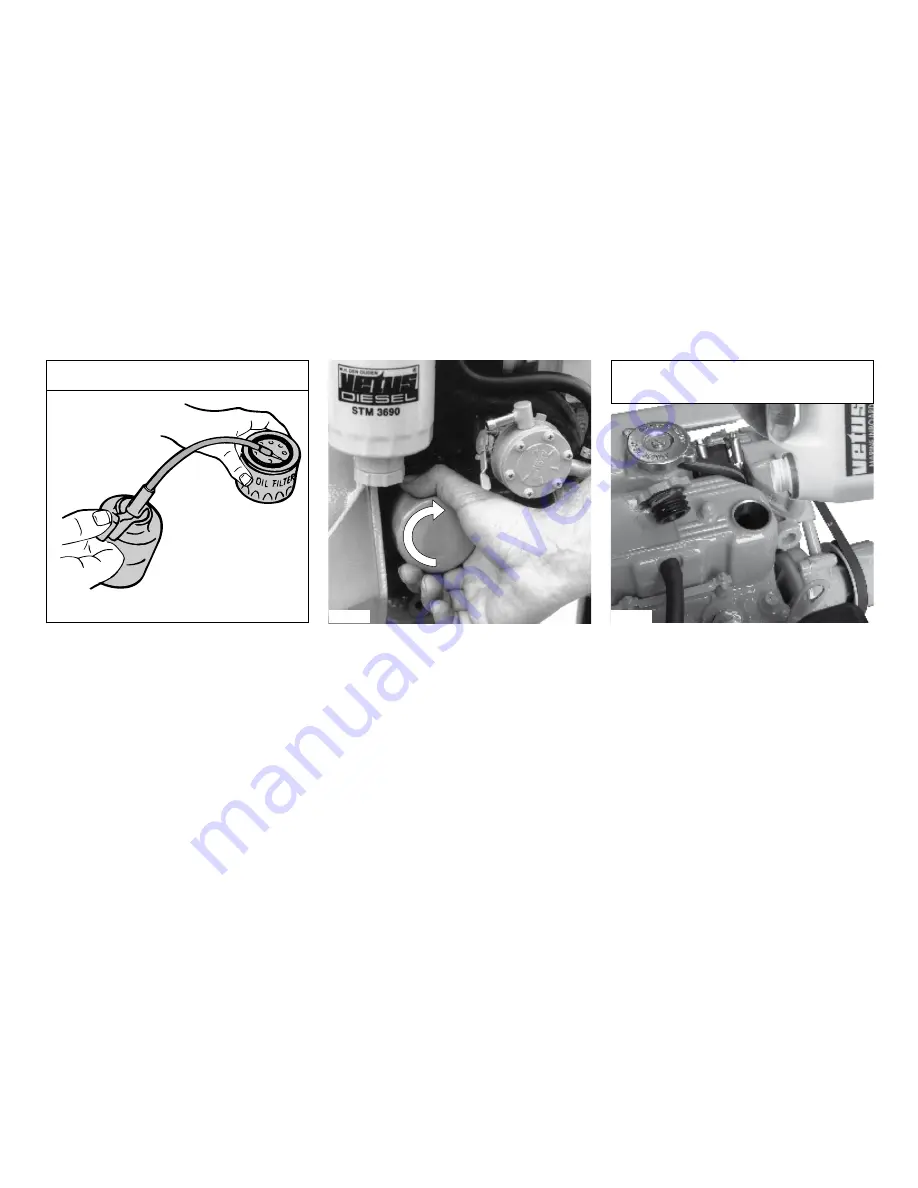
VD01120
29
15 Oiling the oil seal
Clean the contact surface of the gasket.
Lubricate the oil seal of the new filter ele-
ment with clean engine oil.
16 Oil filter installation
Install the filter in accordance with the
instructions printed on the filter element
housing.
17 Refilling with oil
Refill the engine with new oil (for specifica-
tion see page 65) through the filler open-
ing in the valve cover.
Operate the engine at idling speed for a
short period of time. Check for oil leaks
whilst the engine is running.
Stop the engine. Allow 5 minutes for the oil
to return to the sump. Check the oil level
with the dipstick.
Engine oil change
Every 100 operating hours.
4 Maintenance
VD00124
VD01011
o
il
filter
,
art
.
Code
: StM0051
a
Mount
of
oil
:
4.1 litres
(
oil
filter
inCl
.)
(7.2 UK pt, 8.7 US pt)
Summary of Contents for M3.28 SOLAS
Page 1: ...Operation manual M3 28 ...
Page 2: ...ii ...