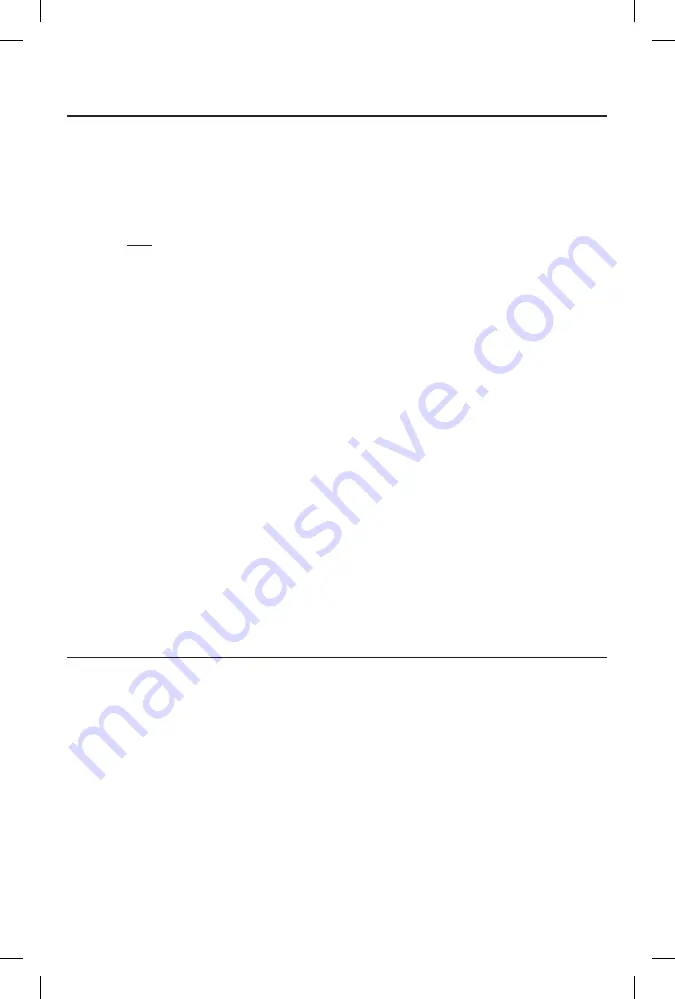
TLC DUAL 444C OBA 1.5 GAL / 200 PSI
USER MANUAL
AIR TANK & PLUMBING
(CONT'D)
MOUNTING THE TANK:
We have included 6 pieces of rubber bushings in your tank mounting hardware. You have the option
of using two layers of rubber bushings on one of your tank legs to slightly tilt tank toward the drain
cock port to improve drainage properties. Use the provided longer bolts, and corresponding washers,
lock washers and nuts to mount the tank to a suitable chassis or other place on your vehicle.
IMPORTANT:
- Tank is rated for 200 PSI maximum working pressure.
- Tank is NOT to be used as a breathing device.
- Use only attachments or tools rated for 200 PSI working pressure or less.
CAUTION! DO NOT PRESSURIZE YOUR TANK UNTIL YOU HAVE INSTALLED
ALL NECESSARY PORT FITTINGS AND ACCESSORIES.
- Apply sealant to threads of fittings prior to assembly and tighten each part with a wrench.
- Do not over tighten if your port fittings are made from brass, since brass threads can be stripped.
- Bleed pressure from tank before servicing or adding attachments.
WARNING: FAILURE TO DRAIN TANK AND REMOVE CONDENSATION
WILL CAUSE TANK TO RUST PREMATURELY.
- To remove accumulated condensation inside the tank, bleed pressure from tank using the drain
cock until pressure is approximately 5-20 PSI.
- Drain tank by opening the drain cock drain valve and close after draining tank.
- If drain cock valve is plugged, release all air pressure from tank, remove drain valve and clean,
then reinstall.
IMPORTANT
: Please observe air tank's Date of Manufacture (stamped on tank leg).
Replace air tank 2 to 5 years from date air tank was first used, or use the date of manufacture as
reference. Adhering to air tank draining guidelines will prolong the life of your air tank.
PLEASE NOTE: RUSTED TANKS CAN FAIL CAUSING EXPLOSIONS OR FATAL INJURIES.
Discard tank immediately if tank is rusted.
SAFETY VALVE:
When using a safety pressure relief valve, point the safety pressure relief valve away
from your body when releasing air. Use the pull ring on the safety relief valve to vent pressure from
the tank before servicing.
DUAL AIR COMPRESSOR INSTALLATION
Please follow these installation instructions to enjoy the best use of your onboard air system.
CAUTION - To reduce risk of electrical shock or electrocution:
- Do not disassemble the compressor. Do not attempt repairs or modifications.
Refer to qualified service agencies for all service and repairs.
- Do not use this product in an area where it can fall or be pulled into water or liquids.
- Do not reach for this product if it has fallen into liquid.
- Use this compressor with 12-Volt DC systems only.
- This product should never be left unattended during use.
Summary of Contents for 50044
Page 1: ......
Page 3: ...REDUCER REDUCER 5 0 0 35 15 10 1 20 25 30 2 REDUCER REDUCER REDUCER REDUCER ...
Page 4: ......
Page 10: ......