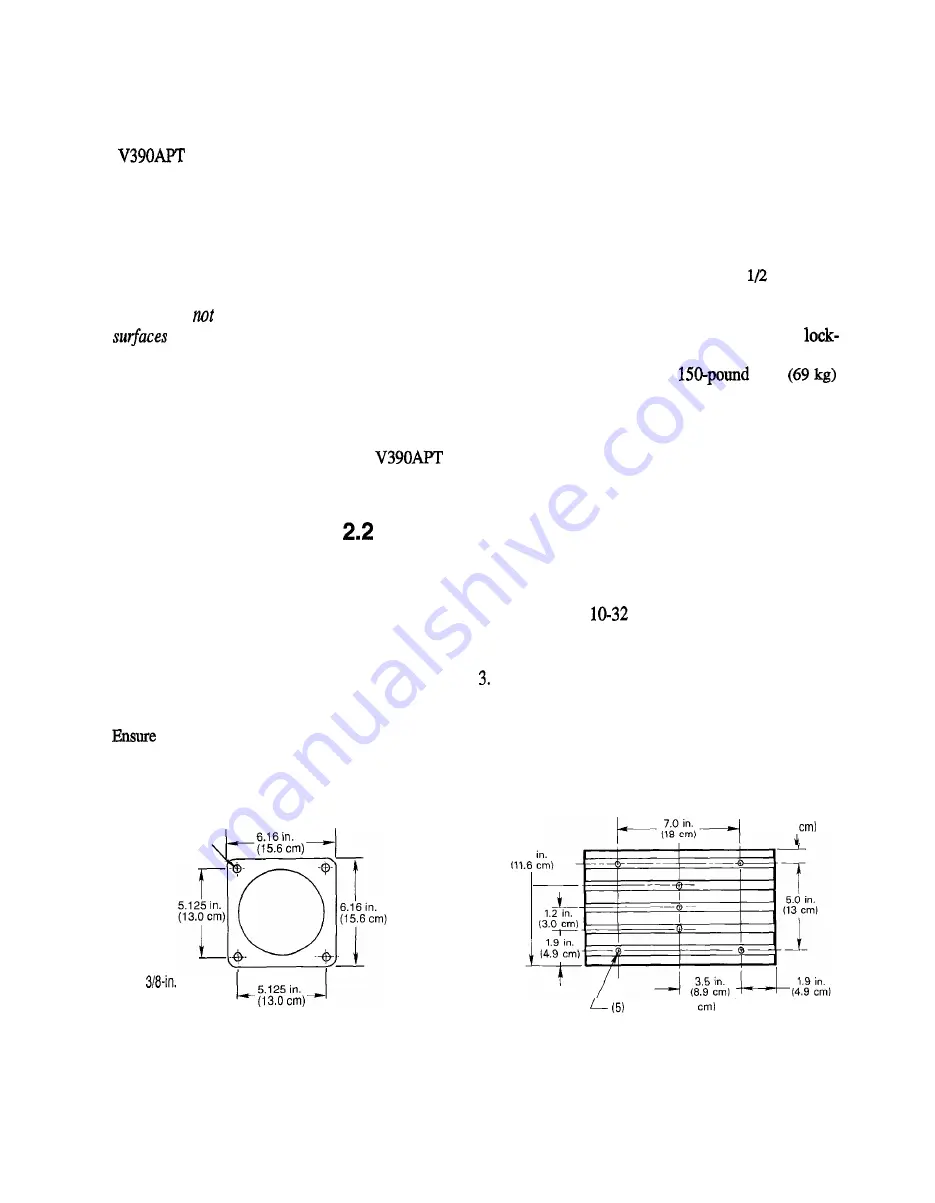
2. INSTALLATION
2.1 Mounting the Unit
The
will operate safely with loads up to 80
pounds (36 kg) mounted upright and 75 pounds (34 kg)
when inverted. To perform properly, the unit must be
securely fastened to a suitable surface and the camera
or housing must be properly mounted and balanced on
the unit. Normal mounting position for the unit is with
its axis vertical, either upright or inverted.
CAUTION: Do
attach these units to drywall
A
and do not install screws into the end
grain of wood.
The pan-and-tilt has been assembled at the factory for
upright mounting and should be mounted directly to a
surface capable of supporting the combined weight of
the pan-and-tilt and its accessories. The
weighs 40 pounds (18 kg).
N O T E : If the unit is to be mounted in the inverted
position, prepare the unit according to the instruc-
tions in section 2.2, Inverted Mounting.
When mounting directly to a horizontal or ceiling sur-
face, use four fasteners. When mounting to wood, use
screws long enough to penetrate at least 2
inches (6.4
cm). If mounting to a steel structure, drill four holes
according to the mounting pattern shown in Figure 2.
Screws should be long enough to accommodate
washers and nuts. In concrete, use lead anchors or
expansion bolts with at least
pullout strength, installed according to manufacturer’s
instructions,
CAUTION: If installing the unit outdoors, use
A
stainless steel hardware.
Inverted Mounting
CAUTION:
To reduce the risk of fire or electric
A
shock, always mount the pan-and-tilt in the up-
right position where rain or moisture is present.
2 .
The pan-and-tilt has been assembled for upright mount-
ing. When it is necessary to mount the unit in the
inverted position, it should be prepared as follows:
1.
that the tilt drive is in the center position so
that the camera mounting plate (Figure 3, Legend 4)
is level.
0.406
in. (1.03 cm)
diameter holes
Use
(10 mm)
hardware
PAN AND TILT MOUNTING BASE
Figure 2
Mounting Hole Dimensions
The front of the drive unit is identified by a decal
(see Figure 3). Facing the front of the unit, remove
the three (3)
screws (Legend 1) on the right
of the camera mounting plate.
Carefully pull the end support (Legend 2) away
from the main housing, maintaining the opposite tilt
arm in position.
4.6
0.75
in.
11.9
0.28 in. (0.07
Dia. Holes
CAMERA AND HOUSING MOUNTING PLATE
X433-893