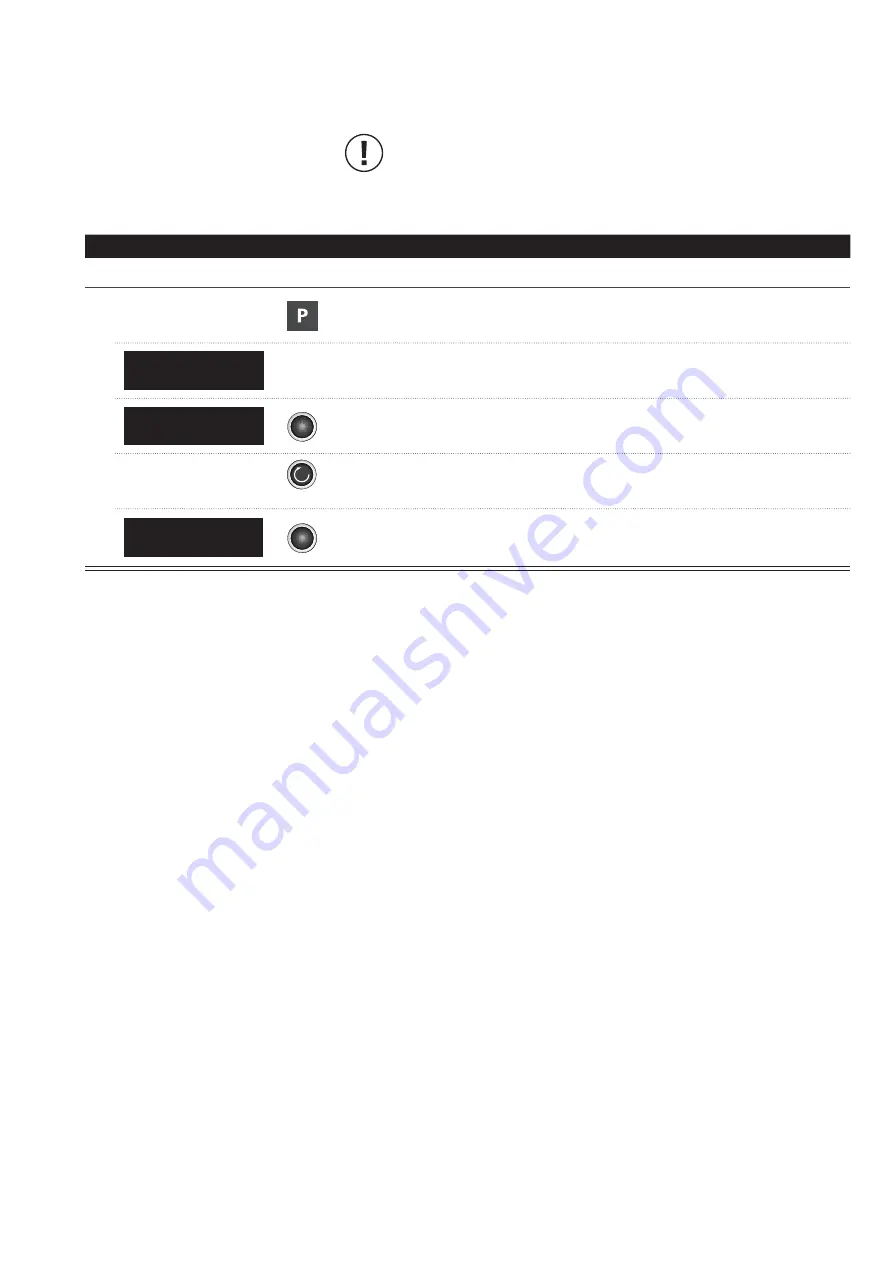
39
02/2021
Vetron 5374 HotAir-Welding
DISPLAY
STEP
DESCRITPTION
»
MACHINE PARAMETER
1
»
Press the “
PARAMETER
“ button
The corresponding LED on the display lights up.
2
G
N M
A E
R M
A
P 0
R
1
00
S
T
T
E
Turn the
JOG KEY COUNTERCLOCKWISE
, until
you can find the
BASIC PARAMETERS
B
p
n
s
a
r
t
c
h
m
r
a
M
a
e
i
c
a
e
i
e
»
Confirm.
»
Turn the
JOG KEY
clockwise, in order to
find the parameter list
3
a
f n .
u c
k y
e
R t
o
1
M40
E
T
P.
M
»
Confirm.
The first machine parameter is shown.
The M in M401 indicates that this parameter is
a machine parameter.
ADVICE!
You can find all calibrations applicable to the machine, including
resetting the operating program and the states of the digital and
analog inputs and outputs under the machine paramters.
Navigate to the machine parameters as follows:
06. PROGRAM- & MACHINE PARAMETER
01.
PROGRAM- & MACHINE PARAMETER SETTING