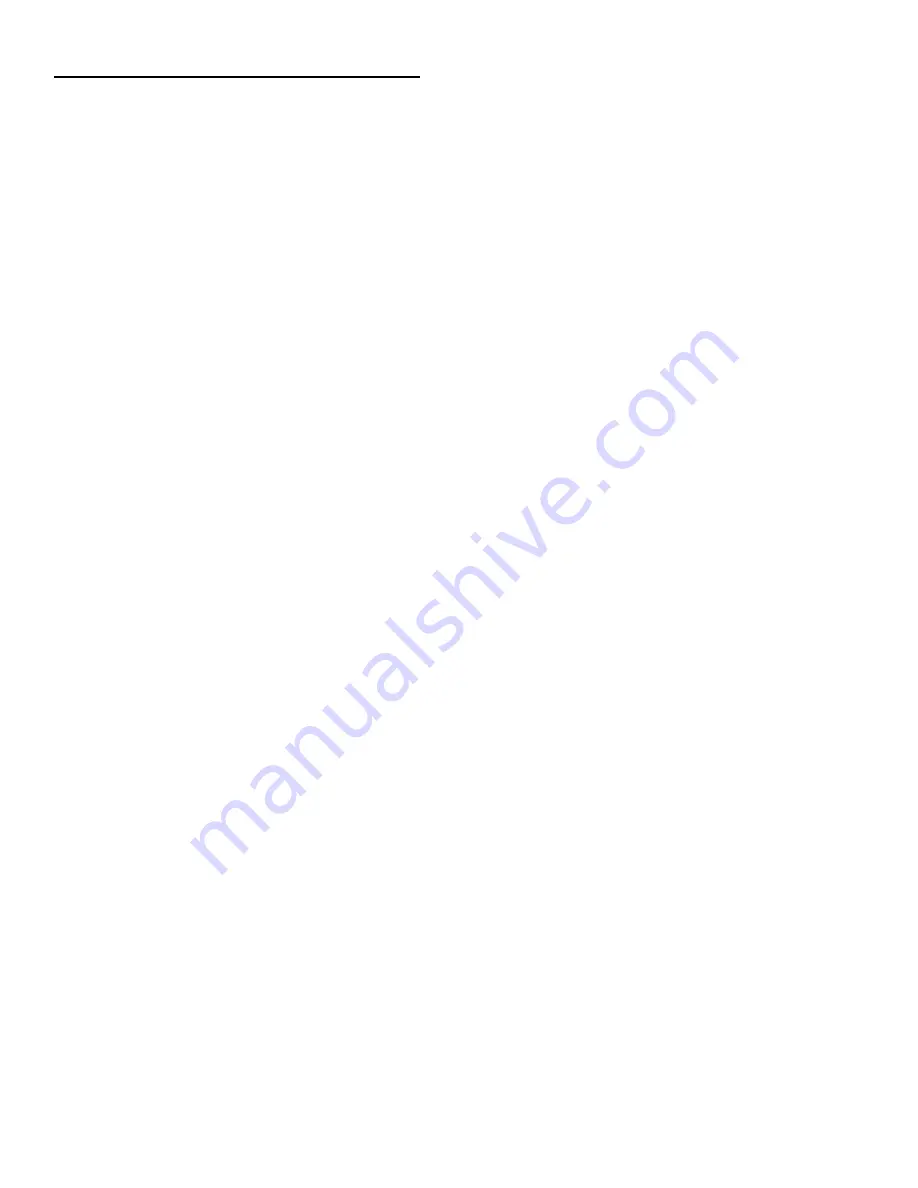
6/25/2015
Manual, WL-100.doc
T
HE POWER UNIT
’
S OPERATION
–
WL-100
The electric / hydraulic scissor dock utilizes an electric motor directly coupled to a gear-type hydraulic pump to
produce the needed fluid pressure and flow to allow the cylinders to perform the work of lifting the platform load.
A hydraulic manifold houses the hydraulic control components, and is bolted onto the top of the reservoir.
The power unit’s hydraulic components are all rated for 3,000 psi working pressure.
o
Important parts of the power unit include:
•
The electric motor. Motors are available for operation on single- or three-phase AC supplies. All are dual-voltage.
(Single-phase is not recommended because of the large current draw and slower speed.)
•
The gear pump. Its shaft is coupled directly to the shaft of the electric motor. Due to restrictions on the size of
the power supply circuit, the single-phase units have a smaller gear pump.
•
The check valve. Its purpose is to prevent the backflow of fluid through the pump. In this way, it allows the
platform to be held at a given elevation indefinitely.
•
The pressure relief valve. Its job is to open a path for fluid to flow back to the reservoir in the event that the fluid
pressure built up by the pump exceeds 3,000 psi. Thus the pump cannot generate more than 3,000 psi.
•
The lowering solenoid valve. This is an electrically-operated cartridge valve with a manual operator. It contains a
screen to keep contaminants from entering the valve. It also has a knurled knob to open the valve manually to
lower the platform in the event of a power outage, damage to toe guards, etc. Push down, turn the knob CCW,
and release it to open the lowering valve. Push down and turn CW to close it.
•
The pressure-compensated flow control valve. This cartridge valve regulates the fluid flow back to the reservoir
when the valve opens. It allows the table to always lower at the same rate regardless of whether there is a load on
the platform or not.
•
The hydraulic lift cylinders. These are displacement-style cylinders. They have a bleeder valve located at their
top end to allow air to be bled from the hydraulic system.
•
The safety velocity fuse. This is a device that is installed in the cylinder’s hose port. It closes quickly in the event
of a catastrophic hose failure to prevent the lift from collapsing down. The platform remains stationary until
pressure is reapplied to the cylinder.
•
The hydraulic fluid. The system uses HO150 hydraulic fluid. Any anti-wear hydraulic oil with a viscosity grade of
150 SUS at 100°F (ISO 32 at 40°C) such as AW 32 or a non-synthetic transmission fluid is acceptable.
When the platform is to be raised, press the “UP” pushbutton. The motor turns (CW at fan end), and in turning it
spins the hydraulic gear pump. Oil is drawn from the reservoir through the suction filter and into the pump. The pump
pushes the then-pressurized oil through the check valve and out to the lift cylinders.
When the platform is to be lowered, press the “DOWN” pushbutton. The lowering valve opens, bypassing the check
valve and allowing the oil in the cylinders to return to the reservoir. The rate at which the platform lowers is
regulated by the pressure-compensated flow control valve.
o
In the event that the platform creeps down slowly after releasing the “DOWN” control, it will be necessary to
remove the lowering cartridge valve for inspection and cleaning, as follows:
♦
Remove any load from the platform.
♦
Warning: Raise the lift and install the maintenance props. Lower the platform until the lift rests on the props.
o
Remove the nut holding the solenoid coil on the valve stem, then remove the coil, and then unscrew the valve
from the manifold.
o
Inspect the valve for contaminants, and the valve’s o-rings and back-up washers for cuts, tears, or other
damage.
o
With the valve immersed in mineral spirits or kerosene, use a thin tool such as a small screwdriver or a small
hex wrench to push the poppet in and out several times from the bottom end of the valve. The valve should
move freely, about 1/16” from closed to open position. If it sticks in, the valve stem could be bent and will
need to be replaced if it doesn’t free up after cleaning. Blow the valve off with a compressed-air gun while
again pushing the poppet in and out.
o
Inspect the bottom of the manifold’s valve cavity for contaminants.
o
Reinstall the valve into the manifold, tightening the valve with approximately 20 lb-ft of torque.
o
If the platform lowers extremely slowly, or not at all, the cylinders’ velocity fuses could be closing. This can be
caused by air in the hydraulic cylinders.
To bleed the air from the system:
♦
Remove any load from the platform.
♦
Warning: Raise the lift and install the maintenance props.
♦
Lower the platform until the lift rests on the props.
♦
Hold a rag over the cylinders’ bleeder valve (it looks like a grease zirk) and open each valve about 1/2 turn with a
wrench. Oil and air will sputter from the valve – once no air is observed, close the valve.
V
ESTIL
M
FG
.
C
O
./T&S
E
QPT
.
C
O
.
7 of 16