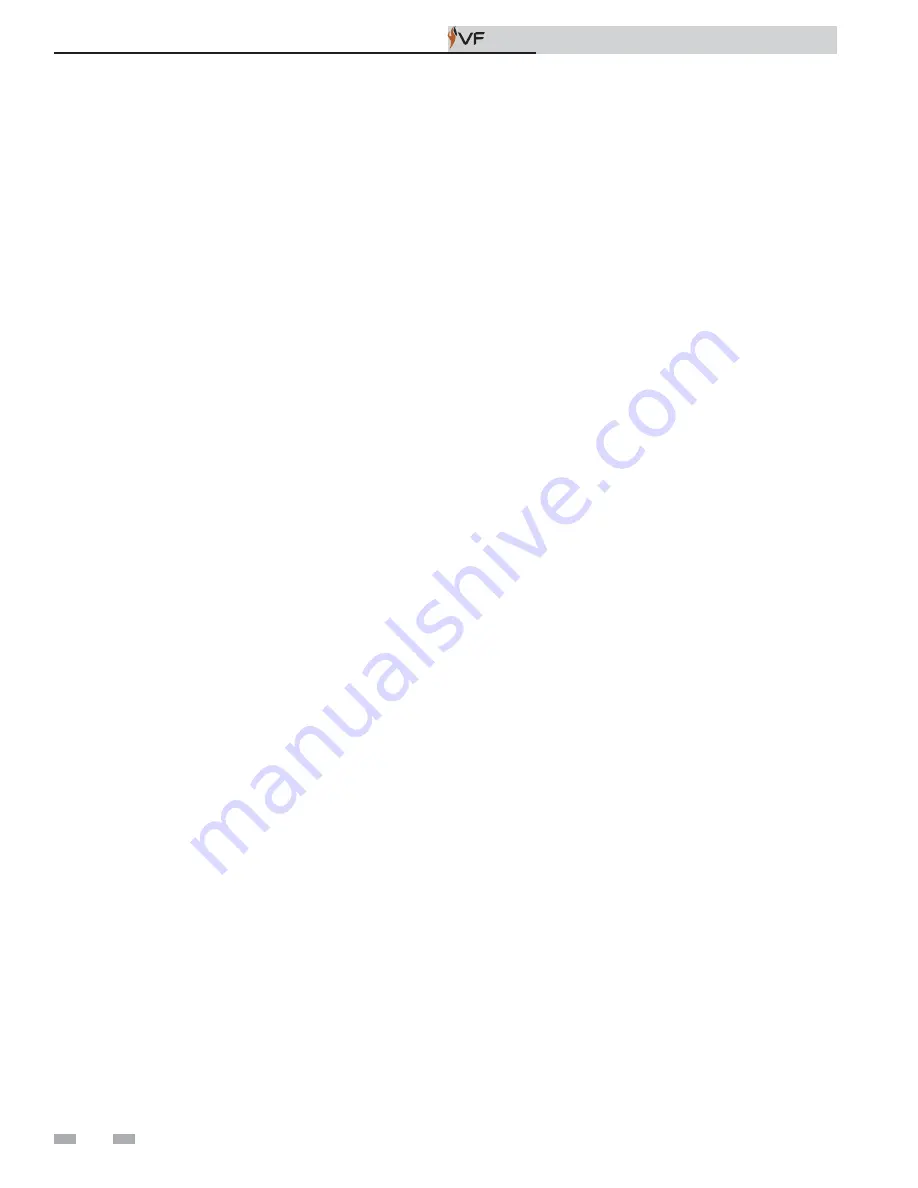
The VF Series - How it works...
1. Heat
exchanger
The heat exchanger allows system water to flow through specially
designed tubes for maximum heat transfer. The glass lined
headers and copper finned tubing are encased in a jacket that
contains the combustion process.
2.
Heat exchanger access cover
The heat exchanger access cover is a stainless steel door which
allows access for service, maintenance, and removal of the heat
exchanger from inside the combustion chamber.
3. Blower
The blower pulls in air and gas through the venturi (see item 5)
and injects the fuel/air mixture into the burner, where they burn
inside the combustion chamber.
4. Gas
valve
The gas valve allows the proper amount of gas to pass into the
burner for combustion. The gas valve on the
VF Series
works
under a negative pressure so gas should only be pulled through the
valve when the blower is in operation.
5. Venturi
The venturi attaches to the inlet (or suction) side of the blower
and generates the negative pressure needed by the gas valve.
6.
Flue sensor (not shown)
The flue sensor is mounted in the exhaust collar of the unit and
monitors the flue gas temperature. If the temperature in the stack
exceeds the maximum temperature the unit will shut down to
prevent a hazardous condition.
7. Outlet
temperature
sensor
This sensor monitors the outlet water temperature. If selected
as the controlling sensor, the appliance will maintain set point by
adjusting the firing rate of the unit according to this sensor.
8. Inlet
temperature
sensor
This sensor monitors inlet water temperature. If selected as the
controlling sensor, the appliance will maintain set point by
adjusting the firing rate of the unit according to this sensor.
9. Electronic
display
The electronic display consists of 7 buttons and a dual line
32-character liquid crystal display used to monitor the operation
of the heater as well as enter and view the programming of the
main control board.
10. Burner
(not
shown)
The burner is made of a woven fabric over steel screen construction.
The burner uses pre-mixed air and gas and provides a wide range
of firing rates.
11. Water outlet (system supply)
The water outlet is a 2 1/2" pipe connection that supplies water to
the system with connections for a flow switch (see #28) and a relief
valve (see #25).
12. Water inlet (system return)
The water inlet is a 2 1/2" pipe connection that receives water from
the system and delivers it to the heat exchanger.
13. Gas
connection
pipe
The gas pipe connection on this appliance is 1", 1 1/4", or 1 1/2"
NPT. To deliver the correct amount of gas volume to the appliance
it may be necessary to have a larger gas line reduced to 1 1/4" at the
appliance. Please reference the National Fuel Gas Code charts for
more
details.
14. Control
module
The control module is the main control for the appliance. This
module contains the programming that operates the blower, gas
valve, and pumps in addition to other programmable features.
15. Air
intake
The air intake pipe allows fresh air to flow directly to the
appliance. The air inlet is part of the filter box assembly where air
filtration is accomplished with a standard filter.
16. Line voltage terminal strip
The line voltage terminal strip provides a location to connect all of
the line voltage (120 VAC) contact points to the unit.
17. Low
voltage
connection
board
The low voltage connection board provides a location to tie in
all of the low voltage contacts to the appliance. This is where most
of the external safety devices are connected to the unit such as the
louver proving switch.
18. Condensate
trap
The condensate trap is designed to prevent flue gases from
escaping the appliance through the combustion chamber drain.
19. Access cover - front
The front access cover provides access to the gas train as well as the
blower and other key components for service and maintenance.
20. Hot surface igniter (HSI)
The hot surface igniter is a device that is used to ignite the air/
gas mixture as well as monitor the performance of the flame
during operation. This device acts as a flame sense electrode.
21. Flame inspection window (sight glass)
(not shown on Models 500 - 1000)
The flame inspection window is a quartz glass window that
allows a visual inspection of the burner and flame during
operation.
22. Gas shut off valve (downstream test cock)
The downstream test cock is provided in the gas train to ensure
complete shut off of the gas to the burner in case of
maintenance, inspection, or testing of the valve.
23. Manual reset high limit sensor
Device that monitors the outlet water temperature to ensure
safe operation. If the temperature exceeds its setting (field
adjustable), it will break the control circuit, shutting the
appliance
down.
24. Relief
valve
The relief valve is a safety device that ensures the maximum
pressure of the appliance is not exceeded. Water heaters operate
on temperature and pressure and are shipped standard as 125 PSI
and 210°F (98.9°C).
25. Power
switch
The power switch is used to engage and disengage power to the
appliance on the 120 VAC circuit.
26. Air
pressure
switch
The air pressure switch is a safety device which ensures proper
blower operation. The air pressure switch is wired in series with
the low voltage control circuit in such a way that if the fan does not
engage or shuts down prematurely the device will break the
control circuit and the unit will shut down.
27. Flow
switch
The flow switch is a safety device that ensures flow through the
heat exchanger during operation. This appliance is low mass and
should never be operated without flow. The flow switch makes
contact when flow is detected and allows the unit to operate. If
flow is discontinued during operation for any reason the flow
switch will break the control circuit and the unit will shut down.
6
Installation & Operation Manual